When people see another acronym, they often ask themselves if this will be another idea supported by great intentions that quickly becomes more of a marketing buzzword than an actual practice.
But what about Asset Performance Management (APM)? Is it really worth looking at and spending effort on?
Managing the performance of assets that a business has made significant investments in has been and always will be central to the success of any operation. Just like the stock market and real estate holdings, knowing how investments are performing in relation to expectations is critical.
What happened in the past can impact performance, but it is more important to understand what is happening now and how it sets the stage for the future. Good performance in the past, or even in the present, is not a guarantee of good performance tomorrow.
The management part of APM begins with complete and reliable information. Then, decisions are made, and actions are taken to preserve performance levels over time. Let’s talk about the APM lifecycle and some of the methods and tools available to support this important program.
What Are Assets, and What Do They Require?
The answer to this question is not as simple as one might think. Certainly, anything the business has ever purchased, even consumables, could be considered an asset. Viewing assets with this broad scope immediately makes their management difficult.
Additionally, definitions may vary between departments. For example, the accounting team will most likely have a different perspective of what an asset is on the company books. A more actionable approach is to establish a list of “critical” pieces of equipment that the business relies upon and that are significant investments.
Assets can also be considered anything that costs money to “operate” over their entire lifecycle, which the business must bear. This could include not only a piece of equipment, but an entire facility. The lifecycle phases to be mindful of include:
- Design
- Procurement
- Implementation
- Operation
- Maintenance
- Refurbishment
- Disposal
The goal is that these ownership costs are far outweighed by the profits generated through the production process or the product for which the asset was initially purchased.
This points to the idea of performance expectations. Questions to consider include:
- What production level is expected of the asset?
- How much uptime is required to meet this goal?
- What is the cost of downtime to the company regarding the labor required to return the asset to service and the loss of production?
Assets will also require new skills and qualifications to operate and maintain properly. It can be challenging to transfer technical knowledge from even five years ago to the new equipment that just appeared on the loading dock for installation.
While some maintenance procedures have not changed in 50 years, simply assuming a pump is a pump is no longer a valid approach. A robust training and qualification program is necessary for any organization managing assets.
Another aspect of managing asset performance is spare parts and consumables. Often forgotten, spare parts – or the lack thereof – can be the biggest detractor to any asset’s performance. No parts mean no production. While the availability of spare parts and consumables may not be of concern with new equipment, they can be challenging to acquire for older equipment.
In a way, all the issues listed above can be perceived as the formation of nightmares. Not to worry; assets are not out to get you! However, an organization will significantly benefit from having a plan – often called a Strategic Asset Management Plan (SAMP). A SAMP is an excellent vehicle to clearly describe the focus groups of assets, what is expected of them, and how they will be managed over their lifecycle.
Collecting the Right Performance Data
Before any asset performance data is collected, it must be determined precisely which kinds of data are required. Collecting data just to do it in the hope that it will be helpful someday is not sustainable. This is especially true if the data collection process requires staff to enter the information manually. Garbage in means garbage out.
Knowing the expected performance of the assets is critical. How many widgets per hour, gallons per day, operating hours per month… the list goes on and on. Establishing what needs to be measured should come before attempting to collect data for the measurement. Then, you can figure out the most efficient method to collect the data that supports the measurement.
Data collection comes in many forms. Modern equipment may provide telemetry that can be used for various purposes. This telemetry can contain vast numbers of elements, often arriving at fraction-of-a-second intervals. Telemetry may be used primarily for operations but can contain a treasure trove of performance information. The trick is knowing how to gain access to it and what tools can interpret it.
Manual data collection is a perfectly valid approach if it results in good data. The challenge with manual data entry is to make the process as efficient as possible for the staff doing the work and for it to result in good data. Rather than having staff type values, configure the system to provide them with drop-down lists to pick from. Keep the number of required fields to a minimum and be sure they are required in the context of the work being performed.
As the needs change, so will the need for data collection. Be sure that the data collection efforts are refined as the operation evolves. Regularly reviewing the data collection needs across the operation is an excellent process and should be considered when designing a SAMP.
Analyzing the Collected Data
Collected data is worthless if it isn’t used. The first step towards use is data analysis. Much like data collection, the expected analysis methods and tools must be defined before the analysis begins. If the collected data doesn’t support an analysis approach, then the results may be of limited use.
An example of this would be trying to calculate an accurate average or mean with an extremely small data set. While a result will be generated, it is unlikely to be an accurate representation or prove useful.
