The question of who in an organization should be responsible for day-to-day machinery lubrication tasks is common. With organizations down-sizing or right-sizing, all of the time preparing for the staffing crunch expected or being experienced due to the retirement of the Baby Boomer generation, many maintenance organizations are in a state of flux as they try to seek the most effective and efficient structure to meet the organization's needs and objectives. In my consulting projects, I'm often asked to comment on how I think the "ideal" lubrication department should be structured. Unfortunately, I'm not always able to provide an ideal answer since there are many ways to organize a maintenance team, but here are my thoughts on the pros and cons of the three most common organizational structures.
The classic lubricant department model: The classic lubricant department is how many companies have traditionally staffed their lubrication needs, and many continue to do so today. In this model, one or more full-time, dedicated lubrication technicians are responsible for lubricating some or all of the plant's assets, reporting either to a lubrication or maintenance supervisor or directly to the maintenance manager. There are some real benefits to this type of approach, not the least of which include the ability to build, train and develop a team exclusively dedicated to the task of lubrication.
With the right choice of individual - someone who is properly trained and motivated - there is no reason why this approach can't work today, as witnessed by many companies who are succeeding with a classic approach to lubrication staffing.
However, history has proved many downsides to this approach. For example, many companies continue to under-value the contribution the classic lube tech plays in helping maintain the plant's assets. Faced with the old thinking that "if you know your way around the plant and can find where the grease guns are kept, you can lubricate," many companies insist on making the "lube crew" a home for unmotivated workers - those who are either incapable of functioning in other trades at a high enough level, are close to retirement and "opt" for the lubricator job based on a perception that the job is easy, or are on medical disability from other more strenuous jobs.
Done properly, lubrication is a fast-paced, skill-rich activity, which - though perhaps not on par with higher-skilled maintenance tasks such as rebuilding machines or performing vibration analysis - requires an individual with certain hard and soft skills coupled with a desire and motivation to serve the plant through lubrication best practices. I have met many lube techs who fit into this category in my career, and they deserve our respect and support for fighting for what they know and believe to be right. Unfortunately, I have also met many who simply are biding time until retirement, punching the clock or are flat-out lazy - none of which help in the "classic" lube tech model.
The multi-skilled maintenance mechanic model: Some companies choose to deploy maintenance mechanics to perform lubrication as part of a multi-skilled workforce. Faced with increasing staffing costs, the belief is that more efficient use can be made of the maintenance team if they are able to perform in all major areas of maintenance, lubrication being just one discipline. Again, there is no reason why this approach can't work. Most mechanics have a significant level of experience with different types of machinery. They typically have more training and knowledge than most lube techs and the ability to not only perform the required lubrication tasks but to complete other tasks at the same time. It certainly can make for more efficient work planning and execution.
Again, the downside to this approach comes not from the philosophy, but from the execution. In many plants where this model has been adopted, mechanics sometimes place a bigger emphasis on seemingly more important maintenance tasks (rebuilding equipment, replacing bearings, etc.) than lubrication tasks, even though some of the non-lubrication tasks are necessary due to poor day-to-day lubrication practices! This pressure to deprioritize sometimes comes from managers or supervisors. But more often than not, it comes from a misguided belief that lubrication requires less skill and is, hence, less important than other tasks that are perhaps more interesting and enjoyable to a skilled millwright or machinist.
Just like the "classic" model, provided that the organization takes a properly balanced approach to lubrication and its role as part of other precision maintenance tasks, there is no reason why this multi-craft skill approach can't be successful.
The operator-assisted lubrication model: With as many as 43 percent of U.S. companies adopting some form of lean manufacturing, companies are increasingly entrusting some or all of their maintenance tasks to operators, including lubrication. Just like the previous two models, there's no reason why autonomous maintenance, operator-assisted maintenance or Total Productive Maintenance - whatever you choose to call it - can't work for lubrication. Where companies go wrong is in expecting operators to function at the same level as a lubrication technician or maintenance mechanic without providing the training, knowledge and process to allow operators to function at that same level. Done properly, TPM and all of its embodiments can and do work. But when operators are simply given a grease gun or oil can and told to "go lubricate," TPM will always stand for Typically Poor Maintenance.
So, you see, there really isn't a right or wrong way to staff the lube department. Whether you're a proponent of the classic model, multi-craft model or operator model, the key is to: 1) build a system and process that supports and promotes lubrication best practices; 2) train and educate those involved; and, 3) insure that no matter who is responsible, that person or persons understand the vital role that precision lubrication plays in delivering plant reliability.
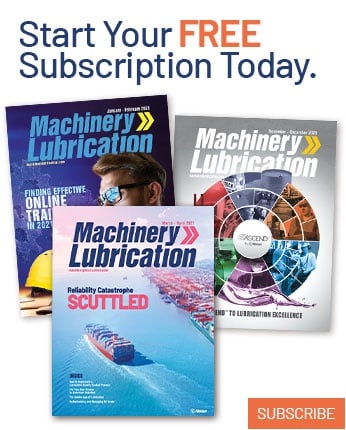