Have you ever seen Rocky IV? In this 1985 hit movie, Rocky, an American boxer played by Sylvester Stallone, is challenged to fight a rough and tough Russian opponent who seems to have all the odds in his favor.
In preparation for the fight, Rocky travels to the Soviet Union to train waist-deep in the Siberian snow using only the bare essentials. Meanwhile, his opponent, Ivan Drago, is given every advantage in the book, including a team of experts who measure and record his every action and physical change with what appears to be near NASA-like technology for that day and age.
But against all odds, and some of the greatest technology of the time, Rocky defeats his opponent and once again secures his champion title, due in large part to his exceptional understanding of the foundational principles of boxing, his resolute preparation style, and his unwavering dedication to his training.
While Rocky IV is a work of fiction, it highlights a valuable life lesson that should resonate with all of us. Technologies, like computer maintenance management systems (CMMS) and artificial intelligence (AI), can be excellent resources to propel you to greater levels of success within your company and the industry, but these tools can easily become your downfall without the proper training and mastery of maintenance and reliability best practices.
Case Studies: Failed Technology Implementation
Case Study #1: CMMS Solution
One company I am currently working with is in the process of upgrading their facility’s CMMS program. They mistakenly believe that the new software alone will solve all of the issues that their maintenance and reliability program is currently facing. These issues include:
- Poor prioritization of work orders
- Poor planning of work orders
- Lack of preventive maintenance execution and documentation
- An incomplete Bill of Materials
- A large backlog of work
- High maintenance cost
- Poor reliability
The price tag for their chosen CMMS solution is more than $10 million. At this scale, failed implementation would have a severe negative ripple effect and could potentially cause:
- A shift of focus, allocating many resources to fixing the CMMS problem instead of improving reliability in the mill.
- A system that slows down maintenance work order process.
- Untrained people deciding not to use the system.
- Problems retrieving spare parts.
- A shift in attitude potentially leading to a disgruntled work force
- High administration costs of the system and the data
These issues not only pose a real threat to the company’s current bottom line, but also their success potential for generations to come.
Case Study #2: AI Solution
A mill site I previously worked with allocated millions to install an AI solution that would monitor and provide a statistical analysis of equipment temperature and vibration levels. What they didn’t consider is that AI solutions must have clean and accurate date, then be trained on what to monitor before they can function independently. As a result, their new system generated an overwhelming number of alerts.
In fact, when the system first became operational, there were so many alerts being generated that it would have taken the site more than doubling its maintenance staff to resolve all the issues and check on the additional alarms. In addition to this, because the site was trying to implement the AI solution to solve their problems, not achieve their objectives, they still had a large backlog of work that needed to be completed but couldn’t be because management wouldn’t approve the necessary budget to cover the repair costs.
They simply bought into the belief that the AI digital monitoring equipment was a great idea, but they hadn’t considered how the additional condition monitoring would affect the rest of the work process or if the technology would generate a return on investment (ROI).
The result was an even larger backlog of maintenance work and a colossal bill from Amazon to store all of their new data.
Establishing Maintenance and Reliability Fundamentals First
Technology is a tool, not a replacement for good practices. While it can accelerate maintenance improvements at your organization, it can never be an actual improvement by itself. If you want something to improve, you must do the work and do it well.
Right now, it feels like we as an industry have completely forgotten this fact. There seems to be blind faith in technology. From trade shows and media outlets to subject matter experts and solutions providers, it seems there is a growing tendency to indiscriminately promote the latest sensors, software, and applications without first considering if they will generate a good ROI or what our facilities must have in place to make these tools successful. This not only lends itself to suboptimization, but it puts the entire future of our companies at risk.
To have a chance at successfully implementing technologies, a facility must first have:
- Good work practices in preventive maintenance, planning, scheduling, RCFA, and materials management
- Accurate master data, such as equipment numbers and Bill of Materials.
Once these are implemented and a solidified part of our facility’s maintenance and reliability culture, we can then evaluate whether the solutions would provide a favorable ROI. Factors that determine if an investment will provide a good ROI include if they will:
- Make the workforce more efficient.
- Reduce the number of failures in the plant.
- Prolong equipment life.
- Reduce costs through automation.
When you begin implementing these new technologies at your facility, it’s crucial to remember that they aren’t meant to solve your problems, they are designed to be utilized in a way that helps you reach your objectives. These objectives must be clearly defined and understood by all stakeholders before technology implementation, otherwise, you’re spending precious company capital on a tool that will only create more issues.
Examples of facility objectives that technologies can help you reach include:
- Improve overall reliability.
- Reduce costs.
- Make the workforce happier.
- Increase the speed and accuracy in executing tasks.
Conclusion
We must be careful not to fall victim to the belief that technology alone will solve all our problems. We must first implement solid maintenance and reliability practices and procedures before investing our time and resources; if we do this, technology can be a great tool to help accelerate improvement and growth. Otherwise, we will be forced to improve processes with whatever capital budget is left after the technology investment, which is often nothing.
To achieve a successful and reliable facility, we need to do the work, just like Rocky. Don’t rely on technology or digital transformation to fix all your problems. Master the basics and utilize technology for what it is – an enhancement rather than a solution.
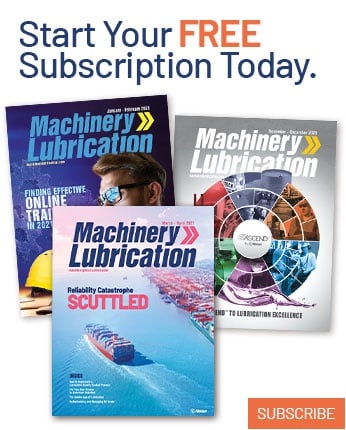