In the modern workplace, where the symphony of technology and human effort choreographs the dance of industry, maintenance has become a silent ballet that nurtures the kinetic energy essential for operations. Yet, maintenance practices are evolving to a crescendo that is not just about keeping machines running, but also about predicting health, ensuring safety, and conserving the precious resource of time. Predictive maintenance (PdM) stands at the forefront of this evolution, wielding data, analysis, and foresight to minimize risks, enhance safety, and reduce downtime.
How Predictive Maintenance Enhances Workplace Safety
The correlation between predictive maintenance and workplace safety is a direct one. Equipment failure is a leading cause of occupational injuries and fatalities. PdM, through continuous monitoring and predictive analytics, identifies potential failures before they lead to catastrophic events. By analyzing data patterns, anomalies can be rooted out, and maintenance scheduled to prevent dangerous conditions from manifesting.
Real-Time Monitoring and Response Systems
PdM entails the use of sensors and IoT technologies to monitor equipment conditions in real-time. As the sensors pick up signals of deviation, alerts are sent out, enabling rapid intervention before a safety hazard can escalate. This proactive approach transforms maintenance into a preventive safety measure, cultivating an environment where the workforce can operate with confidence in the tools at their disposal.
Data-Driven Risk Assessment
Predictive models assess the risk of potential equipment failures, classifying them based on severity. This risk data provides a proactive guide for resource allocation, ensuring that high-risk areas are under constant vigilance, lessening the probability of accidents associated with equipment malfunction.
Reducing Equipment Downtime with Predictive Maintenance
The financial implications of downtime are significant, but so are the operational and safety implications. Downtime can force operational teams to make hasty decisions, escalate workloads on unaffected machines, and disrupt safety and training protocols. Predictive maintenance steps in with a promise of minimizing these disruptions through better planning and foresight.
Proactive Equipment Health Management
PdM systems provide insights into the actual health of machinery. By precisely forecasting when maintenance is needed, companies can schedule downtime during off-peak hours, minimizing the impact on production schedules and, consequently, workplace safety protocols that can indirectly be affected during high-intensity operational periods.
Efficiency through Smart Maintenance Schedules
With predictive analytics, maintenance schedules transform from periodic overhauls to intelligent plans that address specific wear-and-tear conditions. This not only prevents sudden breakdowns that can compromise safety but also ensures that the equipment operates at peak efficiency, reducing the possibility of creating unsafe work conditions due to suboptimal functionality.
Innovative Technologies Improving Site Safety in Manufacturing Environments
Emerging technologies are amplifying the capabilities of predictive maintenance, pushing the boundaries of enhanced safety and downtime reduction.
AI and Machine Learning
Artificial intelligence and machine learning are opening new vistas for PdM. They enable systems to learn the normal operation parameters of machines and, thus, quickly detect outliers that signify potential safety concerns. The self-learning nature of AI in these systems means that as they gather more data, their diagnostic precision improves, which has a direct impact on overall workplace safety.
Drones and Robotics
In scenarios of high risk or in large-scale industrial environments, drones and robotic systems can reach inaccessible or hazardous areas, conducting fault inspections without risking personnel. This technology not only mitigates the risk of accidents but also expedites the inspection process, leading to more timely maintenance interventions.
BIM Software
Building Information Modeling (BIM) software, integrated with predictive maintenance data, can simulate the impact of potential equipment failures on a building's structure and identify any safety concerns that may arise. This enables proactive planning for necessary repairs or upgrades, minimizing downtime and ensuring the safety of occupants.
Overcoming Challenges in Adopting Predictive Maintenance
While the merits of PdM are profound, integration into existing processes isn't without its hurdles.
Change Management and Training
The philosophy and practices of maintenance teams, which are deeply ingrained in ensuring both the efficiency of operations and the safety of the plant workforce, necessitate thoughtful adaptation. Transitioning to a predictive model not only requires change management that encompasses training on new systems and an internal culture shift towards data reliance. It also prioritizes plant workforce safety training as an integral component of this evolution. This adjustment period can pose resistance but is pivotal for reaping the benefits of predictive maintenance in the long term.
Infrastructure and Integration
The cost and effort involved in installing monitoring systems can be a barrier. There must also be a smooth integration with existing software and control systems to ensure seamless data flow and actionable insights. Investing in this infrastructure is an investment in safety and operational efficiency, but it must be done strategically to maximize returns.
The Future of Workplace Safety and Efficiency with Predictive Maintenance
Looking ahead, predictive maintenance is not just a trend but the future of how industries will manage their assets. As we weave a tighter mesh of technology and foresight into our daily operations, the safety net grows stronger, ready to catch any anomalies before they can disrupt the harmony of the workplace.
Predictive Maintenance and Eco-Efficiency
In the context of sustainability, predictive maintenance can help reduce energy consumption and the carbon footprint by ensuring that equipment operates optimally and is not overworked unnecessarily due to inefficiencies caused by undetected faults.
Aligning Predictive Maintenance with Organizational Goals
Adopting PdM is not just about implementing a new process; it's about aligning the maintenance function's objectives with the organization's strategic goals. This alignment ensures that the safety and uptime enhancements of PdM are not just operational successes but business successes as well.
A Safer and More Efficient Future with Predictive Maintenance
Predictive maintenance is a keystone in the arches of workplace safety and productivity. As it gains prominence, it's critical to recognize its potential and the commitment required to fully integrate it into the fabric of modern industry. The promise of a safe and efficient work environment, built on the pillars of data and anticipation, is within reach. For those willing to make the leap, the reward is an operational framework that not only maintains but also advances the safety and efficiency of the workplace.
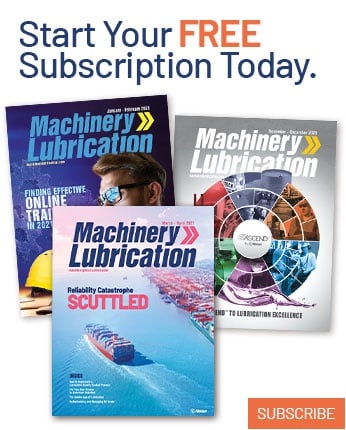