Process improvement is the act of analyzing and improving existing processes. Below we discuss process improvement methodologies, how to get started and more.

What Is Process Improvement?
Process improvement is the ongoing process of identifying, analyzing and improving current processes within an organization, ensuring your business is operating at optimal levels to meet standards, quality benchmarks and quotas. While it usually follows a specific methodology, there are different approaches to process improvement, the most common being a variety of lean manufacturing techniques that each focus on specific areas of improvement. During a process improvement analysis, processes can be modified, added to by using sub-processes or eliminated if deemed unnecessary.
What Is the Purpose of Process Improvement?
Process improvement can be likened to trying to get into better shape; you might start by researching a diet plan and finding a gym or trainer to help you nail down a workout routine. At first, it's easy and exciting to make this change in your life as you start losing weight, feeling better and noticing some real changes. Then, you slowly start slipping into your old ways; you sleep in one morning or eat fast food for lunch a couple of times a week. Gradually, you fall back into your old habits.
Process improvement can follow a similar pattern; you analyze your current processes and come up with an idea that could potentially improve your organization in multiple ways. Your plan gets approved, and the changes are implemented. Soon, you notice everything is falling back into the old way of doing things.
This is why process improvement is important; without an actual standardized process improvement plan in place, changes will quickly drop off. Process improvement strives to identify and eliminate weak points in your organization. Eliminating weakness helps your business in several ways, including:
- improving the efficiency and quality of processes (removing redundant tasks),
- reducing process completion time,
- getting rid of the multiple types of waste and
- identifying broken processes.
Managing change is part of process improvement implementation and is a difficult task. It's essential to have direction and well-defined rules to see results in a process improvement plan. These rules might include things like:
- analyzing existing processes and their current roles or function in the organization;
- identifying broken processes and either eliminating them or deciding how they could better align with the company's overall goals;
- defining how improved processes might add value to the overall operation; and
- reorganizing available resources like information technology (IT), plant-floor operators, systems, etc., to execute process improvement effectively.
What Are the Lean Process Improvement Methodologies?
There is no single lean process improvement methodology that works for each organization's process improvement plan. In fact, there are several techniques designed to identify issues within a process, fix them and analyze the results of the fix to see how it improved the process or if it failed.
While every methodology has a common goal, each may help you with a different need. For example, some focus on lean process improvement techniques, while others deal with the task of getting your company culture in the right headspace for process improvement. Let's take a look at some of the most widely used lean process improvement methodologies.

-
Lean manufacturing: Lean manufacturing or the process of going lean refers to a series of methods, philosophies and tools to minimize waste within an organization and maximize production. Many of the methodologies associated with process improvement are centered around lean manufacturing.
Going lean starts with looking at your processes under a microscope to determine ways in which you can eliminate the eight types of waste: defects, overproduction, waiting, non-utilized talent, transportation, inventory, motion and extra processing. Within lean manufacturing are multiple methodologies used directly for the purpose of process improvement.
-
One of those techniques is kaizen. A Japanese term translated to mean "change for the better," kaizen is a mindset that has teams constantly working together to make incremental improvements in the manufacturing process. The kaizen philosophy emphasizes the importance of each individual's idea and that all employees be involved in process improvement.
Lockheed Martin, an American aerospace, defense and security company, implemented kaizen methods to improve multiple processes throughout the organization. During the mid-1990s, Lockheed Martin was able to reduce its manufacturing costs and lower its defect rate to just 3.5 defects per plane. The company also cut its order-to-delivery time nearly in half, from 42 months to less than 22 months.
- Another lean technique used in process improvement is the 5-S system. The 5-S system is a set of principles designed to eliminate waste and foster a workplace culture of efficiency. The five "S"s translated from Japanese mean, sort, set in order, shine, standardize and sustain. Implementing the 5-S system has organizations sorting all material to determine the necessity of each; organizing necessary items so they're easily found; cleaning workspaces and equipment as well as maintaining that level of cleanliness; developing standards for the first three "S"s and creating rules for how and when tasks will be done; and making the new processes the new normal by conducting audits periodically.
-
Specific to manufacturing, heijunka, or product leveling, is a popular lean technique for improving the predictability, flexibility and stability of your production schedule. It is defined as a technique for reducing unevenness in a production cycle, which in turn reduces waste.
Heijunka is often compared to just-in-time (JIT) practices. However, JIT doesn't produce the leveling seen with heijunka; it requires manufacturing products when they are needed in the quantity required. Heijunka meets customer demand in total over a period of level production, using finished goods inventory to make up for any short periods or periods of higher demand.
