Maintenance teams often need to have difficult conversations if they rely heavily on a reactive maintenance strategy. Even the most experienced teams view reactive maintenance as an ad-hoc task. However, when used optimally with preventive and predictive maintenance, reactive maintenance can drive down costs and improve your maintenance regime.
Reactive Maintenance Defined
Reactive maintenance, also known as breakdown or run-to-failure maintenance, refers to repairs that are completed when equipment has already broken down. Since the repairs aren’t planned, this type of maintenance is normally employed for equipment that is not essential for operations or has a low enough cost to replace it routinely.
There are benefits and disadvantages to using reactive maintenance as the only form of maintenance. It requires less standby manpower, planning and initial cost than other maintenance strategies. On the other hand, it can make it difficult to create a budget and there might be large disruptions of workflow when maintenance issues pop up unplanned, leading to poor time management, loss of production, and distractions and disorganization in the workplace.
Generally speaking, it takes less money and time to wait for equipment to break down then it does to perform routine maintenance. This is reactive maintenance. However, using reactive maintenance on its own is a very short-sighted approach. It can play an important role in a maintenance strategy for emergency situations, but it should not be the focus of the entire operations and maintenance plan. Relying exclusively on reactive maintenance is not sustainable in the long term. For assets that are critical to production, quality, safety and service delivery, it’s better to opt for a maintenance routine that includes elements of routine maintenance, preventive maintenance and predictive maintenance. This is why using this strategy in conjunction with a preventive or predictive maintenance schedule may provide the best results.
Preventive Maintenance as a Strategy
Preventive maintenance involves periodically taking assets offline to inspect or repair them at prescheduled intervals. The goal of this type of maintenance is to extend the useful life of the assets and prevent breakdowns from occurring. Just like with reactive maintenance, there are benefits and disadvantages with preventive maintenance. The major benefit is being able to plan when maintenance is performed to cut down on budget restrictions and loss of production. The major disadvantage of preventive maintenance is the schedule. Since the schedule is repetitive, employees can get tired of performing the same mundane tasks over and over, and may overlook maintenance issues or not perform their duties properly. This can lead to failures and cause the plant to implement more preventive maintenance, creating a vicious cycle of poor maintenance.
Predictive Maintenance as a Strategy
With predictive maintenance, the aim is to predict future failures before they happen, so maintenance issues are streamlined. This system uses sensors and smart technology to collect data. When the data shows a piece of equipment is failing, the system alerts the maintenance team before the equipment fails.
The benefits of predictive maintenance are the cost savings from reduced man-hours and more insight into the equipment’s performance. In addition, relying on sensors and the data they collect means maintenance is determined by the condition of the equipment instead of the best-guess schedule set by preventive maintenance.
The disadvantages of predictive maintenance are the high costs associated with implementing the software and sensors, as well as the extra work that may be required to get employees to use this advanced technology. The pros and cons for each type of maintenance strategy are shown below in the comparison chart by Fiix Software.
Mixing Reactive, Preventive and Predictive Maintenance
These three types of maintenance each have unique benefits and disadvantages depending on which asset is being monitored, at what stage of reliability the plant is, and the impact of downtime on the business. Since there are many downsides to reactive maintenance, organizations tend to move from reactive to preventive maintenance. This doesn’t mean that reactive maintenance can be completely eliminated. Situations will always arise that demand some sort of reactive maintenance. In spite of an organization’s best efforts and planning, the potential for equipment to break down or malfunction still exists. This probability can increase with the use of complex, sensitive or older equipment. Sometimes, a machine may be shut down for days after performing maintenance. In this case, reactive intervention can get processes running again.
Traditionally, maintenance professionals have combined various techniques, both qualitative and quantitative, to identify failures and mitigate downtime. However, the dilemma of which maintenance strategy to use has forced most organizations into a trade-off situation where they have to choose between optimizing the life of a part with the risk of machine downtime, maximizing uptime by replacing potentially good parts, and using past experiences to anticipate when breakdowns might occur. With the rise of new connected technology, machines can collect data and look for future or present maintenance issues, send out alerts, and order and schedule parts and maintenance, all without the help of employees, saving time and money. This is ideal for optimizing the life of machine components while avoiding equipment failure.
This is where reliability-centered maintenance (RCM) comes into play. RCM is a highly involved process that aims to analyze all the possible failures for each piece of equipment and customize a maintenance plan for each piece. With this strategy, all three types of maintenance are implemented in a way that is best for the equipment being monitored. According to RCM, less than 10 percent of maintenance should be reactive, 25 to 30 percent preventive, and 45 to 55 percent predictive. Enterprise asset management (EAM)or computerized maintenance management system (CMMS) tools can even help you identify the best mix of maintenance strategies for your site.
The overall productive capacity of a plant can be reduced between 5 and 20 percent by poor maintenance strategies. Recent studies have found that unplanned downtime costs industrial manufacturers an estimated $50 billion each year. It can be difficult to determine how often a machine should be taken offline to be serviced, as well as to weigh the risks of lost production time against those of a potential breakdown. Employing all three maintenance strategies in tandem can provide a real-time flow of information. This can allow for greater operational efficiencies by using data to drive maintenance action for all types of equipment.
About the Author
Prasanna Kulkarni is the founder and product architect of Comparesoft.
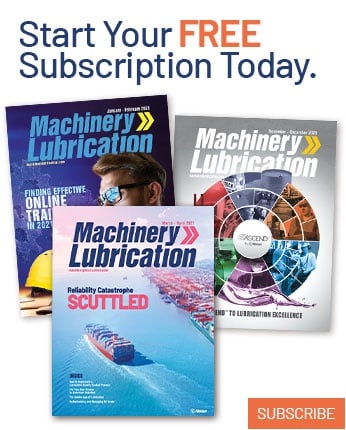