Types of Maintenance
It's well known that billions of dollars are lost each year due to unscheduled downtime and poor asset quality. In a never-ending battle to combat this statistic, organizations implement one of a variety of types of maintenance, often combining two or more. Definitions of the types of maintenance vary across the industry, which can make it rather confusing to differentiate things like preventive and predictive maintenance, among others.
Most types of maintenance fall under two main categories: preventive and corrective. Preventive maintenance is when you proactively initiate tasks and maintenance plans to prevent failures from occurring. In addition to preventing failures, preventive maintenance can have the goal of minimizing the consequence(s) of failure or determining the risk of the failure happening.
Corrective maintenance happens after the failure has occurred. Your team is basically getting the asset back to working order at this point. To clarify, corrective maintenance can be deliberate in the form of a run-to-failure maintenance strategy, which will be discussed below.
Let's examine the most common types of maintenance used across the manufacturing and process industries.
-
Preventive maintenance. Preventive maintenance is an established routine of periodically inspecting equipment, noticing small issues and fixing them before they turn into major problems. The main goal of preventive maintenance is zero downtime. This goal is sought after using three objectives: enhance equipment productive life, reduce critical equipment breakdowns and minimize production loss due to equipment failure.
There are a couple of types of maintenance that fall within the preventive maintenance category. These include:
- Usage-based maintenance, which uses triggers based on the actual usage of each asset. Tracking asset usage with equipment monitors allows maintenance managers to set up a preventive maintenance schedule according to preset parameters.
- Prescriptive maintenance closely resembles preventive maintenance, but it leverages machine-learning software like artificial intelligence (AI) and the internet of things (IoT) to help schedule preventive maintenance tasks.
For an in-depth look at the types of preventive maintenance, how to design a preventive maintenance program, preventive maintenance tools and more, check out the link at the beginning of this section.
-
Predictive maintenance. Predictive maintenance is maintenance that monitors the performance and condition of equipment during normal operating conditions to reduce the likelihood of failures. Similar to preventive maintenance (some people even categorize it as a type of preventive maintenance) and closely related to condition-based maintenance (CBM), the goal of predictive maintenance lies in the name: to first predict when failures could occur and then prevent the failure through scheduled corrective maintenance.
Although many organizations employ both predictive and preventive maintenance (76 percent use preventive, while 65 percent use predictive, according to a recent Reliable Plant survey), there are a few key differences. Most notably, preventive maintenance does not require the condition monitoring aspect that predictive maintenance does. This means predictive maintenance utilizes condition-based technologies like infrared thermography, acoustic monitoring, vibration analysis and oil analysis. Another key difference is preventive maintenance involves inspecting and performing maintenance on assets regardless of whether the equipment needs maintenance (the maintenance schedule is based on a trigger). Predictive maintenance does not.
Below is a chart showing how condition-based maintenance relates to predictive and proactive maintenance. Here, predictive maintenance is one of two sides stemming from CBM: a proactive side that focuses on finding the root cause of a failure and a predictive side that concentrates on the failure symptoms and faults.
For more details on predictive maintenance, predictive maintenance technology and more, click the link at the beginning of this section.
-
Reliability-centered Maintenance (RCM). Reliability-centered maintenance is the process of identifying potential problems with your equipment and determining what you should do to make sure those assets continue to produce at maximum capacity. In other words, you analyze breakdowns to figure out proper maintenance methods and customized maintenance schedules for each individual asset.
Reliability-centered maintenance is sometimes confused with preventive maintenance, but there is one key difference: preventive maintenance isn't selective like RCM, making it less efficient. Since RCM looks at each asset individually, inefficiency is reduced by assigning maintenance tasks tailored to each piece of equipment.
Reliability-centered maintenance uses a general four-step workflow: Choose the asset, evaluate the asset, determine the type of maintenance and repeat the process. Assessment criteria for implementing an RCM program asks seven questions:
- How well should this piece of equipment perform?
