The Reliability in Action department features case studies submitted by our readers. To have your case study considered for inclusion in an upcoming issue, e-mail it to parnold@noria.com or mail it to Reliable Plant, P.O. Box 87, Fort Atkinson, WI 53538. If we publish your case study, we'll send you an official Reliable Plant T-shirt. Here's this issue's contribution:
The company: The Nebraska Public Power District (NPPD) is the state's largest electric utility, with chartered territory in 91 of Nebraska's 93 counties. To meet the needs of 1 million customers, NPPD incorporates several generating plants, 5,000 miles of grid lines and 2,100 employees.
The challenge: NPPD routinely shuts down its nuclear power plant near Brownville, Neb., every 18 months. Each outage costs $25 million in materials and work performed, in addition to $10 million to $15 million in lost revenue. With each day of a shutdown resulting in $450,000 in lost revenue, NPPD strives to accomplish a shutdown in less than 25 days. A typical shutdown involves a total of 12,000 operational activities, and requires 1,500 workers occupied in as many as 500 daily tasks.
In order to manage the intricate schedule of activities during shutdowns, as well as regular daily maintenance, NPPD uses Primavera and SAP. The utility has used Primavera since the 1980s, taking advantage of its scheduling flexibility and reporting functionality. It uses SAP to control financial data and the work management process.
In preparation for a scheduled plant shutdown, project managers and schedulers must transfer 12,000 tasks and their dependencies from SAP and turn them into complete project plans and schedules in Primavera. By providing customized reports and critical path analysis, Primavera provides NPPD management with the tools it needs for high-level decision-making.
The two disparate systems made project management cumbersome and time consuming. Both solutions are effective in their separate tasks, yet there was a lack of control in the transfer of large amounts of data between the systems. Employees were unable to produce accurate reports, which disrupted schedules and led to prolonged project times. As a result, NPPD determined that it needed help to effectively transfer project data by bridging Primavera and SAP.
"During our last planned outage, the lack of integration between project schedules, the resources needed to deal with two schedules and the resulting outage delays contributed to significant cost overruns," said NPPD assistant to the plant manager Mark Gillian.
The solution: To solve its integration issues, NPPD turned to Impress for EPM, a packaged integration application optimized for bridging Primavera with SAP. It synchronizes project-related data between the systems, automating the costly and time-consuming data entry required to keep both systems consistent. It also keeps key SAP information, such as resource and material availability, in sync. As a result, project managers working in Primavera can improve their effectiveness during project planning, scheduling and execution for shutdown activities. Impress also aids NPPD in ensuring its Primavera schedules are aligned with the data in SAP for the planning of daily maintenance activities, helping reduce the frequency of forced shutdowns.
The benefits: The integrated solution helped NPPD cut weekly scheduling man-hours in half by eliminating manual entry, downloads and imports of the activities required to keep both systems consistent. It also improved schedule adherence and accuracy by allowing staff to build schedules based on real-time data. Using Primavera's role-based functionality, the number of people able to change the master schedule could be limited, thereby providing the project manager with more control and ensuring the accuracy of the schedule. Employees now can make confident decisions, knowing that the information provided is reliable, complete and current.
Daily maintenance helps protect against unplanned shutdowns, but when an outage occurs, every minute counts. The ability to generate real-time schedule, cost and resource data from an integrated system lets NPPD management rapidly respond and get the plant up and running again quickly.
The results: Bottom line, this solution:
-
saved more than 100 man-hours per week in schedule development and maintenance time
-
reduced outage duration, minimizing costs and lost revenue
-
improved response time to outages
-
improved accuracy of schedules
-
eliminated duplicate data entry
-
maintained consistent dates and task relationships in Primavera and SAP.
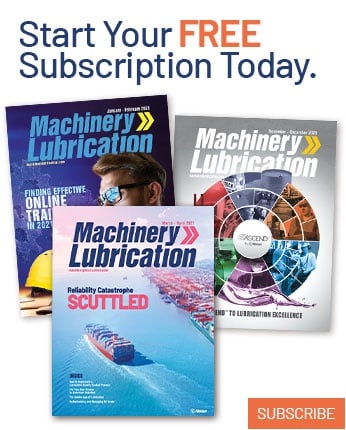