Equipment isn't meant to last forever. Like everything else, it has an expiration date, and it can begin to exhibit signs of wear and tear that require attention. Beyond simply becoming less reliable because of system changes over the years, older equipment may not be able to safely protect personnel and other equipment as it was designed. Additionally, it cannot support the cloud or Internet of Things (IoT) connectivity required of modern facility infrastructure. However, restricted budgets and the cost of downtime from lengthy replacement processes often mean it can be difficult to secure management buy-in on necessary upgrades, which are frequently deferred until the last minute – but they don't need to be. This article will examine the benefits that can be realized through timely modernization.
Hesitance to Modernize
When it is time to upgrade and modernize electrical equipment, plant workers can face resistance from their managers. While electrical systems serve as the backbone of a well-functioning facility, they are normally last on the to-do list for management, who may be more focused on security, energy efficiency, cleanliness and other factors. This can be due to misconceptions concerning the costs, the length of downtime, available space for new equipment and more. However, there are many benefits of equipment modernization that managers would do well not to ignore. The process is also simpler and less costly than full replacement.
Benefitting from Modernization
When facility infrastructure is modernized and upgraded, plant managers can expect to see an increase in reliability and safety as well as enhanced integration with current cloud and IoT technologies. To help make the case for modernization, engineers would do well to discuss the following five benefits with management:
1. Plant Reliability
As many facilities plan to maintain operation for 40 to 60 years despite the 30-year lifespan of most electrical equipment, it is becoming increasingly important to have reliable systems in place. Up-to-date equipment improves overall reliability by eliminating the faults that may occur with older equipment. With just a few hours of downtime potentially costing thousands or millions of dollars, there is no wiggle room for unplanned power outages.
2. System Safety
Modern equipment has additional features to ensure workers are operating in safer conditions. These include space-age materials, compact formats and digital trip units. They also offer high fault current withstand capability without the use of limiting fuses. Since power circuit breakers provide such a vital function in protecting the electrical system and reducing the risk to workers from arcing faults, these design improvements are a quantum leap forward in equipment and personnel protection. In addition, they have lower maintenance requirements than older circuit breaker designs. Because of this, modernized equipment makes it much easier for plants to stay in compliance with National Electrical Code (NEC), National Fire Protection Agency (NFPA) and Occupational Safety and Health Administration (OSHA) requirements.
3. Cost Savings
Unlike full replacement, modernizing equipment maintains the existing switchgear's footprint, saving plants potentially millions of dollars in space reconfiguration. Retrofits can be scheduled and executed over time, improving cash flow. Upgrading also benefits tight operating budgets by extending the life of existing equipment.
4. Availability of Parts
Most manufacturers will halt parts production for equipment models that are decades old. As a result, as equipment ages and requires maintenance, it can become increasingly difficult to source and purchase spare parts. Modern equipment has greater spare parts availability, making repairs and upgrades more affordable and feasible as well as less time-intensive.
5. Digital Capabilities
As technology continues to develop and improve, plants can benefit from integrating modernized equipment that facilitates cloud and IoT connectivity. Many digital components of electrical equipment tie directly into enhancing facility management and enable plant managers to make smarter decisions. For instance, connecting an asset performance monitoring system to electrical distribution equipment allows the health of the equipment to be checked remotely. This provides actionable insights for managing and maintaining critical systems to avoid unplanned downtime.
Implementing the Solutions
Plant managers can often be misled to believe that retrofitting will result in a significant amount of downtime caused by the need to conduct a full rip-and-replace. However, depending on the plant's needs, there are a number of ways equipment can be upgraded without bringing processes to a screeching halt. Two common processes are direct replacement and retrofilling.
Direct Replacement
A new circuit breaker can be designed to fit into the existing cubicle with little to no modification to the switchgear cell. Similarly, a low-voltage direct replacement breaker may use a standard circuit breaker that is interchangeable with new and old switchgear from various manufacturers. This is accomplished via the use of an adapter cradle to fit the new circuit breaker into the existing switchgear. A medium-voltage replacement circuit breaker can also be engineered to fit directly into the existing equipment manufacturer's switchgear. These direct replacement solutions can reduce downtime since there is minimal (if any) outage on the equipment bus.
Retrofilling
The existing switchgear cell and bus can be modified to accept the new circuit breaker. This process usually requires a longer bus outage, during which time the internal circuit breaker cell is modified to accept the new circuit breaker. A retrofill solution is often used in lieu of the direct replacement option for larger devices, such as main breakers and tie breakers. Retrofilling medium-voltage breakers will also allow for conversion of vertical racking to horizontal drawout switchgear.
Conclusion
Modernization should be a top priority for plant managers, as it can increase reliability and mitigate safety concerns that older equipment presents. Upgrading equipment also enables businesses to adopt more modern technologies that support cloud and IoT capabilities, which are becoming more commonplace. Therefore, it is critical to understand the financial and functional repercussions your facility may face if you prolong modernization. Having conversations about the current status of your plant's equipment and discussing ways to maximize reliability and safety should be a common occurrence among your staff and management.
About the Author
Doug Robling is the business development manager for Schneider Electric.
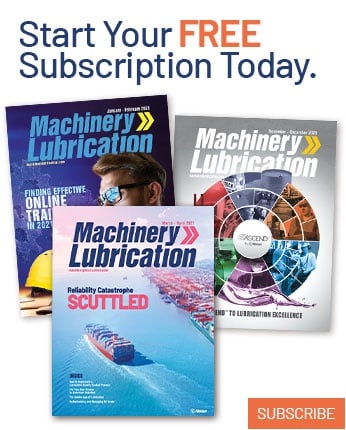