The Foundation of Reliability: Understanding Lubrication

The Role of Lubrication in Maintenance
- Reduced Wear and Tear: Lubricants form a thin film between moving parts, minimizing direct contact and reducing wear. This extends the life of components and decreases the frequency of replacements.
- Decreased Downtime: Well-lubricated machinery is less likely to suffer from unexpected breakdowns. Regular lubrication schedules ensure that all parts operate smoothly, reducing the risk of sudden failures that can halt production.
- Improved Efficiency: Lubricated machinery operates more efficiently, with less friction to overcome. This translates to lower energy consumption and improved overall performance.
- Simplified Maintenance: Regular lubrication is a straightforward maintenance task that can prevent more complex and costly repairs. By keeping up with lubrication schedules, maintenance teams can avoid larger issues.
Types of Lubricants and Their Applications
- Mineral Oils: Derived from crude oil, these are the most common lubricants used in industrial applications. They are suitable for a wide range of machinery and offer good performance at a relatively low cost.
- Synthetic Oils: These are chemically engineered to provide superior performance, particularly in extreme temperatures or high-load conditions. Synthetic oils are more expensive but offer extended intervals between changes and better protection.
- Greases: Greases are semi-solid lubricants used in applications where liquid lubricants would not stay in place. They are ideal for high-load and slow-speed applications, such as bearings.
-
Solid Lubricants: Materials like graphite and molybdenum disulfide can be used as solid lubricants in high-temperature or vacuum environments where liquid lubricants would evaporate or degrade.

Best Practices for Lubrication Management
- Regular Inspection and Maintenance: Establish a routine schedule for inspecting and maintaining lubrication systems. This includes checking lubricant levels, looking for signs of contamination, and ensuring proper application.
- Training and Education: Ensure that maintenance personnel are trained in the correct lubrication techniques and understand the importance of lubrication. Proper training can prevent common mistakes that lead to inadequate lubrication.
- Condition Monitoring: Implement condition monitoring tools, such as vibration analysis and oil analysis, to assess machinery's health and lubrication effectiveness. These tools can detect early signs of lubrication issues before they lead to failures.
- Choosing the Right Lubricant: Select lubricants specifically designed for your machinery's operating conditions. Consider temperature, load, speed, and environmental conditions when choosing a lubricant.
- Proper Storage and Handling: Store lubricants in a clean, dry environment to prevent contamination. Use dedicated equipment for dispensing lubricants to avoid cross-contamination and ensure that lubricants are applied correctly.
Conclusion
Supplier Spotlight
Fluid Metrics 4514 Chamblee Dunwoody Rd. #252, Dunwoody, GA 30338 p: 770-393-8636, f: 770-393-8631 | FluidMetrics.com
Founded in 2003 by a compressor industry veteran, Fluid Metrics utilizes the latest lubrication technologies to maximize compressor performance and reliability. When combined with a proactive, condition-based maintenance plan, our advanced compressor oils, purifiers, and conditioners are proven to dramatically increase compressor reliability, slash your oil and parts consumption, and save you time and money. Give us a call today to learn how much easier and better compressor oil maintenance can be.
RelaWorks 1328 E. 43rd Court, Tulsa, OK 74145 918-392-5058 | RelaWorks.com
Finding the right products can be difficult. Every industry and application is unique. Over-spending and guess work is common. At RelaWorks, we help reliability professionals solve this challenge. Our mission is to provide products for your unique needs and budget. Backed by Noria Corporation’s expertise and legendary customer service, we’re excited to help your reliability program succeed.
Noria Academy 1328 E. 43rd Court, Tulsa, OK 74105 800-597-5460 | Noria.com/Academy
Obtaining certification can be a challenge; new terms, concepts and topics can overwhelm even the most experienced reliability professionals. Training experts all agree that extending the learning beyond the classroom dramatically increases knowledge retention. To aid in this retention and create an innovative student experience, Noria is pleased to offer the Noria Academy app.
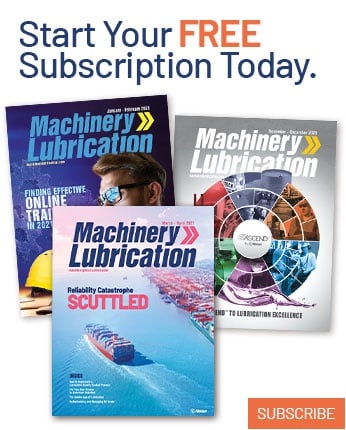