Most producers of commodity products have recognized the importance of continuous, uninterrupted manufacturing operations. Manufacturing reliability allows for full asset utilization, maximizing measures such as return on investment (ROI) or return on net assets (RONA). As important, smooth operations allow managers time to think and plan, to prepare for the future and work on important plant initiatives.
Downtime events inevitably distract attention, creating an atmosphere of crisis and blame. When these schedule-breakers are frequent, customer orders fulfillment requires heroic efforts by everyone in the plant. Production levels decrease; quality issues increase; costs for overtime and parts increase. Profits, especially in a low-margin business, can disappear from a single unplanned outage.
Most companies now recognize that manufacturing reliability is a key to their success. In our experience, that is a new recognition for many companies, where global competitors have made selling prices decrease and quality demands increase. This new realization has company executives searching for an effective approach to improve.
We see many approaches in our marketplace. Teams are formed with the mission of learning and applying best practices, perhaps to buy and implement a new maintenance management system, or benchmarking other companies’ practices. If they are very good and have strong management support, they will make some progress on their own. In other cases, they don’t know what they don’t know, and will spend several years, and possibly millions of dollars, trying to learn. This turns out to be an expensive education, during which the industry progresses beyond the plant in question.
Sometimes the company will choose a consultant to guide them. Depending on the breadth of the consultant’s knowledge and the skills of the individual consultants, this method can minimize the wasted time and money on the path to improved maintenance. Still, the inherent barriers to change will be in the way.
Barriers to change
The first barrier that companies face is ignorance, in a marketplace full of acronyms where each set of letters promises the results of improved reliability. What is the right answer? A variety of vendors offer the following:
-
P&S (Planning and Scheduling): Planned work is shown to be three times as time-efficient as unplanned work, leading to getting more work done.
-
PM (Preventive Maintenance): If through proper inspections we can catch and fix problems before failure, reliability should improve.
-
PdM (Predictive Maintenance): By understanding equipment condition under load conditions, we should be able to identify and trend impending failures, replacing components at the end of their useful life.
-
CMMS (Computerized Maintenance Management Systems): Installing a new system should lead to better control and organizational knowledge, giving us the information we need to improve reliability.
-
TPM (Total Productive Maintenance): Enabling the operator to perform equipment care tasks puts responsibility for problem identification and minor maintenance with the person closest to the equipment.
-
RCM (Reliability-Centered Maintenance): RCM promises to eliminate the source of the equipment defect so that it cannot occur.
-
RCFA (Root Cause Failure Analysis): When problems occur, we can study what went wrong, and stop it from happening again.
Any of these techniques and technologies can be helpful in improving equipment reliability. What any one of these processes in isolation misses is that fundamental behaviors must change for any of them to be systematically applied throughout the plant. Some are very complex to learn; some a huge amount of effort to implement. If any step is done with an incomplete understanding, the results will be suboptimal.
Once again, learning will occur, but not necessarily progress.
About the author:
S. Bradley Peterson is the founder and principal owner of Strategic Asset Management Inc. (SAMI), a business improvement consulting firm based in Unionville, Conn. For more information, visit www.samicorp.com.
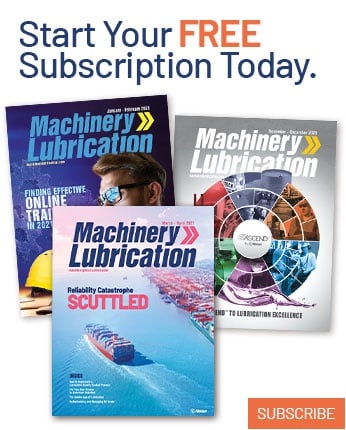