Introduction
Managing your spare parts inventory is a critical component of efficient and cost-effective operations for businesses across various industries. Whether it's manufacturing, automotive, or even the IT sector, having the right spare parts readily available and effectively managing inventory levels can significantly impact a company's bottom line.
These practices involve the strategic procurement, storage, and distribution of spare parts to ensure minimal downtime, optimal equipment performance, and cost savings. In this dynamic and competitive business landscape, mastering spare parts and inventory management is essential for staying ahead of the curve and delivering superior products and services to customers.
Having conducted more than 80+ courses, Ramsoft (UK) has been training and consulting with companies to improve their management of spare parts over the past 10 years. We have found the same issues in all industrial sectors; however, some sectors seem to be worse than others.
This article will present a six-step improvement process for an existing site, as shown in Fig. 1:
Fig. 1 - 6-Step inventory improvement process
Although, we have identified a total of 38 tactics to improve the management of spares, the greatest opportunities for an existing site arise from the following five tactics:
- Step 3 by identifying and removing duplicates.
- Step 4 by seeking rationalization opportunities i.e., reducing the varieties of spares stocked and converting OEM parts to OPM parts where there is little risk.
- Step 5 by conducting a structured review of current stock levels against calculated optimized inventory levels.
- Step 6 by reducing the number of stocking locations.
The key to the above tactics is to have an inventory catalogue that is accurate and to a high standard.
Savings can be significant, evident in the following example:
- A mining company with 100s of drive and timing belts (mostly classified by OEM P/Ns) had no detailed, belt-specific attributes, so there was no way of identifying duplicates.
- Up to 60% reduction in the number of line items for a specific noun group of parts by eliminating duplicates, standardizing on specification, and rationalizing to comply with the standards.
- A review of the company's top 10 line items resulted in the potential reduction of $500,000 in max stock level value.
Step 1: Auditing Inventory Management
Step 1 starts with an assessment of current practices. Three main areas may be included in the audit:
- Management Practices: A formal assessment of all the activities required to manage spares including the systems in place and the use of information. This will result in an assessment or benchmarking score.
- Inventory System Data: Includes a review of cataloguing data, analysis of duplicates, a review of the bill of materials, issues, and demand analysis, etc.
- Written Procedures: i.e., The scope of the procedures in place, their technical content - are they used as they should be?
In this article, we will focus mainly on cataloguing.
Good cataloguing should start in the project phase and continue through the item’s life cycle. Unfortunately, most companies do a poor job of creating their inventory catalogue. Poor cataloguing results in:
- Inability to find the right spare in a timely manner
- Higher number of duplicates
- Excess stock-holding costs
- Additional loss of production while trying to find the right spare
- Emergency purchases when the right spare cannot be found
The main issues are:
- No standards for describing a part
- Too many Mfr’s P/N are vendor’s P/N that typically cannot be validated on the web
- Many typos, e.g., 'I' or 'O', used instead of a '1' or '0' or a '5' instead of an 'S'
- Different formats used to populate the P/N
- No rules for dealing with manufactures who use a dual P/N system
Figure 2 shows one bearing example stocked in three different bins. Oonly by removing the non-alpha numeric characters from the Mfr’s P/N do the duplicates become obvious:
Fig. 2 - Bearing stocked in triplicate
Step 2: Develop or Update Process and Procedures
Following the audit of the procedures in step 1, a plan should be put in place to create or update existing procedure. We have defined a total of x procedures are required to fully manage spare parts. These can be grouped in the same section as the ISO 55000. We find most companies outside of the oil and gas section have poor procedure for requesting and purchasing initial spares and how to achieve good cataloguing.
Step 3: Data Validation and Cleaning
There are several options to cleanse cataloguing data. But the main decisions to make are:
- Whether to outsource to a specialist company or conduct in-house resource
- If in-house, then need to ensure your people are trained in good cataloguing practices and whether to use Excel or MS Access. MS Access is the tool of choice and includes master templates to ensure a high level of governance.
- If outsourcing, again ensure in-house people are trained, so they can review the quality of the delivered data. We have experienced poor quality cleansing carried out by many so called consultants.
A database for data validation and cleansing links multiple tables to ensure governance by creating many Noun/Qualifier1/Qualifier2 templates, as well as the facility to build a master list of P/Ns. For a company with different warehouses, such a tool simplifies the cleansing for the second or third warehouse.
