Physical asset management is more than just keeping critical machines up and running. It’s creating a lasting culture of continuous improvement that utilizes leading reliability principles, such as preventive maintenance, to reduce waste and improve productivity. In doing so, we master the art of risk management and develop ownership over our equipment. This ownership guides our daily maintenance decisions and demands action that positively impacts the future health and useful life of our critical assets.
Determining what action to take and which maintenance activity to prioritize is a key aspect of physical asset management; consult data available from key performance indicators and your equipment’s unique PF Curve to help make an informed decision. These tools help detect anomalies quickly, and the quality data provided is helpful in developing and supporting an effective action plan. In partnership with these continuous improvement efforts, we begin to develop a lean manufacturing process supported by well-maintained equipment.
For example, with lubrication, proper greasing techniques establish the foundation for all other maintenance activities. With nearly 90% of bearing failures being lubrication-related, greasing practices can’t be overlooked. Continuous improvement efforts also affect our current processes by forcing us to identify opportunities to remove waste, such as with the single-minute exchange of dies, which transformed from a complex hours-long procedure to a simple ten-minute process.
Minimizing waste within the status quo of our operations leads to lasting change when paired with the right actions and appropriate policy modifications. These changes affect not only how we view and care for our physical assets but the way we define success and productivity within the industry.
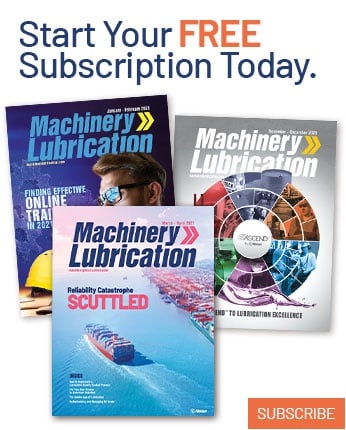