- In what ways can this piece of equipment fail?
- What causes each failure?
- What happens when a failure occurs?
- Why does each failure matter?
- What tasks (proactive) should be done to prevent these failures from happening?
- What should be done if a suitable preventive task can't be found?
Click the link at the beginning of this section to read more about reliability-centered maintenance, including how to implement RCM, real-world case studies from organizations that have implemented an RCM program, and more.
-
Total Productive Maintenance (TPM). Total productive maintenance is the process of using machines, equipment, employees and supporting processes to maintain and improve the integrity of production and system quality. The goal of a TPM program is to improve overall equipment effectiveness (OEE) by forming small, multidisciplinary teams to address core areas like preventive and autonomous maintenance, training machinery operators, and the standardization of work processes. Total productive maintenance focuses on all departments within an organization, ensuring efficient and effective use of the means of production.
Total productive maintenance is considered more of a process than a program as well as an operations improvement process rather than a full-blown maintenance program. It's also not a quick fix, as it takes years to achieve a maximum benefit from a high-quality TPM process; however, you can see results immediately.
Total productive maintenance incorporates lean manufacturing and the 5-S System techniques from its internationally accepted benchmark made up of eight pillars: autonomous maintenance, focused improvement, planned maintenance, quality maintenance, early equipment management, training and education, safety, health and environment, and TPM in administration.
Implementing TPM involves five phases:
- Identify a pilot area
- Restore equipment to prime operating condition
- Measure OEE
- Address/reduce major losses
- Implement planned maintenance
Click the link at the beginning of this section to read more about TPM, including the eight pillars of TPM, how to implement it, how to sustain a TPM process and more.
-
Autonomous maintenance. Autonomous maintenance is a maintenance strategy that consists of training operators to continuously monitor their equipment, make adjustments and perform minor maintenance tasks to increase efficiency. This is done instead of dedicating maintenance technicians to perform regularly scheduled upkeep, freeing them up for more significant and pressing maintenance tasks.
Autonomous maintenance has two core principles: to prevent equipment deterioration through proper operation and bringing equipment to and keeping it in "like new" condition through restoration and proper management. This requires operators to master skills such as detecting abnormalities by understanding the machine's components, making improvements, identifying quality issues and figuring out what caused the quality issues.
Implementing autonomous maintenance involves seven steps: increasing operator knowledge, initial machine cleaning and inspection, removing the cause of contamination and improving access, developing standards for lubrication and inspection, inspecting and monitoring, standardizing visual maintenance, and continuous improvement.
For a more in-depth look at autonomous maintenance, how to implement it and how to sustain it, click the link at the beginning of this section.
-
Run-to-failure maintenance (RTF). Run-to-failure maintenance is an unplanned, reactive type of maintenance that's usually a deliberate strategy designed to minimize costs. Organizations may choose to adopt an RTF plan for things like disposable assets (machines with disposable parts meant to be swapped out rather than repaired), non-critical assets like tools, durable assets or assets that aren't subject to wear or are unlikely to fail under normal operating conditions, or assets that show random failure patterns that can't be predicted.
The caveat to RTF maintenance is it requires good judgment. Knowing when to label something a wholesale failure instead of repairing it is part of the skill set that comes with RTF maintenance. It can present some risk since assets are not being monitored, causing the organization to stare down the barrel of unplanned downtime when something breaks.
However, when implemented on the right assets with smart planning for dealing with inevitable failures, RTF can save time and money by not replacing unbroken equipment.
Machine Maintenance and the Human Body Parallel
When it comes to maintenance types, techniques and cost, the primary types of maintenance can be compared with the human body to get a snapshot of the equivalent "body maintenance" task. The table below uses a power-generation asset example and compares it with the human heart.

Types of Maintenance Triggers
Maintenance triggers can be set and used with multiple types of maintenance. Breakdown triggers are used with run-to-failure or reactive maintenance plans. Predictive maintenance uses things like time-based triggers in the form of alerts to try and prevent a failure from occurring. Other triggers that will be discussed include event-, usage- and condition-based triggers.

