Understanding Maintenance Optimization
The Pillars of Maintenance Optimization
- Predictive Maintenance (PdM): Leveraging advanced analytics, IoT sensors, and machine learning to predict equipment failures before they occur, enabling timely interventions.
- Reliability-Centered Maintenance (RCM): Focusing on critical assets and their potential failures, RCM tailors maintenance strategies to each asset's operational context and risk profile.
- Total Productive Maintenance (TPM): Engaging all employees in proactive maintenance activities, fostering a culture of continuous improvement and accountability.
The Strategic Importance for C-Suite Executives
Aligning Maintenance with Business Goals
- Cost Reduction: Minimizing maintenance expenses while preventing costly breakdowns.
- Operational Efficiency: Enhancing productivity through improved equipment availability and reliability.
- Risk Management: Mitigating operational risks associated with equipment failure, safety incidents, and compliance violations.
Implementing Maintenance Optimization: A Roadmap for Success
- Assessment and Planning: Conduct a comprehensive audit of existing maintenance practices, identify inefficiencies, and establish clear objectives for optimization.
- Technology Adoption: Invest in the right mix of technologies, such as CMMS (Computerized Maintenance Management System), IoT sensors, and analytics platforms, to enable predictive maintenance and real-time monitoring.
- Process Redesign: Reengineer maintenance processes to align with best practices in RCM and TPM, ensuring efficient and effective maintenance activities.
- Skill Development and Culture Change: Foster a culture of continuous improvement, where maintenance is everyone's responsibility. Invest in training and development to equip your team with the necessary skills for modern maintenance practices.
- Performance Measurement: Implement KPIs (Key Performance Indicators) to track the impact of maintenance optimization on operational performance, cost savings, and equipment reliability.
The Role of Leadership in Driving Maintenance Optimization
- Communicating the Strategic Value: Articulate how maintenance optimization aligns with the company's strategic objectives and bottom-line benefits.
- Providing Resources: Ensure adequate financial, technological, and human resources are allocated to support the optimization initiatives.
- Fostering Collaboration: Encourage cross-departmental collaboration to break down silos and integrate maintenance optimization into the broader operational strategy.
Conclusion
Supplier Spotlight
Bel-Ray 2780 Waterfront Pkwy. E. Dr., Indianapolis, IN 46214 317-328-5660 | BelRay.com/industry/industrial/
Bel-Ray® Total Performance Lubricants take care of your production line as well as your bottom line. Trusted for over 75 years across a wide range of industries, our high-performance industrial lubricants are formulated to reduce energy consumption, reduce wear and tear, so you cut down on maintenance and downtime, while extending the life of your equipment to help lower your Total Cost of Ownership.
Noria Academy 1328 E. 43rd Court, Tulsa, OK 74105 800-597-5460 | Noria.com/Academy
Obtaining certification can be a challenge; new terms, concepts and topics can overwhelm even the most experienced reliability professionals. Training experts all agree that extending the learning beyond the classroom dramatically increases knowledge retention. To aid in this retention and create an innovative student experience, Noria is pleased to offer the Noria Academy app.
LubePM 1328 E. 43rd Court, Tulsa, OK 74105 800-597-5460 | LubePM.com
As a Lubrication Management System (LMS) engineered by lubrication professionals, LubePM helps an organization create accountability to ensure that every lubrication point is carefully maintained, inspected and measured. Ready to take your facility’s Lubrication Management System to the next level with LubePM? We’re ready to help. Simply request more information or schedule a demo.
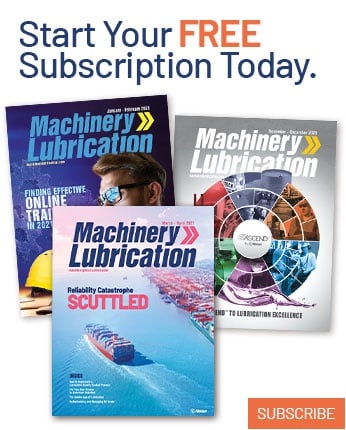