Functional failures in plant equipment are unavoidable. However, the way a company handles its asset failures can have an impact on its annual maintenance budget’s bottom line.
For example, a company that fixes issues after they occur or has Proactive Maintenance technology and processes in place that reduces the occurrence of surprise failures will both have higher costs associated with them. The difference lies in how long they will hold these higher costs and what the outcomes will be. Let’s take a closer look.
Reactive Culture
Reactive maintenance, as the name suggests, means fixing something when it breaks. When a company remains in a reactive state, it can quickly spiral into a bad situation where maintenance costs are doomed to pile up. For example, purchasing will continuously expedite the parts needed for repairs and overhauls that aren’t in inventory.
To avoid this, some companies will keep a larger stock of spare parts, which only serves to drive up inventory and storage costs. Millwrights will also have to work longer shifts to “put out the fires,” which equates to increased overtime pay for the company and longer hours for the staff while still having to keep up with their routine tasks. Working long hours and consistently performing unplanned work can cause undue stress, leading mechanics and millwrights to lose focus and potentially overlook safety hazards.
In a reactive environment, unplanned downtime is king. This greatly increases costs, decreases production, and fosters collateral damage through catastrophic failures in the rest of the system.
Proactive Culture
Proactive Maintenance means doing everything possible to prevent failures before they occur. Running a plant in the proactive domain is proven to lower costs, reduce safety risks, and run systems more efficiently.
Given the initial capital investment required to execute this strategy, which includes obtaining additional maintenance tools and technologies, training employees, and determining and monitoring equipment condition baselines, proactive maintenance typically results in a short-term increase in maintenance costs. However, this increase is short-lived, and the profitability from the increased production and greater efficiency and reliability will outweigh the initial costs.
The costs are also reduced as reactive maintenance decreases through the active prevention of failures and as preventive maintenance tasks are replaced by intelligent condition monitoring strategies. This results in a significant reduction in expensive unplanned downtimes, spare parts consumption, inventory costs, labor costs, and overall maintenance overhead.
One way to maintain a proactive culture within your maintenance department is to assign trained personnel to planning and scheduling. Too often, the responsibility falls to one individual when it should be split into two separate roles (depending on the size of the plant.) I have visited numerous sites throughout the United States, and not one has lacked maintenance tasks for its millwrights because of the separation of duties. This is a key indicator that these two positions are needed.
Planning and Scheduling
Planning is a key component of a good reliability program. It generates more time for the technician by increasing the efficiency of each task through good job plans and properly written procedures. Proper planning also involves coordination with the MRO Stores department to ensure that a kit of the appropriate tools and parts for the planned job is available and delivered in a timely manner to the job site. This avoids the noncompletion of assigned tasks due to incorrect or missing parts and tools.
Scheduling involves detailed coordination with the Operations, Production, MRO Stores, and Maintenance departments to ensure that the timeline of a scheduled task meshes perfectly with each of these departments’ needs and constraints. This also ensures that scheduled tasks occur smoothly, within the scheduled timeframe, and with all the necessary allocated resources, both physical and human. This is a key component of efficient reliability and accountability, and it ultimately boosts profits.
Conclusion
A company's approach to asset failures can significantly impact its maintenance budget and overall profitability. A reactive maintenance culture means fixing equipment when it breaks down, resulting in costly unplanned downtime, increased inventory costs, and potential safety hazards for personnel.
On the other hand, a proactive maintenance culture involves doing everything possible to prevent equipment failures through condition monitoring and precision maintenance tasks, resulting in increased short-term maintenance costs but long-term savings from increased production and greater efficiency.
To maintain a proactive culture, it is crucial to assign trained personnel to planning and scheduling tasks, which involve proper job plans, coordination with MRO Stores, and detailed coordination with the Operations, Production, and Maintenance departments. This not only increases the efficiency of each task and reduces the risk of noncompletion due to incorrect or missing parts and tools, but also boosts accountability and profitability.
In conclusion, investing in a proactive maintenance culture and efficient planning and scheduling is an investment in the company's long-term success.
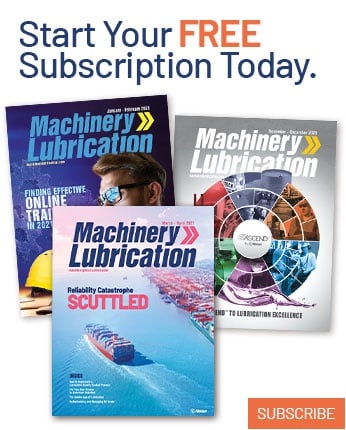