Rope sheaves have always been a frequent cause of maintenance problems. If the sheaves are not running properly, the rope can slip, resulting in rope wear and paper tail tears. Worn ropes can break, requiring unscheduled shutdowns. Lubricant leakage damages the paper, and the need to access hazardous locations for relubrication can be risky for maintenance personnel. For such situations, SKF offer a unique rebuild service that includes the use of component upgrades to make rope sheaves virtually maintenance-free for two years and more.
Another less common but important issue is the danger of sheaves falling off their shafts, causing damage to the product, the felts, the rolls or even worse, people.
Most mills have learned to accept these conditions as normal, and use preventive maintenance to minimize their possible impact. The sheaves are periodically removed and replaced with new or refurbished sheaves, or are simply equipped with new bearings. And still, failures occur during machine startup – when rope sheave performance is critical.
When a well-known board mill was facing such problems, the result was 17 hours of unplanned stops per year because of rope sheave failures. Every year, the maintenance crew needed to replace 30 sheaves, which took four man-hours per sheave. They would typically remove the sheaves, dismount the failed bearing and mount new ones. At €6 000 per production hour and €35 per labor hour, the mill was looking at significant maintenance costs each year.
The critical point was reached when one of the failed sheaves fell off a machine from a height of six meters. The mill contacted SKF and the SKF engineer investigated the unit to establish the cause of failure. The analysis clearly showed that the bearings had failed because of inadequate lubrication and corrosion damage.
For such situations, SKF offers a unique rebuild service that includes the use of component upgrades to make rope sheaves virtually maintenance-free for two years and more. Other benefits include: reduced rope wear; fewer chances of paper breaks; lessened risk of sheaves falling off; and the elimination of grease leakage.
The rebuilt units are equipped with specially greased SKF bearings, which perform well even under marginal lubrication. Both the rope sheave unit and bearings are sealed for life, eliminating the need for grease nipples or lubrication ducts that could leak.
The units are black chromed to resist corrosion, with other coatings also available. And, the addition of a patented security device locks the unit firmly in place and prevents it falling off the shaft, even in the unlikely event of bearing failure.
By replacing the bad performers with rope sheaves rebuilt by SKF, unplanned downtime was significantly reduced, enabling the mill to schedule planned stops for less urgent and routine maintenance. Most importantly, the work floor became a much safer place because of the unique locking facility of the sheaves.
The financial benefits from the SKF solution speak for themselves.
Return on investment (ROI) figures over a two-year period
Savings per machine by avoiding downtime and maintenance: €265 500
Total SKF rope sheave units investment: -€90 000
Total savings: €175 500
Total ROI: 195 percent
Other board mill applications where similar benefits might be experienced using similar SKF technology and knowledge are: locations that are difficult to access, and places where lubrication, humidity and contamination are issues of concern.
To learn more, visit www.skf.com.
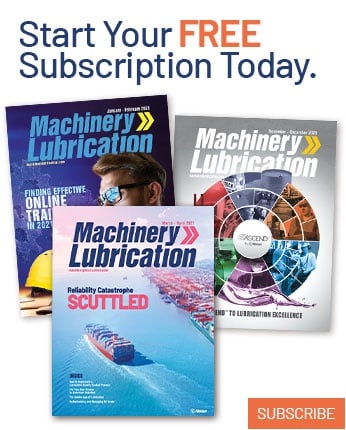