In aerospace projects, there are no “do overs.” Even minor errors can prove expensive or deadly. NASA's $125 million Mars Climate Observer burned up in the Martian atmosphere when the manufacturer gave NASA English measurements for thrust, rather than the metric units NASA was used to. A loose piece of foam cost seven shuttle astronauts their lives. But careless mishaps also take place on the manufacturing floor.
In 2003, for example, the U.S. National Oceanographic and Atmospheric Administration's $233 million NOAA-N Prime weather satellite was severely damaged by falling three feet to a concrete floor at Lockheed Martin's satellite factory in Sunnyvale, Calif. When one crew failed to document that it had removed two dozen bolts from a cart used to turn the satellite over, and the other crew failed to follow procedures and check if the bolts were in place before moving the satellite. The end result was a $135 million repair bill.
Missing bolts, then, can certainly be a problem. But so are over- or under-torqued bolts and rivets.
That’s why Six Sigma black belt Vu D. Pham of Boeing took on the task of improving the accuracy of the torquing at his plant. Along the way, he not only improved the accuracy, but by using a PDA-based calibration verification system from Mountz Inc. of San Jose, Calif., he also found a way to save the company a lot of money.
“We calculate that real savings for the first year was a couple hundred thousand dollars,” says Pham, leader of engineering assurance at Boeing's Satellite Development Center (SDC) in El Segundo, Calif. “This is just the raw savings of not sending tools out for calibration, and doesn't include our savings on failures, repairs and personnel costs.”
In December 2006, Boeing Space and Intelligence Systems (S&IS) was named as one of the two Gold-level recipients of the California Awards for Performance Excellence (CAPE), the statewide equivalent of the Malcolm Baldrige Award (SDC is a part of S&IS).
Calibration Conundrum
Boeing's SDC is the world's largest satellite manufacturer, with more than 200 commercial communication satellite launches since 1963, in addition to military and weather satellites and spacecraft. The SDC's million-square-foot manufacturing facility has more than a dozen satellites under construction at any given time, primarily its 601 and 702 series of body-stabilized communications models, as well as two lines of mobile communications satellites. Pre-launch testing includes subjecting them to spin rates of 30 to 100 RPM, as well as vibrations and sound similar to what they would experience during launch (up to 50,000 pounds of force and 165 decibels).
To test their ability to withstand the rigors of space, they are placed in a thermal vacuum chamber and subjected to temperatures of minus-320 degrees to plus-250 degrees Fahrenheit while powered up and with instruments operating.
The facility has received both the Software Engineering Institute's Capability Maturity Model Integration (CMMI) Level 5 (Optimizing) certification and the Aerospace Standards (AS) 9100 Certification. AS9100 consists of the ISO 9001:2000 standard with additional aerospace specific requirements. Part of the SDC's quality control program, for example, is complying with ANSI/NCSL Z540-1-1994 calibration standards.
“To meet those requirements, a torque verification system has to include maintaining the history of each torque and the calibration data,” says senior calibration engineer William K. Jinbo. “A quality control person would actually monitor the whole process of the bolt torquing from the beginning of obtaining the wrench to the very end after the torquing is done. Then they would have to maintain the data and history of the torque.”
It also meant that each torque tool needed to be sent outside for calibration, an expensive proposition considering that SDC has 3,500 torque tools.
“I had a task to improve the quality of the torque tools that were causing the over-torque,” says Pham. “To achieve this, we first had to conduct a study of root causes using the standard Six Sigma tools. This entailed looking at the people, systems, processes and methods as well as the torque tools themselves.”
One thing that Pham and his team looked at was whether the gages were properly calibrated or were the culprit. They conducted a study of repeatability and reproducibility and found that the tools were out of calibration, some by as much as a factor of 1.5 or two. This was despite the tools being sent to a third party for calibration.
But even though they were within tolerance, they were still subject to operator error. The tools were spring-loaded and different operators would pull it different amounts after hearing the click. The solution that was in place to rectify this issue was to have an inspector standing there also listening for the click to ensure the component was not under- or over-torqued. But even this wasn't consistent.
Then there was the issue of usability of the tools.
“With some of our tools, we could not change the torque values quickly enough, so we use different tools for different torque values,” says Pham. “That is why we went looking for what else was out there that we could use.”