Step 4: Standardization and Rationalization
After Step 3, the cataloguing should be of a consistent format, and you can start to seek rationalization opportunities. Standardization requires setting out the company’s organizational strategies and can be categorized by equipment, manufacturer, or by the material of construction, and so on.
Without proper standardization, inventory will be higher, and hence, so will stock-holding value. A recent data-cleansing exercise revealed the company had bought equipment from both USA and Europe. This meant they had different drive-chain components to different standards, thus, resulting in a need to hold stock for both the DIN and ANSI standard.
Here is a small sample of caterpillar belts from a total of 540 belts (involving many OEMs) stocked by a large mining company. There is no information on the type, size, or cross section. Without more detail it is impossible to properly identify the duplicate belts. We see same issue with filters and other spare types.
Fig. 3 - Selection of caterpillar belts with no attributes
Step 5: Stock Optimization
To carry out this step, the stores team need to understand the different replenishment strategies. The two main ones are ROP and Min-ROP-Max. Which strategy to use is dependent on the EOQ (Economic Order Quantity). When EOQ is lower than the demand rate in the lead time, then Min-ROP-Max should be used. EOQ is also influenced by the average number of line items purchased on the same PO.
Most texts books define the basic formula but do not cover which strategy to use, neither do they define the process to optimize existing stock holding when the inventory may have 20,000 line items or more.
Key to the optimization process is to assign a criticality ranking to each spare part, which allows a %-service level to be defined to each spare, i.e., 99%, 98%, 95%, 90%, 85%. The service level influences the amount of safety stock to add.
For ROP-controlled inventory we aim to lower the average stock level value and for Min-ROP-Max and the Max Stock level Value.
It is important that sound formulas are used rather than rules of thumb. A review of a recent asset-management book stated the ROP should be 2-times the Usage in the Lead Time. This rule of thumb does not consider risk.
Figure 4 shows our evaluation of this rule. It is assumed the desired service level is 98% and the annual demand varies from 5 to 100. We can see that this formula gives a low service level for low annual demands (resulting in potential stock outs) and a very high service level for high annual demands (excessive stock-holding value).
Fig. 4 - Evaluation of a rule of thumb
Initial indicators of excess stock holding are:
- Excess stock (difference between QOH Max and CMMS Max)
- High number of years of stock or TOR calculated at line item level
- High K Value (K is a measure of safety stock; any value above 2.33 is considered excess)
Figure 5 shows an analysis of very high K values, indicating excess stock:
Fig. 5 - Spares with high K values
Figure 6 shows one example from a large chemical plant and the actual max stock level, the calculated (optimized) and the proposed max level. This resulted in a reduction in max stock level value of $88,179, and this was considered conservative.
Fig. 6 - Extract from an optimization study
Note, although calculations for optimization can be obtained in bulk, the review to make stock changes is carried out item by item.
Step 6: Monitor Performance and Taking Action
Step 6 includes several tactics such as:
- Monitoring ADR against estimated usage and stock balance
- RCFA for A-class items
- Repair versus replace decisions.
- Evaluate rotable spares.
- Obsolete management
- Training in all aspects of managing inventory.
Summary
We have shown a proven process to reduce inventory, which can result in significant savings. Over the past 20 years Ramsoft (UK) have trained 1000’s of delegates in maintenance, reliability, and spares. However, we have primarily focused only on the effective management of spare parts.
Most of the professionals we have traied all have similar issues with inventory management, which is why in our main training course, titled "Effective Spare Parts Management & Inventory Reduction", we add the disclaimer that "Savings are guaranteed". This the only course for which we have ever made this claim.
Give this step-by-step plan a try at your facility and let us know your results.
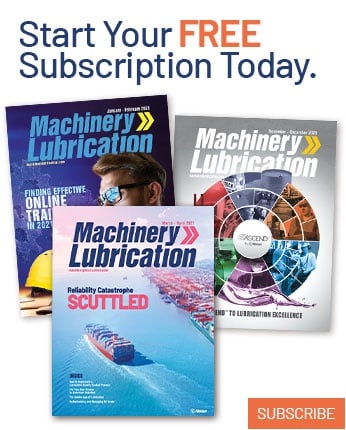