Despite their widespread use, electric motors are largely misunderstood in terms of how they function and how they can be tested. Even with the ever-broadening understanding of reliability-centered maintenance (RCM) practices and reliability initiatives, the belief still exists that if you put power to an electric motor and it starts turning, it must be defect-free. Nothing could be further from the truth.
This article will discuss the types of failure modes that can be discovered with electric motor testing as well as the basic steps for an effective acceptance testing program. Concrete examples of the cost savings and immediate impact on equipment availability and effectiveness as a result of a comprehensive motor acceptance program will also be given.
Building a Motor Testing Program
When building an electric motor testing program from scratch, the old adage about how one would eat an elephant comes to mind. The answer: one bite at a time. Building a motor testing program can be an enormous undertaking. There’s the cost of equipment, which is not insignificant, plus the allocation of resources to perform the work.
Considering that electric motors can account for 75 percent or more of the overall electrical energy consumption of an industrial facility, the sheer number of assets that would require testing can seem overwhelming. A good first step can also be your last line of defense against acquiring motors with defects — acceptance testing.
To understand how acceptance testing fits into an overall reliability strategy, consider the basic goals of a reliability program. Chief among them is reduction of maintenance costs. Electric motors can be a costly asset, especially for custom applications.
Increasing the mean time between failures (MTBF) can have a direct impact on maintenance costs. Reducing the amount of failures can also drive down the overall maintenance dollars spent. While the application of RCM technologies can have an indirect cost savings impact, that savings can be realized almost immediately with motor acceptance testing.
Precision maintenance practices are only as good as the assets being installed. An electric motor that arrives on your loading dock from a vendor or repair facility can have failure modes present in it that acceptance testing could potentially reveal. Once the motor has been received, it belongs to the facility.
Any defects discovered after receipt also belong to the facility. A robust electric motor acceptance test can help ensure that received motors are defect-free, so failure modes aren’t being introduced into the process or system.
When deciding on a motor test instrument, cost and applicability are obvious considerations. Request demonstrations of the various types of testers. Research other facilities within your organization or even from other organizations within your industry to determine what will work best for the program you are trying to build.
Training personnel to perform electric motor testing will also be essential. While electric motors are a common asset, many otherwise talented maintenance and reliability professionals are not savvy in how electric motor testing works, particularly how to analyze the captured data.
Specific training is required if the personnel assigned to the task of motor testing have no previous experience. Numerous industry standards exist for motor testing. Invest in these standards and apply them as the basis of your motor testing program.
5 Steps to Beginning Electric Motor Testing
There are five general steps to beginning acceptance testing: selecting a vendor and repair facility, developing a tracking strategy, conducting a receipt inspection, performing acceptance tests, and implementing a proper storage system.
Vendor and Repair Facility Selection
When selecting a vendor and repair facility, keep in mind that you want someone reputable. It’s also ideal to choose vendors who utilize equipment similar to that used at the facility to test motors prior to shipment. Selecting the right vendor ultimately will lead to fewer rejected motors. It’s common practice in the motor industry to ship the best motors to facilities where acceptance testing is known to occur.
Tracking
To track motors once they are accepted, develop an administrative process that tracks motors from the time they hit your loading dock until they are scrapped at the end of their useful service life. This includes when they are sent for repair. Don’t rely on the motor’s nameplate to track it. This is often swapped in repair shops. The best tool is an embossed metal tag with a specific internal code or number that is permanently attached to the motor.
Receipt Inspection
A receipt inspection involves a detailed visual check of the motor and all its components. Make sure the shaft was supported during shipping, the motor casing is clean and shows no signs of impact, and that the grease fittings are installed and capped. Also, check the casting for cracking. Confirm that the feet are flat and machined, and that the nameplate is installed and readable. Open the connection box and give the crimped connectors a good tug. Verify that the fan shroud is properly installed and that the cooling fins aren’t cracked or otherwise damaged.
Acceptance Tests
After the visual receipt inspection, several electrical tests should be performed. A “megger” test can be used to ensure no path is present from insulation to ground. Surge testing, phase-to-phase resistance and inductance, and a rotor influence check (RIC) are also advisable.
These tests can reveal turn-to-turn shorts, high-resistance connections and insulation weakness in the windings. Many of the failure modes detected through acceptance tests are not the kind that would necessarily keep a motor from starting and running but could lead to premature functional failure.
Storage
Ideally, your motor storage area should be climate-controlled. Temperature swings can result in condensation forming inside the motor. You also want the motor storage area to be free from inherent vibration. Exposure to vibration during storage can lead to false brinelling in the bearings, which can lead to premature bearing failure.
Store motors in such a way that they are easily accessible, particularly the motor junction box. Motors in storage should be tested just like in-service motors on an inspection route. Access to the junction box is required for this. Also, depending on the size of the motor, rotating the shafts of stored motors every 30-90 days is imperative. This will help guard against false brinelling and rotor sag.
Finally, it’s a not a bad idea to use cost-savings data to help promote your program. As MTBF increases, there should a definable cost savings associated with it. By tracking failure modes and the technologies used to detect them, you can point to specific reductions in failure modes to which the increase in MTBF can be attributed.
Cost-savings data and promotion of your motor testing program can mean the difference between continuance and cessation. Shamelessly promote the successes of your motor testing program to ensure it enjoys longevity.
This article was previously published in the Reliable Plant 2019 Conference Proceedings.
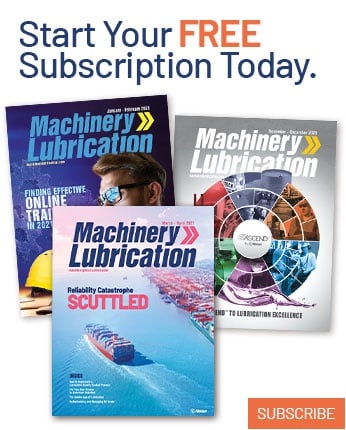