Three-Phase Improvement
Based on the initial evaluation of problems with the existing torque system, Pham and his team began a three-phase project to address the issues found. Phase one was to locate tools that were more accurate and consistent than what they had been using. They investigated several manufacturers. Pham's boss, director of engineering quality Dan Pace, had worked with Mountz tools at a previous company, and recommended that they be considered.
“We found that the Mountz tools could produce repeatability and reproducibility,” says Pham. “We tried them with different operators and different values, and they came very close to Six Sigma values.”
While that alone would have made a significant improvement in operations, that wasn't enough. That led to phase two: ensuring the tool was accurate every time, not just after the annual calibrations.
“Even though the tool is good, what guarantee is there that if it is dropped it will still be calibrated?” says Pham. “So, I challenged the vendor to come up with a portable calibration system that we can bring to the point of use and test the tool before we use it. That way we will know if the values have shifted.”
The supplier came back to Boeing with a laptop loaded with the verification software, but Pham
rejected that solution as being too cumbersome to work with in the confined spaces around a satellite. So, at Pham's request, a PDA-based version was developed, mounted on the tool cart. This met Boeing's requirements. The final system consisted of:
● 12 Mountz Wizard PLUS PDA handheld torque displays/calibration systems
● 27 Mountz BMX torque sensors
● a large assortment of Mountz specialty cam-over and break-over wrenches and screwdrivers
“We greatly appreciate the partnership we had with Brad Mountz in developing this system,” says Pham. “He is willing to listen to the customer and put forth the effort to develop the PDA system. The technical support team was excellent.”
With the proper tools, Pham could now concentrate on phase three – the people and processes. Utilizing the above calibration system, the tools were verified right on the shop floor every time they were used. The software in the PDA also recorded the calibration test and the information on the torque being performed, so the data was there for audit and verification purposes. The end goal of the third phase was to get this process validated as a replacement for sending out all the tools for calibration and having an inspector witness each and every torque.
“We can verify at the point of use, prior to installing something, that we have a good value,” Pham says. “My communication to the calibration department was, if we can do this here now, why should we send these tools out for calibration? It doesn't make sense.”
After some back and forth it was determined that Boeing could meet the NIST calibration requirements in house. Instead of having to send out all the thousands of tools for calibration, only the Mountz equipment needed to receive third-party testing.
“The only thing we have to send out is the torque sensor and the Mountz PDA for calibration – five pieces instead of thousands,” he says.
Reproducing Success
Jinbo admits that he wasn't sure in the beginning whether the system would work.
“I was first of all fairly skeptical about being able to have a torque verification system at the point of use,” he says. “Several factors determine the accuracy including the actual person doing the torque and whether he or she has the right technique. If they don't have the right technique, that will create a problem as far as torque is concerned. But, after seeing it in action, he is pleased with the results and says the system has also gotten a positive response from the technicians who use it.
“The main reason for it being on the floor is to have confidence in the level of torque before the torque is done. It makes it easier for the technicians and they don't have to worry about broken bolts from over-torquing or not applying enough torque.”
It has been about two years now since the SDC moved its calibration in house. In the meantime, Pham has been promoted and moved on to other projects. Currently he is developing and establishing a strategy to bring the quality of the engineering functions up to or beyond those of operations.
“You need to focus on the black belt tools – repeatability and reproducibility and having the right tools,” says Pham. “The key point is don't just accept things the way they are. When I have a project, I always push my engineers and challenge them to do better.”
About Mountz Inc.
San Jose, Calif.-based Mountz Inc. produces a wide variety of torque tools, including torque analyzers, torque testers, torque sensors, torque wrenches, electric screwdrivers, torque screwdrivers, torque multipliers, assembly tools, screw counters, balancers and special torque applications. For more information, visit www.etorque.com .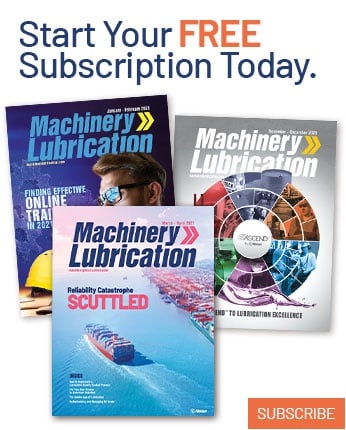