-
One of those techniques is kaizen. A Japanese term translated to mean "change for the better," kaizen is a mindset that has teams constantly working together to make incremental improvements in the manufacturing process. The kaizen philosophy emphasizes the importance of each individual's idea and that all employees be involved in process improvement.
-
Six Sigma: Six Sigma is defined as a set of methodologies, tools and techniques with the overall goal of process improvement and fewer defects. It seeks to improve the quality of products manufactured from a process by identifying and getting rid of the causes of defects as well as minimizing the variability in all processes across an organization.
Successfully implementing Six Sigma leads to an increase in performance and a decrease in process variation, which in turn can result in increased profits, improved product quality and a boost in employee morale. Six Sigma relies on data and statistics to make decisions more than any other methodology. It uses both quantitative and qualitative lean manufacturing tools like statistical process control (SPC), process mapping, failure mode and effects analysis (FMEA), and more.
Process engineers utilize one of two methodologies within Six Sigma to implement it: DMAIC (define, measure, analyze, improve and control) or DMADV (define, measure, analyze, design and verify). DMAIC is used on existing processes to identify issues and improve them through root cause analysis. DMADV is employed when organizations need to create new processes, with the goal of developing processes that are as streamlined as possible from the start.
- SIPOC analysis: SIPOC (suppliers, inputs, process, outputs and customers) is a tool that summarizes the inputs and outputs of a process in a table. SIPOC analysis is often used during the process improvement implementation during the "define" phase of a DMAIC process. It's typically employed to give everyone on the team a high-level overview of the current process, which lends itself to refamiliarizing people with the process due to changes over time. It is then utilized to define a new and improved process.
-
Kanban: While technically a lean manufacturing tool, kanban is a popular stand-alone lean process improvement technique. It is a visual tool to help personnel understand the process of a workflow. This helps eliminate inventory and overproduction by regulating the flow of goods inside and outside the factory.
Teams often use kanban boards (either digital or physical boards) with columns such as "To Do," "Doing" and "Done" to control inventory. A kanban card can be placed in a visible area to indicate when inventory needs to be replenished. With this process, products are assembled only when there is demand from the consumer, reducing inventory waste. Because of this, it is a common method utilized to achieve just-in-time (JIT) inventory.
Kanban works to implement four core principles: visualize the work, limit the work-in-process (WIP), focus on workflow and continuous improvement. Minimizing WIP is important with kanban, and kanban boards make it easy to track WIP limits by simply being able to count how many cards are in the "in-process" column. If you're using a kanban software for your board, you can even set an alert for when you reach a predetermined WIP limit.
- Value stream mapping: Value stream mapping is a lean management tool used for analyzing the current state of and designing a future state for the process that takes products or services from their inception to the customer, minimizing as much waste as possible. Value stream mapping is employed to improve processes with repeatable steps and/or multiple handoff points. Often, in manufacturing, these handoffs are easily identified, since they usually involve tangible things changing hands.
Lean Process Improvement: Getting Started
Continuously improving your business is the overall goal of process improvement, so in order to sustain this continuous cycle of putting ideas into practice, it's important to follow a simple four-step process improvement cycle.

- Identify: Brainstorm opportunities for improvement within an existing process workflow.
- Plan: Come up with ideas as to how the process can be improved (brainstorm).
- Execute: Implement the changes agreed upon by the team in the brainstorming session.
- Review: After some time has passed, conduct an audit of the new process workflow to ensure it's doing what you intended.
While this four-step continuous process improvement cycle lays out a solid mindset for lean process improvement, it doesn't give you an actionable plan for how to manage and measure your improvement efforts. To move your ideas from the brainstorming room and into reality, you'll need some actionable steps for implementing the methodologies discussed above.
Actionable Steps for Implementing Process Improvement

- Map the current process. Before you do anything else, take an in-depth look into the current process in question. With your team, visually map out the current steps to the process to identify areas for improvement. Many organizations use simple flow charts to visualize how each step flows into the next.
- Analyze the process: Using the flow chart you've just mapped out, closely examine each step with your team. Speak with operators and determine where delays routinely occur, where too many resources are employed, or where you spend a lot of money. Finding the root cause of these issues is the most critical part of this step; you must figure out exactly where in the process the problem occurs to understand how to fix it. This is where the root cause analysis method and Six Sigma come in handy.
