Several years ago, I spoke at a conference in Australia about the Fox versus the Hedgehog approach (Reference: Jim Collin’s book Good to Great. Published 2001). I based the presentation on an IDCON survey that asked respondents if their organization was a Fox or Hedgehog. The survey results showed that only 16.7% of respondents thought their company was a hedgehog company. The rest viewed themselves as Fox or a mix of Fox and Hedgehog organizations.
This means most organizations are taking a short-term approach to cost reduction and savings. In the long term this is very costly. I frequently see examples of this at client organizations. One common example is that cost reduction initiatives focus almost entirely on visible cost reductions while overlooking or ignoring the waste built into the day to day work system.
Let me give you some examples from a big paper mill’s shutdown. I hope you do not recognize these examples at your organization, but if you do, you certainly are not alone.
It was common that operations and maintenance shutdown schedules were wide open until the morning of the shutdown.
Does this seem familiar?
The area shutdown was estimated to require ten hours to complete all the necessary work.
In order to cut costs, the shutdown was restricted to eight hours, so some work had to be postponed. To bring in more contractors to complete all work necessary would cost too much visible money.
“Perhaps we can run the three rotary steam joints until next shutdown, they aren’t leaking…yet. We know, from the PM inspection reports, that the carbon rings in these joints only have about 1/8” thickness left but we can take the risk” was one suggestion. So, these jobs were cancelled along with some other work deemed as not urgently needed.
During the mid-shutdown meeting, the operations manager added three forgotten jobs that weren’t put on the maintenance schedule before the shutdown. This delayed the start up by three hours.
The coupling for one dryer section drive was to be replaced. After pulling the coupling off the shaft it was discovered that the coupling was not requested from the store. When it was found, it was not prepared to the right shaft diameter, and the key way didn’t fit. This was one of the last jobs, so no time was given to prepare coupling properly. The old coupling was put back and welded together to be fixed right later.
At start up, the steam system was started too fast resulting in a lot of water hammer in pipe systems.
A consequence was that two of the three carbon rings in the rotary steam joints cracked and the joints started to leak. They could be shut-off, but this would result in a 10% slowdown of production speed.
Also, the cost of repairing the joints went up by 10 times because of the damaged seal surfaces. The coupling lasted through the startup but was forgotten and three months and three shutdowns later, the bearings in both motor and gearbox failed. The welded coupling was too stiff and also misaligned.
This resulted in six hours of unscheduled lost production and additional maintenance costs.
The root of the above examples of waste is poor discipline in prioritization of work, failure to act on PM inspection reports, lack of closing time for shut down schedules, the ease of adding on a job even during a shut down, lack of planning of work, etc.
But it had always been this way in this organization, so the waste was known and accepted.
The fix to the problem will take time, because it includes a cultural change.
“Right now, we have to save what we can in the short term. We don’t have time to deal with this, and on top of that, it will cost money to improve our work system” were common sayings at this organization.
The time and cost to improve is visible cost, the existing invisible waste is embedded in the work system. So instead of improving long term and saving long term waste, the visible short-term cost saving initiatives takes over.
Other visible short-term cost savings I’ve seen include: Cancelling training programs, reducing the of number of planners and supervisors, postponing needed maintenance work, reducing the number of lubricators and handing this important task to operators without training.
It is understandable that costs must be reduced, this is needed to survive.
To sustainably improve and stay competitive, plants must take a more long-term approach to improvement initiatives. The short-term savings will often worsen the situation within a three to five years perspective. A long-term cultural change initiative will improve performance substantially but could take three to five years to come to fruition.
For more information visit www.idcon.com
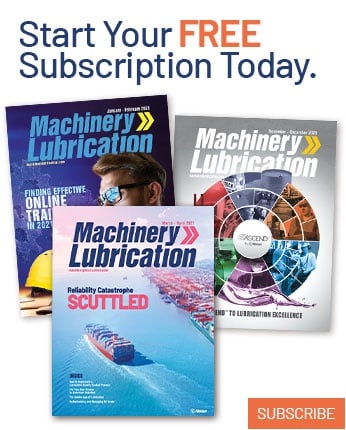