Preventive maintenance (PM) is an integral component of successful asset management. Companies that rely on mechanical equipment to remain operational, and even businesses that utilize mechanical assets in a support role, must ensure these items remain functional and "healthy" day after day. Effective planning and scheduling play a crucial role in the ultimate success of any preventive maintenance program. The following information will discuss how to optimize these two areas.
Scheduling: Fixed vs. Floating
When it comes to preventive maintenance scheduling, you must decide whether to implement a fixed approach, a floating one or a combination of the two methodologies. What are the differences between these two frameworks?
A fixed PM schedule requires the performance of certain tasks between regular, pre-defined intervals. For instance, a fixed schedule may mandate that a production machine receives an inspection every Monday, or that a system's filter is replaced on a monthly basis.
A floating schedule allows for greater flexibility as to when maintenance tasks are performed. It is based on prioritizing needs over preset routines. Thus, a floating schedule may allot some time for a filter inspection; however, if the filter is still in good shape, then there would be no mandate to immediately replace it.
You can think of the difference between fixed and floating schedules as the different approaches to changing a car's oil. Some vehicle owners change the oil every two to three months without exception, while others wait to reach a certain mileage threshold instead.
Each approach has its own unique benefits. A fixed schedule can effectively spread out a large volume of tasks evenly among an organization's maintenance force. Fixed scheduling also makes it less likely that routine, yet critical activities will be overlooked. In many cases, a fixed scheduling program ensures that warranties are not prematurely revoked by original equipment manufacturers.
In contrast, a floating approach allows for the greatest degree of schedule flexibility, especially when certain tasks are not immediately critical to a machine's continued functionality. Floating schedules also allow the maintenance team to spend more time assessing risk and prioritizing critical areas.
Understanding and utilizing these two scheduling methodologies, perhaps in a hybrid approach, will help you optimize your preventive maintenance program.
Planning Principles
It is also crucial for PM-conscious organizations to embrace and implement fundamental planning principles to achieve the best results. Here are five key principles to keep in mind:
Employ a Dedicated Planner/Set Aside Planning Time
Companies that have successful preventive maintenance programs understand the importance of tasking either a single employee or a dedicated team with the program's planning duties. Failing that, the maintenance team member who currently handles planning activities should at least have sufficient time to focus on this vital job without worrying about unnecessary distractions.
Ensure Instructions Are Standardized and Clearly Documented
Without standard procedures in place, it may be next to impossible for a planner to estimate the amount of time needed for any given maintenance task, especially if more complicated repairs are needed. Therefore, it's essential for an organization to develop and disseminate standard plans (at least for common maintenance activities). These standard plans can always be updated and improved at a later time.
Plan for the Lowest Skill Level Required
Once a planner receives news of a high-priority task and analyzes the relevant instructions, he or she should generally allot the amount of time required for a technician with the minimum required skills and experience to successfully complete the task. If it actually takes that long to complete the task, then the program remains on schedule; if the technician finishes the work early, all the better.
Take Auxiliary Tasks into Account
All too often technicians spend a large chunk of their time on necessary tasks that are only indirectly related to actual maintenance projects; e.g., searching for the correct tools, hunting for parts, waiting on permits or supervision, etc. While these activities are not necessarily considered part of the maintenance task, it is still wise to leave some wiggle room in the schedule for the intrusion of reality.
Prioritize According to Urgency and Importance
Many planners use the failure mode, effects and criticality analysis (FMECA) model to determine which tasks should be given top priority. For instance, a relatively unimportant piece of machinery may require urgent repairs; however, if absolutely critical production equipment is due for scheduled maintenance, then it may take precedence over any other activity.
Other Preventive Maintenance Tips
In addition to the above information, here are three other helpful suggestions for implementing an exceptional PM program:
Utilize Asset Tracking Software
Since so much allocated maintenance time is spent on locating the correct tools and parts, consider tagging each relevant piece of equipment with a digital tracking device. Then, with some help from specialized software, your employees will be able to locate the needed assets at a moment's notice.
Leverage Maintenance Management Software
An effective computerized maintenance management software (CMMS) platform can give you a high-level view of current and projected maintenance needs while facilitating the scheduling and work order process.
Train Your Team to Interpret, Implement and Record PM Data
A tool is only as good as its user. Thus, bring your maintenance team onboard the PM program by educating them on how to most effectively interpret and implement a given work order. Also, be sure to teach them the best practices for recording data.
If you deploy the above-mentioned suggestions in a strategy tailored to your organization's unique circumstances, you should enjoy a more effective, streamlined and impactful preventive maintenance program.
About the Author
Egle Segzdaite is the digital marketing manager for Dynaway. She can be contacted via email at egs@dynaway.com.
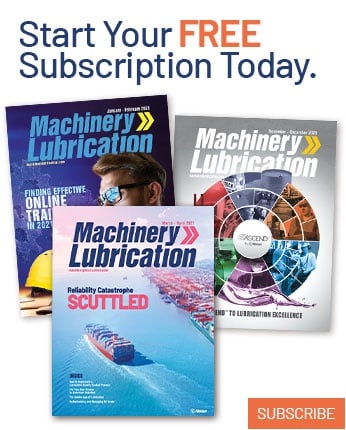