This afternoon, we completed another successful kaizen five-day event at an aerospace company in Indiana. The team was outstanding, the results were excellent and the kaizen event process was far from perfect, really meaning our kaizen implementation.
Taking a page out of the military handbook, let’s look at this kaizen event for lessons learned. Our military has long utilized the process of debriefing, or a “hot-wash” from what I have been told, to examine the lessons learned on the battlefield or training session for improvement and evaluation, providing a critical review of one’s action. Here’s what I learned from this kaizen event.
Lesson 1: Keep the kaizen training to what is actually needed for the event.
I learned this lesson long ago, abandoning the idea of packing as much training into the event as possible to increase value to the participants. It makes absolutely zero sense to go into the details of a SMED system (single minute exchange of dies) if your event has no changeovers as an obstacle to improvement.
Yet, I have attended kaizen events where the training package was a canned program for the full day, regardless of the scope of the kaizen event. Our kaizen event this week concentrated on throughput to the customer, so the training was only a half-day focusing on seeing waste, standard work and process flow. I spent too much time on some of the tools, time observation for one, which could have shortened the training time by 30 minutes.
Lesson 2: Provide the kaizen training at the right time.
Many kaizen event training programs spend valuable training time the first day teaching how to complete a report out on Friday. By the time Friday rolls around, they end up teaching this portion of the training all over again because everybody has forgotten the lesson during the week.
Sounds like muda (waste) to me. I only mention the report out on Monday morning, leaving the details for Friday morning prior to the report out. When Friday arrives, I bring the team together for the quick "How-to-do-a-report-out" session, and then the team goes to work without many questions. I think I did a good job on this one.
Lesson 3: Properly scale the scope of the kaizen event.
How many kaizen events bring an elephant to the table for a small team of five people to try to eat in one week? Although we love a challenge and admire a team that tries to tackle a huge project, the size of the scope matters.
Keep the scope in line with the resources at hand. Our project was huge, covering more than 30 process steps that encompassed more than 10 days of well-documented cycle time to complete one unit. It would have been impossible to cover all this work, so we focused only on the waste in between these steps, walking and waiting. This scale could have been examined in more detail prior to the event.
Lesson 4: Measure twice, cut once.
After training on Monday at 12:30 p.m., our kaizen team was ready for action. Time to go to gemba. With data collection activities through Tuesday afternoon, the team had a workable layout ready for maintenance support by 2:30 p.m. A flurry of activity, with equipment moves and scouring the area for our needs, leads us to a transformed work area by 6:30 that night. Maintenance started without haste hooking up the new air and electric drops. The new layout was a tremendous improvement. Hurray!
But wait, the team started coming up with more ideas to try out. We asked the maintenance crew to hold up a bit while the team discovered the process of conducting multiple experiments to find the optimal layout. Only five layouts later, the team was satisfied with the results.
Each of the five layouts shortened the distance traveled in the process, gaining an extra 5 percent improvement. Luckily, only a few of drops had any significant changes, so we did not completely tick off our wonderful maintenance support crew. Do not become satisfied with Idea A without trying multiple solutions (ideas B, C, D, etc.). You just might find a better way. Then, call in the maintenance troops to action.
Lesson 5: Do not tick off your maintenance support crew.
Please see above.
Lesson 6: Pick the right lean tool for the job and use it well.
There are plenty of lean tools to choose for kaizen activities, so you must determine the right tool and use it well. In our case, the spaghetti diagram was the best tool. It was simple to use although extremely time-consuming for the large amount of travel in our process. The spaghetti diagram quickly showed the team the best areas for opportunity and was a great visual for comparison of layout options. Some of our time observations on the first day did not end up providing much help with our focus on the in-between process wastes.
Lesson 7: Buy-in, Buy-in, Buy-in.
Without the buy-in of the operators in a new process, the improvements of the week will not last past the Friday report-out. It is critical to get the process owners to buy-in to the new process. Of the five team members, we had one operator and one team leader of the process. All the other operators were asked for input and involved in the process of determining the layout each step of the way.
Even with this high level of involvement, we had some unhappy campers. It took plenty of “please try it” and “what do you think?” before all the concerns were addressed. Several changes were not completely understood by those it affected, and several detailed changes were not discussed outside of the team before we made them. It may take patience and effort on the part of the team to get buy-in. To be successful, you have no other choice!
Lesson 8: Watch out for collateral damage.
Our new layout had a ripple effect. We took over an area belonging to another process and ended up swapping areas with them. We had a layout for our area but not one for the ousted department. We moved our equipment around our plan with precision and piled up the other department’s workbenches into our recently vacated area with reckless abandonment.
Although we did provide air and electric to keep them running production the next day, they were not too happy with our thrown-together layout. We ended up spending time the next day fixing the mess we left behind. The end result was a much improved process flow for both areas; however, we should have spent some quality time on the layout of the other area up front.
Lesson 9: Keep your kaizen goals simple.
Many times, a kaizen event will put a long list of targets or goals on the team to accomplish – productivity, cycle time, 5-S, floor space, quality, etc. All these goals are noble and beneficial; however, they may leave a team running in too many directions. Pick one goal to focus your kaizen team. Our kaizen goal was to improve the throughput of the process to the customer. We measured this goal with 1) time and 2) distance. Clear, simple and measurable. Good job!
Lesson 10: Go to gemba and stay there the entire week.
With the exception of our Monday morning training and eating lunch, our kaizen team remained in our kaizen area the entire week. We had a meeting table, a few chairs and a flip chart placed in our kaizen area sharing information with the area (along with all those that passed by) throughout the kaizen process.
Not only did this remove the muda of walking back and forth to an off-site meeting room, it also limited the team debates on the actual process. We shared information on display with our kaizen newspaper for all to see. No secrets, nothing to hide. Even the daily team leader meeting and the final report-out were conducted at gemba.
In fact, our Friday report-out was attended by the owner of the company and his entire staff along with interested management from other departments seeing the actual improvements at gemba instead of relying on just descriptions of the changes in a stale conference room. Have the final report out at gemba; it will have a huge impact!
As stated earlier, the kaizen event results were excellent. We reduced the customer lead time in days by 36 percent and shortened the distance traveled by 68 percent (from more than 6,800 feet to 2,199 feet). The spirit of kaizen was ignited at this company and they are ready for more!
Can the kaizen process be improved? Absolutely!
About the author:
Mike Wroblewski started his lean journey with instruction in quick die change from Shigeo Shingo. Mike is president of Victory Alliance Technologies, a Greensburg, Ind., firm that specializes in lean implementation. He writes a blog called " Got Boondoggle?" featuring lean and Six Sigma topics. Mike can be reached by e-mail at mwroblewski@victory-alliance.com.
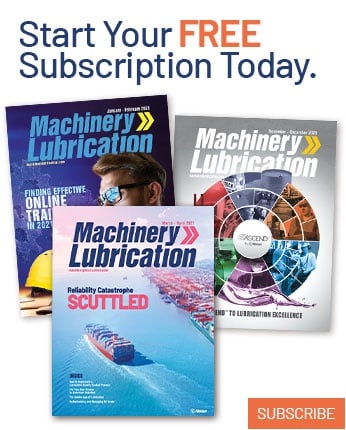