Maintenance is a business within the manufacturing business. In many cases, maintenance costs are among the three largest expenses for a manufacturer.
All of the fundamental systems involved in the maintenance business must be in place and functioning.
Maintenance managers must make decisions that will yield greater maintenance efficiency and profitability.
As indicated in the graph at the bottom right, the cost of condition-based, predictive maintenance (PdM) can reach a point of negative return. The cost of PdM must always be weighed against the benefits. The cost-to-benefit ratio for PdM can vary based on the process. For example:
-
What is the cost per minute of process downtime?
-
Can the process be backed up? Is it in cycle time?
-
Will a process failure cause safety concerns?
-
What failure modes will the predictive tool forecast?
-
Are these historic failure modes?
-
What resources are needed to collect predictive data?
This simple method of determining the cost-to-benefit ratio will help in making short-term decisions. But if we are to be competitive in the business of maintenance, we must go another step further and ask the longer-term questions like:
-
How can I apply PdM tools in a cost-effective manner?
-
How can we build a predictive tool into a machine’s controls?
Maintenance should not allow the process of answering these questions to stop because we can’t afford the predictive tools today. The potential for efficiency and cost savings in maintenance that predictive tools possess should be an incentive for us to find a way to collect the required data and develop predictive tools that are affordable, and cost- effective. No one argues that the future of the maintenance business is the application of condition-based, predictive prognostic tools.
Maintenance business leaders will never stop their quest to eliminate reactive, breakdown maintenance. Reactive maintenance has costs associated with it that go beyond simple downtime costs:
Spare parts: A strong predictive program allows for only a just-in-time spare parts inventory.
Morale: Breakdown maintenance is stressful and fatiguing.
Safety: Breakdown maintenance results in more injuries (per hour worked) than planned maintenance.
To be maintenance leaders, we must never stop moving toward smarter, cost-effective maintenance systems.
Dr. Jay Lee is the Ohio eminent scholar in advanced manufacturing at the University of Cincinnati. He formerly served as the Rockwell Automation professor at the University of Wisconsin-Milwaukee and was director of product development and manufacturing at United Technologies. He is also the founding director of the Center for Intelligent Maintenance Systems, a National Science Foundation initiative that's developing technologies to enable machines to achieve near-zero breakdown performance. CIMS partners include Rockwell, Toyota, GM, Harley-Davidson, DaimlerChrysler, Ford and Siemens. Contact Dr. Lee at jay.lee@uc.edu. |
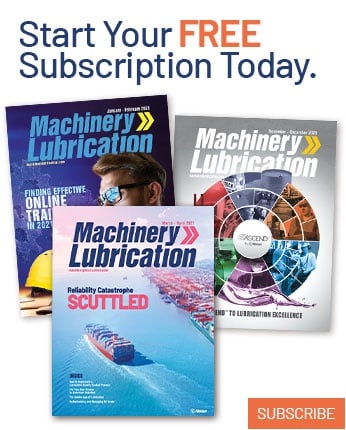