-
Breakdown triggers. As previously mentioned, breakdown triggers are used with run-to-failure or reactive maintenance programs. When an asset stops working, an alert is triggered, which schedules a maintenance work order to repair the asset and restore it to normal operating condition.
Breakdown triggers typically are only useful when an organization is running a group of low-cost, easy-to-replace equipment and has replacement parts and units in stock which can be readily and easily swapped, minimizing downtime as much as possible. Using breakdown triggers is similar to a cat-and-mouse game; not having to plan for maintenance allows for a less expensive maintenance budget, but it also means you must have spare parts and equipment available at all times, as well as personnel to fix issues. Holding stock like this goes against lean principles like Just in Time (JIT), which are designed to cut down on held stock.
- Time-based triggers. Perhaps the most commonly used maintenance triggers are time based. These are linked to a maintenance planning software like a computerized maintenance management system (CMMS) and alert based on a preset time interval. Time-based triggers are used in predictive and preventive maintenance programs for simple tasks like lubricating gears or scheduling an inspection. For example, when an asset hits a runtime of 14 days, an alert is triggered to have it serviced. Outside of a manufacturing setting, a time-based trigger would be changing your heating, ventilation and air conditioning (HVAC) unit's air filters every three months.
-
Usage-based triggers. Similar to time-based triggers, usage-based triggers rely on a predetermined metric based on the usage of the asset in question, regardless of the time period. Unlike time-based triggers, which are carried out regimentally regardless of the machine's condition, usage-based triggers mean an asset is only getting maintenance once it has completed a specific amount of service.
Just like your car gets an oil change every 5,000 miles, any machine that performs time- or quantity-restricted operations can be set up with a usage-based trigger. Meter readings can be added to a CMMS and used to set alerts when a desired quantity or value is reached. Usage-based triggers are a great way of maintaining equipment subject to irregular timetables and are most often used with predictive or preventive maintenance programs.
- Event-based triggers. Event triggers can be used to respond to and assess equipment or facilities after an event such as a fire or flood has occurred. For example, the need to schedule and perform checks of the electrical system and infrastructure after a flood can be driven by a CMMS, with the system alerting the maintenance team of such tasks. Although event-based triggers happen after an event has taken place, they may not all be directly connected to the event itself. Most event-based triggers act as follow-up checks to an event.
-
Condition-based triggers. Condition-based triggers are employed according to an assessment of an individual asset. The assessment is used to determine whether it's acceptable for the asset to continue running or if maintenance is necessary. This is a more in-depth option because it requires maintenance personnel to have working knowledge of the asset to make an informed decision about its condition.
Equipment condition can be assessed remotely as well. Sensors placed on an asset to monitor parameters such as temperature, vibration and noise can be used as condition-triggered alerts. For example, if a sensor notices a spike in temperature that surpasses a predetermined range, an alert is sent to schedule an inspection.
Modern Maintenance Technology
One of the biggest keys for manufacturers to excel in operational maintenance is to use the data provided by modern technology. To do this, a new maintenance solution is all but required to keep assets, employees and processes organized and working seamlessly.
Technological advances are most prevalent in condition-based monitoring in the form of proactive and predictive maintenance. Under these types of maintenance, technologies like oil analysis, vibration analysis, thermography and motor current analysis can help determine root causes and failure symptoms, seek benefits like machine life extension and early fault detection, and reduce the number and impact of failures.
Today's technological revolution in the manufacturing industry has led to fewer errors and defects, optimized production and reduced labor costs. Automated sensors that can continuously monitor machinery are among the biggest improvements. Not only can they be employed across multiple types of maintenance, but they can also generate a massive amount of data that can be analyzed and used to improve processes.
CMMS solutions can help harness all this data and integrate it with four key aspects for a modern maintenance technology strategy: using predictive maintenance, focusing on data and the IoT, managing inventory, and improving cycles for continued success.

