Maintenance operations represent a significant investment in industrial facilities, and this crucial practice can produce substantial benefits for the entire facility through optimization efforts.
While there is no one right way to approach maintenance optimization efforts, a facility can deploy four practical strategies to begin reaping the benefits of a transformed system.
Evolving from Preventive to Predictive Maintenance
While preventive maintenance (PM) and predictive maintenance (PdM) are frequently considered similar, it's essential to differentiate them to optimize a facility's maintenance practices.
At its basic level, PM schedules routine equipment inspections to uncover issues before more significant maintenance problems develop. While PMs can reduce downtime and minimize production losses, this method has limitations. For example, PM is schedule-based, not condition-based, which can lead to excessive maintenance. In turn, this can lead to maintenance-induced failure, unnecessary downtime, and wasted technician time.
Additionally, issues can only be caught during scheduled inspections, meaning issues developing between inspection periods can go unchecked and cause excessive damage. However, instead of abandoning preventive maintenance entirely, a better strategy is to evolve them into something more sophisticated: predictive maintenance.
Unlike PM, PdM monitors machinery during operations to detect anomalies at their inception and circumvent failure and machine damage altogether. If implemented correctly, PdM provides accurate, timely data on machine conditions and performance during normal operations. As a result, the benefits of PMs are extended, and the challenges are reduced; according to the Department of Energy, PdM programs save up to 40% in maintenance costs over reactive maintenance and up to 12% over preventive maintenance.
Establishing Condition Monitoring
Many predictive maintenance cultures cannot function efficiently without condition monitoring. Condition monitoring measures machine performance against preset parameters during operation, noting any changes in performance that could indicate impending failure. Once established in a facility, condition monitoring collects and provides timely insights into the health of any machine on the monitoring system.
This collected information is crucial to maintenance activities, providing historical data, anticipating future asset performance and degradation rates, and helping determine root causes. This allows anomalies to be predicted before damage occurs and corrective maintenance action to be scheduled at the optimal time with minimal impact on production.
Modern technology allows most condition-monitoring activities to be performed using wireless sensors and internet-connected software. Combined with this real-time connectivity, condition monitoring provides several benefits, including decreased maintenance costs, reduced downtime, extended asset life, and cost savings through saved resources such as technician time and parts replacements.
Implementing CMMS or EAM
A key component for optimizing maintenance is a computerized system to help manage the nuances of facility maintenance activities. Two common options include a computerized maintenance management system (CMMS) and an enterprise asset management (EAM) system. While similar, understanding their differences is crucial to selecting the right one.
CMMS software simplifies and helps manage maintenance activities. The software collects and stores all maintenance operation information in a single database. It also analyzes and disseminates the information to help maintenance personnel better understand their equipment and what maintenance activities to perform. Most CMMS solutions are extremely customizable, and can include:
- Predictive maintenance task management
- Work order systems
- Maintenance planning and scheduling
- Vendor and inventory management
While CMMS helps with maintenance specifically, EAM systems help manage a facility’s entire infrastructure and all physical asset lifecycles, from installation to replacement and disposal. This system can function across every department, (even seemingly unrelated departments like finance and human resources), to ensure the entire business is operating in lockstep.Additional features common to EAM systems but not CMMS can include:
- Budgeting and accounting
- Energy monitoring
- Fleet management
- Floorplans and schematics
By selecting the right system to accommodate a facility’s needs, maintenance teams can access the tools and assistance required to advance maintenance optimization initiatives and better understand and care for critical equipment.
Investing in Workforce Training and Development
With the looming threat of mass retirements and a growing skills gap, investing in workforce training and development is one of the best ways to fortify a facility's maintenance optimization efforts. Even with the latest systems and technologies, few benefits will be realized if technicians aren't adequately trained.
Workforce training and development require an upfront investment. However, the effects produce compounding benefits that create a thriving maintenance culture by developing technician skills and fortifying a facility’s ability to achieve business goals and objectives.
In addition, training and development opportunities produce compounding benefits, including:
- Increased operational efficiency
- Enhanced workplace safety
- Reduced downtime
- Increased adaptability to technological advancements
Workforce training and development opportunities also come in multiple forms to meet business needs and technician learning styles. These can include:
- In-person or online training events
- Interactive technologies, such as virtual reality (VR)
- Mentorship programs
- Career development opportunities, such as industry conferences
No matter the format, investing in the people who maintain critical equipment and bring invaluable skills to the facility can only enhance the company and enable progress toward meeting maintenance optimization goals.
Supplier Spotlight
AssetWatch 60 Collegeview Rd., Westerville, OH 43081 844-464-5652 | www.assetwatch.com
Predictive maintenance has never been easier or more cost-effective, thanks to end-to-end condition monitoring from AssetWatch. With remote wireless sensors, advanced AI, and CAT III+ experts—all for a low monthly subscription—your team will have the power to conquer unplanned downtime for good. Try us risk free for 30 days, and start seeing value on day one.
RelaWorks 1328 E. 43rd Court, Tulsa, OK 74145 918-392-5058 | RelaWorks.com
Finding the right products can be difficult. Every industry and application is unique. Over-spending and guess work is common. At RelaWorks, we help reliability professionals solve this challenge. Our mission is to provide products for your unique needs and budget. Backed by Noria Corporation’s expertise and legendary customer service, we’re excited to help your reliability program succeed.
LubePM 1328 E. 43rd Court, Tulsa, OK 74105 800-597-5460 | LubePM.com
As a Lubrication Management System (LMS) engineered by lubrication professionals, LubePM helps an organization create accountability to ensure that every lubrication point is carefully maintained, inspected and measured. Ready to take your facility’s Lubrication Management System to the next level with LubePM? We’re ready to help. Simply request more information or schedule a demo.
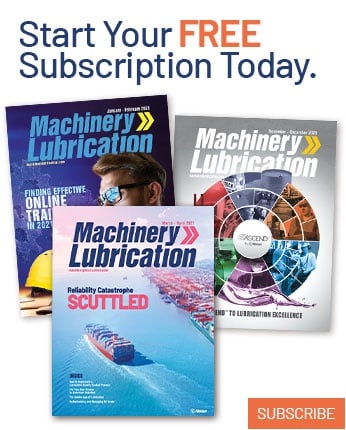