- Redesign the process: After issues are identified and root causes are determined, redesign the process to eliminate the problems you've discovered. Again, this is a team effort. Involving the entire team in this step ensures you have the correct understanding of the old process. Consider each team member's ideas during the brainstorming session. For each idea, think about how the affected team members would carry out the redesigned process, how long it would take and what the potential risks are.
- Assign resources: This step involves discussing what you will need to make this change happen. Consider all the departments that may be impacted by this change and discuss the proposed change with other managers. After everyone affected is aware of the change, let them know what their new process entails by explaining the new process, how it impacts their current job and how it affects the overall organization.
- Design an implementation plan: Everyone should now know their new role and have the resources needed to put the new process into action. Next, it's time to create an implementation plan. Working with the team members you've identified in the previous step, develop a detailed plan containing specific tasks each person will be working on and the resources that will be used during each step. Create a timeline showing when each task will begin and end using specific dates for the action to take place.
- Execute the plan: The most important part of this step is communication. Before an action is taken, verify that the new process and implementation plan have been communicated with each affected team member. Keeping everyone in the loop of any process changes helps ensure they won't resist the new process. Put the plan into action following the implementation plan you created in the previous step.
- Audit and optimize: Since the goal is continuous process improvement, your work is never done. It's a continuous effort. Once the new process has been put into action, schedule a time down the road to perform an audit on the changes, so you can see if they're actually making a difference. Regular process improvement audits help ensure employees are following the new process as outlined in the plan. Audits can also identify any bottlenecks that may arise and enable you to work with the team to get past them.
What Is an Example of Process Improvement?
As mentioned in step seven, process improvement should be a continuous endeavor. Let's take a look at some examples of how you can continuously make process improvements in a manufacturing setting.
- Team brainstorming sessions. Regular team brainstorming sessions, or think-tank sessions, can have multiple benefits. Not only do they continuously bring ideas for process improvement to the forefront, but they create a sense of ownership among employees. When everyone's ideas are considered, personnel are more likely to feel appreciated, which makes them more inclined to get on board with any process improvement changes made in the future. It's a good idea to have an agenda for these meetings, including a time for each individual or team to present ideas.
- Monthly training and cross-training. Ongoing training goes hand-in-hand with continuous process improvement. Cross-training employees on multiple positions helps protect processes from natural bottlenecks that tend to happen as a natural result of human-focused processes. If someone is on vacation or out sick, a cross-trained employee can step in and prevent a bottleneck from occurring due to the missing team member. Cross-training is often done through monthly or quarterly continuous education.
-
Poll employees and customers. Employees work directly with the processes in place every day. They have the best insight into things like what is causing an error. Most employees probably could give you a list at any given moment of potential improvements that could be made.
Surveys are a key tool for continuous process improvement and can help you understand how your processes impact the entire organization. Survey your employees, vendors and customers with unique questions on how things could be improved. You might discover issues that weren't even on your radar. Among the questions these surveys should include would be:
- What are you, as a leader, doing that employees are happy with?
- What could be done to improve the quality of products and services?
- What changes would employees like to see in the future? Ask them to prioritize their list as to what is most important to them.
Carefully compare the results from these surveys over time to see how your organization operates and gain insight into how process improvement changes have or have not improved your processes.
- Time audits. Set measurable benchmarks so you can track things like how long it takes to complete a specific task. This benchmark can then be used to measure against any other process improvements or changes. Over time, this helps you track how efficient and effective your process is. Some organizations bring in a third-party researcher to conduct process improvement audits, so detailed data can be collected, analyzed and compiled into reports showing how new processes or changes are performing.
- Efficiency audits. Continuously looking to improve processes related to delivery cycles, billing cycles or anything that affects production can lead to less wasteful use of resources and allow your organization to do more in the same amount of time. Improving your single-minute exchange of die (SMED) process, for example, can eliminate time-wasting and result in faster delivery cycles.
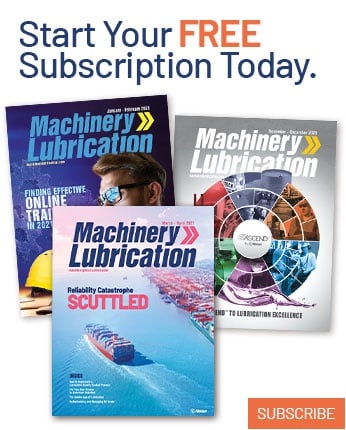