How do you initially train someone new to the planner/scheduler position? First, let’s talk about the selection process, as I see this as an issue in many organizations. Ideally, the planner/scheduler should be one of your best craftspeople. You have to compensate the position at a level at least equal to your first-level supervision. The compensation should include accounting for the average overtime earned as a craftsperson if you expect them to apply for the position. You will not get many applicants if you are asking them to accept a significant reduction in their pay.
In addition to being a highly skilled craftsperson, the candidate should have good computer skills, a positive attitude, people-oriented and be self-motivated.
After you have identified the right person, the obvious next step is to get that person trained. You generally have a couple of choices here. You can send them off to a class, or you can host an on-site course.
This brings us to another question. How do you help guarantee success with planning and scheduling? Realize that you can send a planner/scheduler off to training, have them return and, despite their best efforts, the organization will not allow them to plan and schedule work. Providing the on-site course will allow you to educate supervisors, team leaders, managers, engineering personnel, production supervisors, production planners and anyone else who interacts with the maintenance work management process. Now everyone can understand not only the roles and responsibilities of the planner/scheduler, but also their own roles and responsibilities in relationship to the work management process.
When I teach maintenance planning and scheduling classes, I want to share a number of approaches. There are a several methods and opinions on how to plan and schedule work. What I find is that some groups actually do a disservice to their course participants by not sharing a comprehensive approach with various methods.
After the initial training is complete, recognize that you are only one-third to halfway done. After about one to two months, it’s time to bring in a coach. Ideally, the coach is an external resource who walks a mile beside the new planner/scheduler. The purpose of this is to observe the activities of the planner/scheduler and also the interactions within the organization.
When I coach and mentor, I’m looking to determine if the planner/scheduler is applying the items learned in the class. Are they creating job plans? Is the continuous improvement loop in place? Is the planner/scheduler focused on the future?
Next, I’m looking to see how the supervisors are interacting. Do they understand their roles and the planner’s roles? Are work orders being completed and data entered into the CMMS? Is the organization aligned for proactive scheduling? These are just a few of the items that I address in my coaching sessions.
The number of coaching sessions depends on the organization. It may only be one to two in total. Now, about retraining, a number of organizations bring me back on a semi-annual to annual basis to provide an overall best practices health check as a good method to determine if the organization is continuing to mature in its implementation efforts. If it has gone stagnant, I’ll point out the obstacles and help get them back on the road to success. Ultimately, this is my primary goal. I have a passion for maintenance and operations, so I really care about people being successful.
If not an external resource, someone internally needs to remove the obstacles to ensure effective planning and scheduling.
With respect to retraining, you should always be in a state of constant learning. That means reading articles and attending events that foster learning.
During a two-day maintenance management course in California’s wine country, I met a planner/scheduler who attended the course the previous year. At the end of the course, I asked him why he chose to re-attend so soon afterward. He mentioned that he had forgotten a number of items, and the main one was creating job plans. Wow! Besides scheduling the work, this is one of the most important parts of planning and scheduling. This example highlights the need for retraining, especially if you opted not to provide coaching.
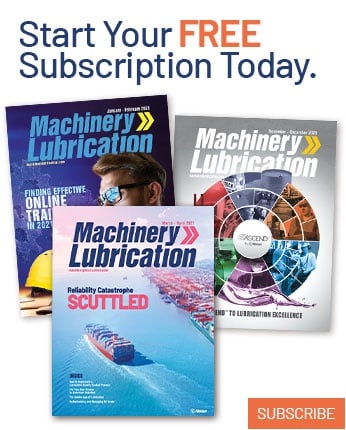