Home Market Foods is a premium food products provider based in Norwood, Massachusetts. The company recently identified an opportunity to significantly improve its maintenance storeroom management. Cost-saving activities had been focused on unit costs instead of value, while inefficient inventory practices were limiting the ability for maintenance technicians to find the right part when needed. Labor and material costs continued to rise. Several supply-chain management techniques were used to gain better control of the maintenance storeroom.
Taking Inventory
The maintenance, repair and operations (MRO) storeroom began as a small cage in the maintenance area called “the parts cage.” All parts were received into the system and booked as an expense. Physical inventory had never been done because there was not enough time, manpower or information. In 2011, the first physical inventory was conducted, which accounted for all spare parts that were owned.
The first step was creating an inventory parts master list in the computerized maintenance management system (CMMS). The master list was grouped together using commodity codes. Stock numbers were issued with unique internal numbers. The commodity codes were used to classify parts, such as “BRG” for bearings. There were also commodity codes for original equipment manufacturer (OEM) parts.
Data Cleansing
When developing an item master or implementing a new CMMS, a thorough data cleanse must be performed. Immediate cost savings can be achieved by creating commodity codes and stock numbers, as this helps to cleanse the storeroom of duplicate parts in multiple sections. For example, we found several of the same electrical push buttons within the different OEM parts. The electrical controls were standardized to one manufacturer, and a section designed for these items. This standardization cut costs by stocking less material and reducing downtime for mechanics who no longer had to fumble through all the equipment parts looking for a contact or button.
Standardizing
The next step was standardizing our equipment descriptions. All descriptions now follow the same sequence, such as “motor, 1 HP, 1,800 RPM, 56C, stainless.” This allows us to search all 56C motors to see if we have something usable in stock if for some reason we do not have the exact stainless-steel motor. This standardizing activity has been most useful with gear motors.
Constant Improvement
To be effective, the storeroom must be in a constant improvement cycle. For example, if the correct motor is not in stock but a replacement motor is found, the stock room must take charge in tracking this information and working with planning to determine whether it is a sufficient spare or if the proper part should be replaced once it has been received.
There must also be trust between the storeroom and the mechanics. Without trust, the mechanics will hoard materials or over-order, which will lead to inaccurate data. For instance, three filters are replaced each week on our breading equipment. The mechanic who performs the change usually grabs a case of 12 and puts them in the attic so he doesn’t have to go all the way to the storeroom the following week. The order point then tells purchasing to order another dozen filters because we have none, and the cycle continues.
Having a proper transaction procedure is another critical element to success. Inventory should be updated in real time for items being received into stock and issued out of stock. We implemented barcode scanning, which allows technicians to sign out materials directly to their work orders using a barcode. As we continuously improve, we will be working to always require a work order for materials to help track costs and work order history.
After a few years of accurate inventory counts, we have been able to validate our cycle-counting process and eliminate the need for a yearly count. A monthly cycle-counting schedule has been created not only to calculate what is used but also to ensure all items are counted at least once a year. Of course, some spares were purchased due to the risk of downtime. In these situations, the part only needs to be counted once a year, since there is not much usage.
What to Stock
When deciding what to stock, critical parts should be evaluated separately. First, determine criticality and then make your stocking decision. In the past, if a machine went down because we didn’t have a motor, we would buy two so we would have a spare the next time. This mentality resulted in a lot of non-moving spare parts.
Poorly managing your non-stock inventories can cause lost time and improper assembly. Vendor-managed inventory and point-of-use lockers are typical value-added services from suppliers. They can also help you build trust with your mechanics. Our quick-disconnect air fittings are a good example. These fittings cost just $1 but can put a roadblock on a job if they are not in stock. While the mechanics will always find a way to make it work, this increases wrench time and the chances of an air leak, as well as discourages the technicians that the storeroom will have what they need when they need it. We found the best solution was to use an inventory service. However, we take control of the program by scanning our own orders using a barcode and adjusting the minimum and maximum levels so the supplier does not overfill our orders.
Partner with Suppliers
Identify your primary suppliers and decide which ones could be partners. Many different suppliers can provide for our needs, but we have asked our suppliers to partner with us to help solve our problems. Scorecards can be used to decide which supplier is the best fit. Remember, the one with the lowest cost is not always the right solution. Quality, delivery and service should all be considered.
Inventory management was one of the first steps in Home Market Foods’ journey to reliability. These changes have improved our ability to provide job plans on PMs and make work orders more task-based. We have also been able to reduce the amount of inventory by planning when each part will be needed. This type of planning has increased our uptime and maintenance labor productivity.
This article was previously published in the Reliable Plant 2019 Conference Proceedings.
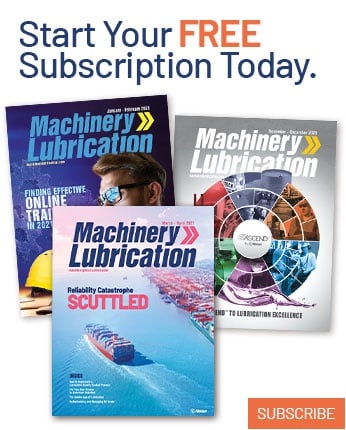