Today, a variety of analysis tools are available on the market, especially since the introduction of machine learning (ML) and artificial intelligence (AI). Gone are the days when a spreadsheet with formulas and macros is needed to visualize metrics. Business intelligence tools, some built into Enterprise Asset Management (EAM) and other systems, have vast amounts of functionality and data visualization methods.
However, additional skills will be needed to get the most out of these tools and produce meaningful results for the organization. A report full of interesting-looking charts and graphs may seem useful, but if they do not support decision-making, it is a waste of time.
Analysis methods need to be documented and refined over time. A metric that was useful a few years ago might not be as valuable today. As with data collection, the resulting analyses must evolve as the organization does. This highlights another key element of the SAMP – data analysis management.
A nuance to analysis is the need to consider external factors that impact asset performance. The data collected might not include important elements such as ambient temperatures, weather patterns, and contractor usage, which can all dramatically impact asset performance and might not be part of captured telemetry. This is where a Reliability Centered Maintenance (RCM) technique might be leveraged here.
Using Data to Guide Decision-Making
With quality data and insights from the analysis stage, the next step in APM is making decisions. Often, people think they must take action, but it’s okay if the insights suggest not doing anything; doing nothing is a decision.
Either way, no matter what the decision, it must be recorded for all to see, not only now but also in the future. This will help future efforts when an issue arises, and research is needed. While most organizations are great at recording “what” decisions are made, this step will ensure they accurately record “why.”
Asset performance decisions can range from the previously mentioned “do nothing” approach to the need to replace the asset within a limited timeframe. Changes to the methods used to maintain or operate assets may also be needed to help them perform as expected or extend their useful life. This is especially true as assets begin to age to protect the facility’s investment.
When trying to identify the best decision, start with a well-formed problem statement. In Lean and Six Sigma, a quality problem statement is formed by:
- Clearly identifying the pain or the gap that is occurring.
- Pointing to when and where the issue or trend was observed.
- Quantifying the impact the issue has on those affected.
- Calmly describing the importance of addressing the issue.
Developing a problem statement to identify a decision provides a framework to follow and an assurance that the decision was made based on credible information. The more precise the reasoning behind a decision is, the more likely it will be adopted by those impacted by the decision or the resulting changes.
The Value of APM: Taking Action and Adjusting
While each stage provides multiple benefits, the real value of an APM approach resides in taking action based on accurate data, analysis, and recorded decisions. Once a decision is made, it must be acted on, and the results must be recorded. The hope is that all decisions made will result in effective actions, but keeping accurate records and reviewing them often is the only way to measure success.
For example, let’s say a decision was made to add a step to an asset’s preventive maintenance plan. Based on the performance data, it’s projected that adding this step will enable the asset to operate longer between service interruptions.
Keep in mind that this additional step will increase costs, and accurate record-keeping during implementation will help determine if the action is producing the desired effect. If the effect is positive, then the data, analysis, and decision-making steps were successful. If not, then the analysis, and even the data source, will need to be reviewed and potentially questioned.
Managing an asset’s performance is about taking action over time to preserve its function and enhance a facility’s return on investment. Effective actions are based on informed decisions, which come from thoughtful analysis of reliable data.
Repeating the Process
While successes should be celebrated, don’t let it delay you from continuing to review other assets and their performance. Continue to capture useful data and perform analyses that deliver insightful results, which can be used to make well-informed decisions. Effective and traceable actions result from these good decisions, allowing facilities to extend equipment life and enhance maintenance practices.
Wrapping Up
With the true value of Asset Performance Management revealed, it’s easy to see that it’s not just a marketing buzzword but a well-formed process that delivers lasting results from a facility’s hard work and dedication.
APM is not a new discipline. It has been practiced for decades; it just didn’t have a name. Now, there is not only a new acronym to banter about but a defined and proven approach that can formalize and support an organization's high-performance expectations.
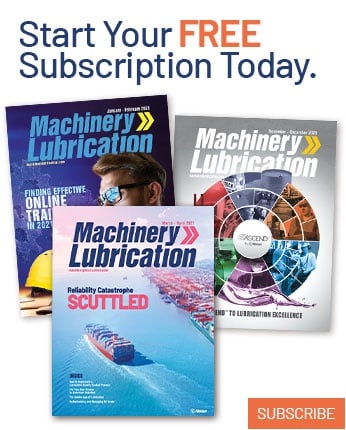