Digital transformation is a crucial aspect of staying competitive in the manufacturing industry. However, embracing and implementing it can often be an uphill battle, especially if employees resist the change.
Let’s explore a few strategies and techniques for overcoming resistance to digital transformation in your organization.
No. 1: Message and communicate transparently
Developing a strategic plan and consistently communicating the steps required to achieve the desired future state is essential. It is crucial to involve front-line employees in the digital transformation process, as management initiatives impact them directly. This not only ensures employee buy-in but allows for an understanding of any potential challenges or roadblocks. You can do this through implementing crew-level training and education programs — keep in mind that upskilling the digital workforce is all about continuous learning.
Additionally, a part of consistent messaging and communication involves aligning the transformation strategy with business goals. Conduct a comprehensive assessment of overall organizational objectives in the short, medium, and long term. Determine the technology that can support and enable the achievement of these objectives.
For example, if the primary focus of the organization is to expand to new markets rapidly, it may be more prudent to prioritize the establishment of a robust cloud infrastructure. This will support mission-critical processes from multiple locations rather than burning money on AI technologies.
This approach ensures that the technology investments align with the overall business objectives and support the organization's ability to achieve its goals.
No. 2: Engage stakeholders and leadership
Once the potential benefits of digital transformation in support of organizational objectives have been identified, it is crucial to engage stakeholders early on in the change process. Digital transformation can significantly impact how business functions are executed, including the roles, responsibilities, and processes of individual employees, as well as the interactions and collaboration between teams.
It is essential that everyone — from the boardroom to the shop floor — understand the rationale behind the investment in digital technologies, to foster buy-in and mitigate potential resistance to new processes. This is particularly important when implementing digital technologies to automate tasks or when ROI isn't immediately evident.
For example, consider setting up a steering committee, task force, or oversight forum with empowered representatives from different departments across all levels of the organization. These forums can help garner input and feedback, as well as provide a sense of ownership and accountability for the success of digital transformation at an organizational level.
By involving key stakeholders in the process, employees will be more likely to support the changes and be more invested in the success and outcome of the digital transformation roadmap. Engaging stakeholders also helps to identify any potential roadblocks or challenges that may arise during the process.
Setting clear expectations, holding oneself and others accountable, and demonstrating decisive action are all key components of effective leadership in any change-management process. Bear in mind that the leadership’s actions and goals are monitored too. Any deviation from stated expectations can undermine the change effort.
No. 3: Implement a CMMS
A Computerized Maintenance Management System (CMMS) can assist in the transformation process by digitizing maintenance schedules, inventory management, and other key operations in one centralized platform. This can help improve efficiency, reduce downtime, and increase overall productivity.
Additionally, a CMMS can also provide real-time data and analytics to help decision-makers identify areas for improvement and optimize operations, such that you can truly implement smart maintenance.
For example, a CMMS, integrated with smart sensors, and IoT, can enable condition-based or predictive maintenance in your plants, such that equipment degradation is proactively identified, with maintenance planned, scheduled, and executed before consequential failures. This can be in the form of online vibration monitoring on rotating equipment, where smart sensors will continuously monitor the vibration levels.
Predictive modeling will predict failure based on system conditions combined with vibration parameters, and a CMMS will initiate work requests, allocate resources, and background tasks and schedule them before the anticipated failure date. By implementing a CMMS, employees on the shop floor will be able to directly see and experience the tangible benefits of digital technologies and potentially be more likely to support them.
No. 4: Gradually scale up
Don’t implement all new technologies and processes at once. Begin with a pilot project or small-scale implementation and demonstrate their successes before moving on to the bigger projects. This allows you to test and adjust before fully committing to the whole nine yards of digital transformation.
By starting small, your employees will also be more likely to adapt to the changes, observe the small gains, and ultimately, be more open to further digital transformations in the future. Gradual scaling up allows you to continuously improve and optimize the technology, reduce the risk of failure, and increase the chances of success in your digital transformation initiatives.
No. 5: Measure progress and desired outcomes
To ensure that the digital transformation is delivering the desired outcomes, it is important to set performance metrics and Key Performance Indicators (KPIs). An excessive number of KPIs can lead to ambiguity and impede progress. Therefore, it is essential to focus on a specific set of KPIs that align with the unique objectives and requirements of the organization.
To effectively create and choose the appropriate KPIs for digital transformation, the following best practices should be considered:
- Identify KPIs that can be easily quantified and comprehended by non-technical stakeholders.
- Ensure that KPIs are tailored to the specific needs and expectations of the intended audience.
- Clearly define the expected business outcomes or benefits that the KPIs aim to achieve.
- Take into account the current state of the organization and the desired end-state when determining KPIs.
- Set achievable goals for KPIs, to avoid overburdening the team or setting them up for failure.
It is important to note that KPIs can also serve as both leading and lagging indicators. Leading indicators, such as the rate of technology adoption and user experience, can provide immediate feedback on the success of digital transformation initiatives.
In contrast, lagging indicators, such as downtime, Overall Equipment Effectiveness (OEE), Mean Time to Failure, and Mean Time Between Failures (MTTF/MTBF), may take longer to reflect the impact of digital transformation strategies. It is crucial to keep this distinction in mind when selecting and monitoring KPIs to evaluate the effectiveness of digital transformation efforts.
Parting Thoughts
Overcoming resistance to digital transformation in a manufacturing plant can be a challenging task, but it is essential for staying competitive in an ever-evolving dynamic business environment. By clearly communicating the benefits of digital technologies, involving stakeholders in the process, implementing a CMMS, and starting small, manufacturing plants can effectively embrace digital transformation.
These solutions will ultimately aid in automating production lines, optimizing supply chains, and providing intelligent data that enables organizations to respond quickly to shifting consumer demands.
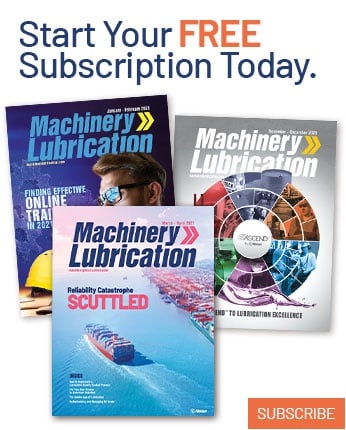