Introduction
In the industrial world, unexpected equipment failures can lead to significant operational disruptions, safety hazards, and financial losses. This case study from January 2024 highlights the importance of timely maintenance, systematic diagnostic procedures, and the potential cost savings achieved by addressing issues before they escalate. The case revolves around the kiln primary air fan, a critical component in the production process, which tripped on high load, leading to a temporary kiln breakdown. The maintenance team averted a more severe incident through a detailed inspection and corrective actions and saved substantial costs.
Incident Overview
The kiln's primary air fan motor, operating without issues for a decade, began to show signs of distress when its current gradually increased from 92 amperes to 180 amperes over six days. No defects were initially found despite various inspections, including vibration analysis and lubrication checks. However, the motor eventually tripped on overload, causing a brief kiln shutdown.
Inspection and Actions Taken
During the six days leading up to the breakdown, the maintenance team performed multiple inspections and took several actions:
- Vibration measurements of the motor and fan bearings remained within the normal range of 2-3 mm/sec.
- Alignment checks of the motor and fan were conducted, and the results were satisfactory.
- The fan outlet's pneumatic control valve was verified to function correctly.
Despite these efforts, the motor's high load persisted, leading the team to suspect internal winding problems due to the motor's age. The decision was made to replace the motor, but the problem also continued with the new motor. This prompted a more in-depth inspection of the kiln main burner, revealing a significant issue: a 1.5-meter-long crack in the burner jacket with a 20-30 mm opening.

(Photo of a kiln burner complete assembly showing the location of the hole and burner jacket)
Corrective Actions and Outcome
The burner jacket's crack allowed primary air to escape, causing the fan to run continuously at high amperes to maintain the required air pressure. The maintenance team quickly patched the hole with anchors and castable, securing the burner jacket. As a result, the fan's current load immediately dropped to the normal range of 90-95 amperes, and the primary air fan pressure set point was achieved.
Recognizing that the original motor was still functional, the team reinstalled it and returned the new motor to the warehouse, thereby saving the $14,700 maintenance cost.
Savings and Safe Operation
By addressing the problem promptly, the maintenance team achieved several key outcomes:
- The SIEMENS motor was saved from potential damage, avoiding continuous operation at high load, which could have led to overheating and possible fire incidents.
- The planned maintenance approach prevented a longer and more costly breakdown, resulting in net savings of $33,331 from reduced clinker production loss.
- The team's efforts were recognized by the plant director during a daily cross-functional meeting, highlighting the importance of proper diagnostics and solution implementation.
Conclusion
This case study underscores the critical role of preventive and predictive maintenance in industrial operations. By systematically diagnosing the issue and taking timely corrective actions, the maintenance team ensured the kiln's safe operation and realized significant cost savings. The lessons learned from this incident, including the importance of visual inspections, vibration analysis, and effective maintenance strategies, are invaluable for any organization aiming to minimize downtime and enhance equipment reliability.
Key Takeaways
- Systematic diagnostic procedures, including visual inspections and vibration analysis, are essential in identifying hidden defects.
- Timely and well-planned maintenance can prevent costly breakdowns and safety incidents.
- Proper communication and recognition of the maintenance team's efforts contribute to a culture of safety and efficiency.
- This article reminds us of the importance of staying vigilant about equipment maintenance and the benefits of addressing issues before they escalate into more severe problems.
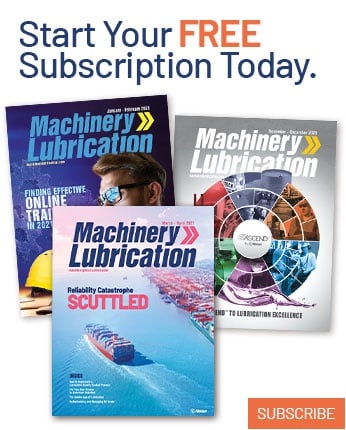