For the past decade, I've been involved in benchmarking activities. In my role as Cargill's worldwide reliability and maintenance manager, my colleagues and I have traveled the globe to many of our food-processing facilities. Additionally, in our networking with companies active in the Society for Maintenance & Reliability Professionals, we've visited many other industry segments such as steel, pharmaceuticals, mining, energy, petrochemicals, automobile assembly and bearing assembly. The most common words I hear during these travels are: "Yeah, but we're different."
Translation? "We're in the (fill in the blank) business, and no one can compare what we do to the benchmarks held for other businesses." I recently heard this quote: "Every plant is a snowflake with a unique structure and DNA."
My first response is, you are right. You are different. But, you may be about 10 percent different and 90 percent the same. I continue to be approached by individuals who seem to think that M&R practices need to be distinctly different from one industry to the next.
At Cargill, we believe that proactive M&R principles can work in all environments, businesses, geographies and facility sizes. We teach the following: Plants, whether varying in size, business, operation or geography, have mechanical and electrical equipment used to make a product for customers. Although used in many different operating contexts, the equipment design and operation follows the mechanical and electrical laws of nature.
Many facilities have little redundancy, so most of the equipment is critical due to one or many factors: safety, environmental, quality, production, customer impact and cost. Some facilities have more redundancy or equipment that's only used periodically. In many of these cases, these critical pieces of equipment have failure modes that have consequences that are unacceptable to the business in some way at some time. Therefore, it's beneficial to prevent or detect these failure modes before they occur. This helps in many areas: safety, environmental, customer service and cost, to name a few. Actions to prevent or detect these failure modes - predictive techniques, preventive tasks, failure-finding tasks and/or equipment redesign efforts - are functions of the proactive M&R model. All facilities will have some critical equipment with failure modes that must be detected by these methods.
The issue has been that the paradigm of "we're different" limits a person and organization's thinking to apply the appropriate proactive strategy to the situation. It allows you to have an excuse for not getting the available reliability, safety, environmental, quality, operating efficiency and maintenance cost improvements that the business needs and requires to stay competitive.
I recently read a very good article by Gabriel Szulanski and Sidney Winter in the Harvard Business Review titled "Getting it right the second time". The premise of this article was that even though everyone says they benchmark results and practices in a particular discipline, few truly use a best practice found successful in another business in its entirety or without modification. The authors state that nearly everyone wants to tweak or modify the practice to fit the situation or business, or just to give it their own spin. By doing this, the practice's effects and results are minimized. Few truly use the found best practice and apply it directly to their business. The authors point out that when a practice is directly applied with no modifications, results are experienced quicker, in larger amounts and in a more complete nature.
In my travels, I've seen this behavior. Many facilities with the "we're different" paradigm opt to tweak, resize, dumb down or fancy up a best practice before they even try to apply it. Many spend more time in the evaluation and modification process than in the planning process needed to directly implement the practice. Results are slower and the impact minimized.
However, after several years of applying these same principles and practices directly in Cargill, we have facilities in different businesses, geographies and sizes achieving significantly better M&R results than previously experienced.
I believe the power here is to take the learnings from distinctly different businesses and be the first to apply them to your business. Seek out an array of businesses to understand how they apply M&R principles and practices. This learning can set you apart from your competitors and help you succeed.
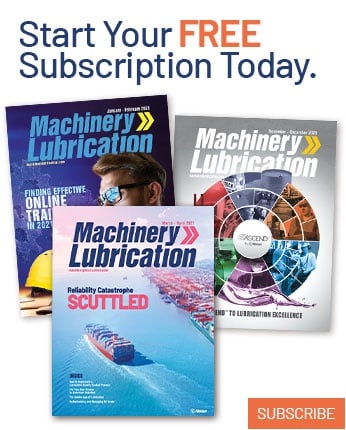