For a busy aircraft components manufacturer that is milling and turning short runs of precision parts, shorter cycle times and quicker tool changes mean greater profitability. Crissair Inc. in Palmdale, Calif., turned to tool supplier Sandvik Coromant to help cut milling time on one alloy steel hydraulic body 63 percent. The success led to a broader Productivity Improvement Program that identified some $87,000 in potential annual savings, and ultimately to a huge $600,000 payoff by introducing a quick-change modular tooling system.
Crissair has produced precision fluid control components for civil and military aircraft since 1954.
“We have manufactured our products for nearly every airframe manufacturer and major subcontractor in the industry,” says general manager John Semione. “Crissair prides itself in its flexibility to design custom valves to meet specific customer requirements. Because we have design, manufacturing and test capabilities within our facility, we can create and quickly deliver various types of valves to meet any particular customer application.”
Components are machined from 17-4, 15-5 and other alloy steels, 300 Series stainless, Inconel, titanium, and aluminum. The company has developed more than 10,000 proprietary designs for its customer base, of which 3,500 are still active.
“Since most items are produced in short runs of 15 to 30 pieces, short cycle times and fast changeovers from one part to another are essential to profitability,” says Semione.
Milling cutters
One common series of hex-shaped hydraulic components includes sizes from 0.2 inches in diameter by 0.3 inches long to 3 inches in diameter by 18 inches long. The 15-5 alloy steel material is milled on the face and outside diameter to +/-0.005 inches on the hex dimensions. Finishes must be held to 100 microinches or better. Orders for the most popular sizes are 400 to 500 parts a year.
“That’s a big run for us,” says Crissair machine shop manager Larry Moore.
However, cycle time on one of the larger fittings was nearly 20 minutes on Fadel CNC milling machines using end mills with conventional carbide inserts.
“To improve our overall productivity, we wanted something to speed up those milling operations,” says Moore.
Discussions with Sandvik Coromant field representative Martin Morris resulted in trials of the Sandvik CoroMill 390 milling cutter with grade GC1025 carbide inserts. The CoroMill end mill is designed for high-speed machining with less runout than comparable tools. The fine-grained carbide inserts with their titanium nitride coatings are optimized for cutting stainless steels with a fine finish.
“The sharp cutting action and wear-resistant coating made 1025 the best insert for that particular job,” says Morris. “Together, advantages of the new tooling and inserts enabled us to reprogram the machine to run the parts faster and increase feeds. That pays off in greater productivity.”
Machine speeds and feeds using the original end mill and inserts were 2,300 rpm and 8 ipm. The CoroMill 390 enabled operators to run the same parts at 5,000 rpm and 60 ipm.
“We saw a massive increase in material removed by our Fadels,” says Moore.
Cycle time for the large hydraulic component fell from 20 minutes to 7.5 minutes. As a bonus, the milling operation that once required costly coolants could now be run dry.
Productivity program
The tooling success in the milling operations led Crissair to consider changes in its turning cell with four Okuma and Ikegai CNC lathes. Sandvik Coromant productivity teams conduct several hundred such Productivity Improvement Programs a year without any cost to manufacturers. The partnerships typically boost plant-wide machining throughput 20 percent and generate significant savings in machining time and maintenance, repair and operating costs. In the Crissair facility, Morris was joined by productivity team leader Mark Smith and two more Sandvik team members.
Time is money
The Productivity Improvement Program started with a thorough audit of cycle times and machining data in Cell One. With the existing cutting inserts, one part-off operation on a stainless steel hydraulic body required 26.1 seconds. Surface speed was just 100 sfm and the feed was 0.0015 ipr. With a switch to Sandvik’s Grade GC2135 inserts, machine operators more than tripled speed to 325 sfm and increased feed 2.3 times to 0.0050 ipr.
The toughened carbide is made for cut-off to center jobs. Cutting time per component fell from 20 seconds to less than 2 seconds. With non-cutting time unchanged, overall cycle time fell 70 percent, from 26.1 seconds to just 7.86 seconds. The cumulative savings in time and tools cut machining cost per component 56 percent. Over a typical annual run of just 145 parts, savings would amount to $73.16.
In a finishing operation on the outside diameter of a stainless steel connector body, cutting time with a conventional carbide insert was 26.4 seconds. The productivity team recommended changing to Grade 2015 inserts to increase feeds and speeds. The heat-resistant carbide and tenacious coating make the inserts especially well suited to turning stainless steel. Increasing surface speed from 164 to 262 sfm and feed per revolution from 0.0025 to 0.0050 ipr reduced cutting time 68 percent to just 8.28 seconds. In addition, the advanced carbide insert increased tool life three-fold, from 25 to 75 pieces per edge. Total machining cost per component was cut by 61 percent, and overall savings on an annual run of 200 parts were $70.89.
Though the savings on individual part runs were small, their cumulative value was significant. The Productivity Improvement Program identified potential savings totaling $87,797 over a full year from all the operations in Crissair Cell One.
Sandvik representatives provided training for Crissair machine operators to implement the changes smoothly.
“The group that came out here was professional and knowledgeable,” says Semione. “The training they provided really helped our machining process.”
Quick change tooling provides windfall
As the productivity changes were implemented, Semione asked Sandvik Coromant representative Morris, and local Sandvik supplier Phil Canipe from BC Tooland Carbide, about modular tooling to improve job changeovers.
“We do a lot of short-run jobs,” explains Semione. “Setup time is a real cost driver. If we amortize the cost of setup over just 15 parts, it becomes a significant factor.”
Soon after, Morris and Canipe made their recommendations for Crissair to evaluate the Sandvik Coromant Capto modular tooling system and developed a training program to maximize Crissair’s return on investment.
Capto quick-change tooling uses a tri-lobed coupling to create an extremely stable joint. The self-centering coupling has a pre-tensioned joint interface that develops several tons of clamping force. A quick turn on an Allen key releases and reclamps the holder with 0.000080 inches of repeatability, radially and axially. The modular holder enables machine operators to replace tools quickly and return them to accurate cutting positions. It also eliminates hit-or-miss adjustments and costly scrap on setup.
Changeover on their CNC lathes was typically a five- to six-hour job.
“We were using old drill holders with blocks and bushings, and the whole thing was very time consuming and very imprecise,” says Moore. “First, you have to find a drill and bushing to go in that holder, then put them in and use a microscope to get the location to program the CNC.”
Capto tool holders eliminated both the hunt for bushings and the painstaking adjustments to center each tool.
“We easily cut our changeover time in half,” says Moore. “Our target is now two hours or less.”
Semione adds, “We have found that if we really focus on a job and have all the tools prepared up front, we can set up most jobs in under two hours. Our goal is to average less than one hour and have modular tooling on each CNC lathe.”
The annual cost savings realized by using modular tooling is more than $600,000.
“The recommendations and training have made us more competitive and profitable,” he says.
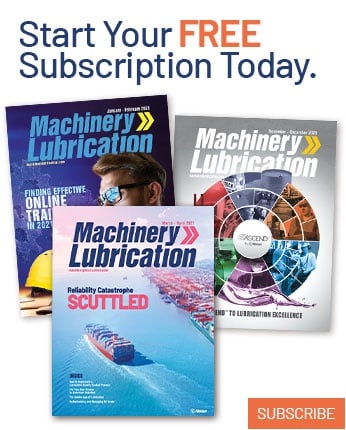