The competition for talent has been intensifying for years. Despite talk of economic downturns, unemployment rates worldwide are at unprecedented lows, and businesses in every sector are experiencing difficulties in finding skilled individuals to fill positions. Good maintenance and reliability professionals are becoming increasingly difficult to find and retain.
But, with the help of a CMMS system, a company can improve its practices and culture, helping to make it a more desirable place to work than its competition. Finding and retaining quality employees is all about creating a mutually beneficial relationship for both parties, and by doing so, we guarantee the continued success of our facilities and team members.
Attracting and Retaining Quality Employees
Many workers are re-evaluating their career paths since the pandemic. The average employee turnover will hit 30% in 2023 as employees move for better working conditions or new careers.
That means employees will move on after an average of only three years. When an employee leaves, it costs about 33% of their annual salary to replace them, so it makes sense to do what you can to retain existing team members.
Did You Know?
77% of manufacturers report having ongoing difficulties attracting and retaining workers.Source: Harver
Regardless of how well-paid the role is, nobody wants to be on board a sinking ship; everyone wants to be part of a winning team. That means working with great people in a company with a positive workplace culture in a role that challenges you daily. Companies with happy employees have a 51% lower turnover rate and are more successful at attracting new talent.
Maintenance managers are increasingly seeking innovative ways to increase maintenance roles' attractiveness for current and prospective employees. They invest more in their people through training and upskilling, continually examining the work-life balance, and ensuring competitive employee compensation packages.
They are also evaluating the maintenance organization itself.
- Is this a great place to work?
- Do we give our technicians all the necessary tools to do the role?
- Do we have the right systems and processes to make them successful?
- Are the maintenance technicians happy to come to work each day?
The many benefits of Computerized Maintenance Management System (CMMS) software have been widely documented over the years, such as:
- Improved regulatory compliance.
- Increased safety.
- Efficient work order tracking.
- Automated preventive maintenance scheduling.
CMMS software can help elevate the work environment. Implementing a CMMS is also an excellent way to improve company culture, as it can help to create a more transparent, efficient, and collaborative work environment.
Every day, more and more companies are looking to invest in a CMMS to help mitigate talent acquisition and retention challenges.
Here are seven ways a CMMS helps hire and retain quality employees.
Reason #1: Basic Organization of Maintenance Operations
A new hire's motivation and excitement will quickly disappear once they realize the organization lacks the tools to make them successful. Running a maintenance department without a CMMS is like running a hotel without a proper booking system. Not having the right tools and systems for the job increases stress and frustration. In addition, the employee's perception of the maintenance leader and the company drastically decline.
Today, technicians expect to have the tools to complete their tasks efficiently. When employees have the tools and resources they need to perform their best, it positively impacts job satisfaction, engagement levels, and company culture.
CMMS software helps:
- Plan and schedule maintenance activities.
- Manage work orders.
- Track inventory.
- Monitor equipment performance.
Having a CMMS in place means steering the ship is more manageable and makes the technician's role more predictable and engaging.
Reason #2: Performance Enablement
By providing a centralized platform that streamlines maintenance and asset management processes, a CMMS helps optimize performance across the entire organization. Employees can easily access critical information, making them more effective in their roles and boosting overall productivity.
Furthermore, a CMMS offers features for tracking performance metrics, setting goals, and providing feedback – all essential components of an engaging workplace. Performance enablement is crucial for cultivating a great culture, as it empowers employees to make data-driven decisions and visibly contributes to the company's success.
Reason #3: Democratization of Information
CMMS software helps to democratize information by making critical data available to all relevant stakeholders – from technicians and managers to executives and business partners. This open-communication model fosters collaboration and knowledge-sharing, leading to innovation and more efficient problem-solving.
A CMMS provides a centralized platform where team members can:
- Monitor asset performance.
- Review maintenance histories.
- Manage work orders.
This transparency helps build employee trust and promotes a more inclusive and cohesive working environment.
Reason #4: Limit the Impact When Technicians Leave
When employees leave the organization, 70% of their knowledge walks out the door with them. Great leaders ensure minimal or no impact when key individuals leave the organization. The easiest way to limit the amount of knowledge that leaves is by capturing as much knowledge as possible during day-to-day operations.
CMMS software is the best way to do that. Knowledge and information from the floor are captured within the CMMS system when end users complete work orders and document repair notes. That way, a substantial amount of the information and knowledge remains in the organization when employees leave.
Reason #5: Speed Up Onboarding
When new hires join the team, having all that information at their fingertips will speed up the onboarding process, ensuring minimal overall impact on the organization. That's where CMMS software comes in.
A properly configured CMMS software is like a manual for the equipment in the plant. Checklists and procedures in the CMMS outline the steps needed to perform different jobs. The technicians can also search work order history at the plant for similar issues, speeding up the troubleshooting process.
Reason #6: Create a Safer Place to Work
A basic human need is to feel safe in their surroundings. The same is true in the workplace. Employees seek safe equipment, procedures, and environments to conduct their work. A safe environment can improve employee engagement, loyalty, morale, and productivity.
Maintenance leaders can use CMMS software to help create a safer working environment by:
- Documenting all procedures in standardized checklists
- Tracking all safety work orders
- Focusing on planned maintenance and the associated reduction in emergency repairs.
Reason #7: The Latest Technologies
The younger generations are more concerned with career growth and want to work with the latest devices and cutting-edge technologies. They don't want to work with outdated CMMS software built on 20-year-old technology. They want to work with the latest CMMS applications on mobile devices. Keeping technology current is crucial in retaining those people.
Conclusion
Computerized Maintenance Management System software is crucial in creating a culture that helps attract and retain maintenance staff. This software allows maintenance staff to manage and track maintenance operations efficiently, from work order creation to completion.
By utilizing CMMS software, maintenance staff can increase productivity and reduce time spent on administrative tasks. Being efficient and productive can increase job satisfaction and a sense of accomplishment among maintenance staff.
Additionally, CMMS software provides a central repository for all maintenance-related data, including equipment history, inventory, and maintenance schedules. This helps maintenance staff to prioritize and plan their work, resulting in better time management and fewer work-related stressors.
Overall, CMMS software can significantly contribute to the retention of maintenance staff by enabling them to work smarter, not harder.
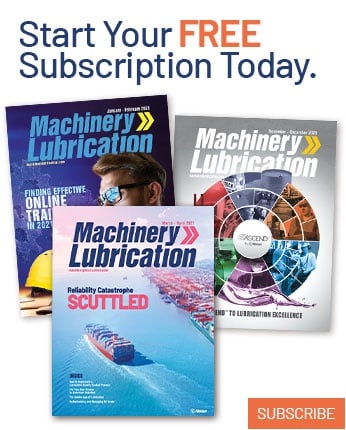