- Using predictive maintenance: While preventive maintenance is a good way to keep you from running to failure and reducing downtime, the next step is implementing predictive maintenance to efficiently gather and analyze the data your machines are generating.
-
Quality data and the IoT: It's important to have a CMMS that can handle the massive amount of data being produced throughout your plant. You'll want to integrate data from basic self-installed sensors to embedded sensors and everything in between. This usually means you should look for a CMMS with an IoT strategy so you aren't married to a single type of hardware.
The IoT is employed to wirelessly integrate data gathered from assets on the plant floor to a CMMS utilized throughout the organization. This will require setting previously discussed triggers and alerts to automatically create work orders without human interaction.
- Managing inventory: A recent Plant Services survey found nearly 29 percent of respondents had a three- to four-week backlog of maintenance tasks. Always taking a reactive approach to maintenance only causes your backlog to grow, which means your assets aren't receiving the proper maintenance they need. Tracking backlogged tasks in a CMMS helps you identify problems, causes and solutions, and leads you to embrace a more proactive culture to reduce backlog.
- Improving cycles: Leveraging data from a modernized plant floor setup and integrating it through a CMMS puts you on a path to improve your maintenance cycle, sustain savings and boost efficiency.
Modern Maintenance Technology Trends
- Industrial Internet of Things: As previously discussed, the internet of things, and more specifically the industrial internet of things (IIoT), is a modern form of automated data collection through the use of a network of wireless sensors. Today, low-cost, multi-purpose sensors are more readily available than ever. They can be configured into different sensor networks on multiple industrial assets and used to automatically collect maintenance data. This eliminates the need for expensive and time-consuming manual data, which is prone to human error.
-
Augmented Reality (AR): Remote maintenance and training are starting to benefit from AR thanks to the ability to offer remote instructions. This customized approach allows maintenance tasks to be customized to an employee's understanding and skill level. Augmented reality can facilitate training provided by an equipment vendor or senior-level maintenance personnel via a cyber presentation that shows how to perform a task.
While still an emerging trend, using AR for training is gaining in popularity due to the increasing complexity of industrial equipment. Augmented reality can ease the burden on maintenance personnel trying to keep up with variations in new equipment, including technologically advanced capabilities that accompany each asset. There are already several vendors who offer large-scale AR solutions for maintenance tasks and IIoT providers who provide AR as part of a bundled package.
-
Maintenance as a Service (MaaS): MaaS is a fairly new paradigm for the maintenance world. It essentially involves delivering maintenance services on demand. With MaaS, a vendor can charge a plant operator according to the maintenance services he/she actually uses instead of a flat service fee. Vendors do this by collecting and processing large amounts of data, storing them via the cloud and scheduling tasks based on this data. Services include:
- predicting the lifetime of an asset or offering insight on optimal maintenance intervals;
- providing service manuals, videos, and virtual reality (VR) and AR interactive support;
- configuring information technology (IT) and other systems within a plant based on analytical results; and
- providing detailed statistics and reports on machinery.
Early stages of MaaS programs are starting to be made available by vendors. ThyssenKrupp Elevators now come with a proactive maintenance program that predicts problems before they occur and notifies the appropriate individuals to perform an inspection. BMW is also planning to take MaaS to the consumer in the near future, offering programs that will let car owners know the best time to have maintenance done on their vehicles.
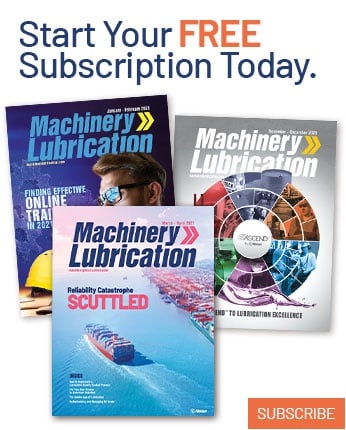