The Unilin Mohawk plant in Mount Gilead, North Carolina, has implemented a program to improve the reliability of its equipment using vibration, thermography, oil analysis, airborne ultrasound, laser alignment, field balancing and visual inspection routes along with online and portable data collection. This article will detail the company’s experience with these techniques to overcome obstacles and real-life situations.
Clean-up Fan
The fan below has a 52-inch wheel and a 422-horsepower motor. The equipment had problems in the past with the fan bearing seal, which allowed fiber to enter the bearing and cause bearing damage. On Jan. 10, 2018, the fan was found to be misaligned.
Note the two speed frequencies (motor and fan). An alignment job was performed on March 6, 2018, which found severe misalignment. After the laser alignment was performed, the equipment worked well for a short period of time.
Failure History
The fan was reported to have a bad bearing in the drive-end side on March 21, 2018. A work order was created based on the following waveform tendency.
Unfortunately, the plant didn’t have plans to shut down for maintenance until April 23, 2018. We began monitoring a fast-growing failure development and followed the four stages of bearing failures according to the Charlotte Technical Associates’ chart. We only reached stage 3 but performed an endurance test for the motor bearings. During one month, we discovered different failure stages with the following tendencies:
We had external race frequency failures with their harmonics (stage 3 of bearing fails) but never began stage 4. Above, you can see the speed spectrum for the day previous to performing the repair. You can clearly see the external race bearing frequencies and their harmonics.
Actual Condition
The equipment runs well now, and we have continued the monitoring program. The bearing suffered an extreme endurance test.
Conclusion
We cut the bearings and confirmed the diagnosis. After performing root cause analysis and checking the evidence, we concluded that the origin of the fault was due to misalignment.
Twin Fans
The West ID fan has a 350-horsepower motor, variable speed and dampers for regulating flow. The air is hot because it comes from the furnace to maintain internal pressure. The power transmission is by belts.
The East ID fan had a history of problems compared with its twin fan. It had a balancing problem, which can be seen in the spectrum and time waveform below.
With no time to perform a balancing job, the non-drive end failed on Feb. 12, 2018. To balance the fan, you must stop the furnace, which typically happens once a year.
The following jobs were performed on the fan:
- The right suggested bearing was locked.
- The bearings and seals were set.
- The hole between the fan housing and bearing was partially closed. The temperature in the bearing housing was 438 degrees F and dropped to 60 degrees F five minutes after the plate was welded.
- Alignment and tension jobs were performed on the belts.
- Auto-lubers were installed farther from the fan housing.
In this case, we locked the drive-end bearing, because this typically was where the highest radial load was located. While the situation improved, we still needed to perform a balancing job. The thermal profile of the bearing before closing the hole is shown below. You can even see the heat without the thermal camera.
The hole could only be seen when the cooling fan was removed. We did not have an opportunity to perform the fan cleaning and balancing job until April 29, 2018.
Actual Condition
After performing the balancing, the actual condition was good.
Conclusion
After performing root cause analysis and checking the evidence, we concluded that the origin of the fault was the combination of the heat over the bearing and the unbalance. Once a year when we stop the furnace, we must service both fans.
Thermal Oil Pump
This planetary gearbox was powered by an ABB motor. Three years ago during oil sampling data collection, one external contractor lost a sampling hose, which was trapped and pulled by the gears. Most of the hose parts were retired at that moment.
On May 17, we discovered a high oil temperature alarm, and our mechanics noticed the lubrication pump didn’t work. The decision was made to run the gearbox without lubrication, but after one 12-hour shift, the pump was changed. Oil samples and vibration data were collected to determine the damage. A borescope inspection and a filter change would be scheduled for the next down day.
Actual Condition
The iron content increased from 2-3 parts per million (ppm) to 10 ppm. This was due to incipient damage in the gears. The damage was confirmed with vibration measurements and the borescope inspection.
A deep borescope inspection will be performed during the next downtime. The equipment inspection program is closely monitoring the frequency.
Inlet of the pump
Overall vibration measurement
This article was previously published in the Reliable Plant 2019 Conference Proceedings.
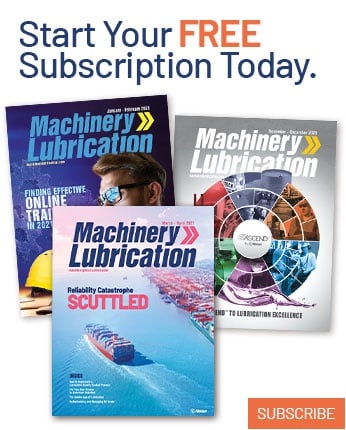