There are several consistencies in the types of people who go into industrial maintenance. They tend to be type “A” personalities — confident, somewhat cocky and a little rebellious. Their value is in the knowledge and ability they bring with them, and they don’t see this as something that can easily be replaced. They are independent and take a lot of pride in their knack for getting the job done. This helps to explain some of their resistance to maintenance procedures.
Most industrial maintenance departments will tell you they already have procedures, whether they are stand-alone overhaul documents or embedded in the instructions of a preventive maintenance (PM) plan. In most cases, these procedures are not good.
They typically are general documents that use broad terms such as “inspect” or “overhaul,” which don’t help anyone who doesn’t already understand the scope of work. Many think this type of instruction in a procedure is adequate.
These are often the people who are already familiar with the equipment. To them, the use of a procedure is at best an irksome bit of paperwork. At worst, it is seen as a time-sink that becomes a hindrance to getting more things accomplished.
Many maintenance professionals also have a little voice in the back of their minds that says, “If there is a detailed procedure, they’ll be able to get rid of me and bring in a lower paid person to do my job.” This last statement is an important consideration because it is a real fear for some.
In addition to maintenance personnel not having a great desire for detailed and thorough procedures, there is the fact that creating a procedure takes time and effort. The crafting of clear instructions is not as straightforward as the uninitiated may think.
The technical research that must go into a procedure can be daunting. The difference between “inspect the equipment” and a procedure that walks you correctly through every step with the necessary details to execute it correctly is almost exponential in scope. A one-sentence instruction can be turned into a 10- or 20-page document that can take a week or more to create.
So why bother? Why spend time and money on something that isn’t wanted and which many in-house people will tell you isn’t even needed? In the majority of maintenance departments, the discussion stops right there. However, there are very strong and pressing reasons for developing detailed maintenance procedures.
Benefits of Procedures
Procedures bring completeness or thoroughness to the work. Once, as a way of capitalizing on the working knowledge of the maintenance technicians, I gathered the top four mechanics in the department to talk about one piece of equipment. I asked one of the mechanics to walk through what he did every time he performed a PM on the equipment. He started by saying, “The first thing I do is grease the six lube points.”
As soon as he said this, a different mechanic spoke up and said there were seven lube points, with the seventh being relatively hidden. The other three mechanics had no idea there was a seventh lube point. Without going into all the specific details, I can recall how every mechanic knew of at least one task that had to be performed on the equipment that the other three didn’t realize.
None of these tasks were trivial. All four of these individuals had worked in the department for at least seven years and were on the day shift in a department of only 12 people, yet they still weren’t able to transfer their specific equipment knowledge to each other. Now multiply this by the amount of equipment and the number of people in your plant to get an idea of the variability of the work being done.
Procedures bring consistency to the process. They not only ensure that all the tasks are performed but that they are performed in the same way. For example, one person may grease a bearing until it spills out the sides.
Another may think one pump is enough. If the procedure defines the amount of lubricant to be added, you’ve introduced consistency to the process. The same applies to specifying bolt torque, alignment tolerances, etc.
Procedures also offer a detailed record of the equipment’s history. If you have a procedure and have developed a culture of adherence, you can be confident in knowing exactly what work has been done on the equipment and at what frequency.
This is a huge help when trying to diagnose the root cause of a failure or when adjusting your PM task frequencies. You can even use procedures as a repository for the information you want to keep, such as alignment readings and wear measurements.
Procedures give you the ability to capture knowledge. The more you work on the equipment, the more you learn about it. Items such as lubrication amounts and frequencies, alignments, torque requirements, and preventive part replacements are often determined or altered based on equipment experience.
There’s also the ability to document the knowledge gained from previous failures to provide specific details that may not be obvious to a competent technician. Procedures offer a place to store this information in a way that is easy to retrieve and use.
A procedure can also allow you to institutionalize upgrades or changes in work practices. It’s always challenging to modify a person’s habits even if he or she is not opposed to the change.
A procedure that specifies the use of an anti-seize compound on bolts or the precise alignment of motors and gearboxes will remind personnel that standards have changed while reinforcing the proper actions until they become the new habits.
Good procedures make it easier to schedule technicians. It’s common for maintenance departments to schedule work around certain technicians who know how to maintain a particular piece of equipment. It’s not unusual for repairs to be moved up or delayed or even to stop a partially completed job to get the right person on it.
A procedure eases this restriction by enabling any competent technician to perform the work correctly. It also frees up the more talented people from repeatedly doing the same technical work, allowing them to grow in other ways. It’s a win-win for the staff and the department.
Procedures also simplify job planning by identifying the necessary parts, tools and supplies. You can add specific site, process or coordination requirements into the procedure. All of this reduces the reliance on an individual’s memory and helps to increase the efficiency of the work execution.
Finally, good procedures can help disseminate knowledge throughout the department. For example, say you decide to start using an adhesive on all your set screws. You gather the maintenance group together at the morning meeting and inform everyone about the new practice.
Unfortunately, some people were off that day, or you forgot to tell the backshift crew. The backshift supervisor may not have remembered to pass along the new instructions or garbled the message. After the weekend, perhaps half of the people you told forgot about the change.
Then, as new people enter the department, you don’t brief them specifically on using the adhesive on all the set screws because there are hundreds of different standards in the department and nobody ever made a list of them. By placing these instructions in procedures, you reinforce the changes and remind everyone of the department’s standards.
We’re living in a different world than we were 20 to 30 years ago. I grew up in the Pittsburgh area. If I would have thrown a rock into a crowd of people 30 years ago, the odds were high that I would have hit someone who understood mechanics and equipment. That’s not true today. Now, the machinery around our houses is mostly not meant to be repaired. Instead, it’s designed to be replaced or have the parts changed.
Cars are another great example of this. Also, video games seem to have a much greater appeal than trying to fix your toaster. Because of this, people coming into the maintenance field are not bringing the average level of practical experience they once did.
You can’t expect them to have good sense when it comes to working on equipment. One of the ways to overcome this deficit is with effective procedures that not only address the complicated tasks but also give detailed instructions for how to perform the pedestrian tasks.
Equipment is becoming more complicated, and there is less room for error by the maintenance group. Even the tools are more complex. We’ve gone from dial-indicator alignments to laser alignments and from using your hand to feel if something is vibrating too much or is running hot to using accelerometers, infrared guns and cameras. Maintenance must keep up with the times. The development of good procedures is a critical tooth on this cog.
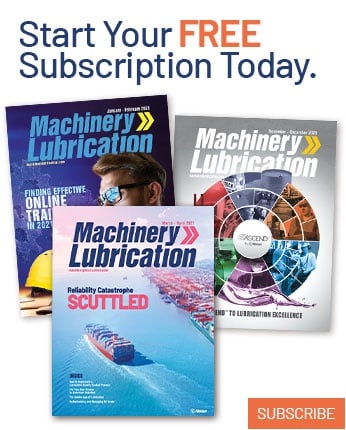