The first industrial electric motor was probably considered a breakthrough in its day, even as there was plenty of room for improvement. As technology has advanced, motor manufacturers have developed better motors that use less energy and lower costs. While it's only natural for manufacturers to employ the latest technology in creating electric motors, the scope for further advancements in production methods has been instrumental in improving the efficiency of these motors.
Consider the following statistics:
- The global electrical market was valued at more than $70 billion in 2015 and is expected to grow at a compound annual growth rate (CAGR) of 4.2 percent from 2017 to 2025.
- World electricity usage is estimated to reach 35 trillion kilowatt hours by 2035, and almost 28 percent will be used by electric motors.
- Ninety percent of installed motors run continuously at full speed and use mechanical systems to regulate output.
The future definitely looks promising!
Before getting into the efficiency of electric motors, it is important to understand more about the common motors used in industries.
A simple DC motor converts direct-current electrical energy into mechanical energy. It typically comes equipped with a high number of coils, which make it efficient. However, it can still result in a lot of wasted energy due to the friction between the commutator and brushes as well as the loss of torque at certain angles. Furthermore, if the motor gets stuck while trying to lift a heavy load, the rotor coils can easily overheat and melt. This is why a number of industrial and heavy home appliances use electric motors.
How Manufacturers Can Save Electricity with Electric Motors
The way an electric motor is designed and the way it is used are the two determinants that can help save electricity. Let's look at the design aspect first.
Using Copper Windings in Stator Coils
As far as the conductivity of the motor is concerned, it is always better to go for copper coils rather than outdated aluminum ones. This is because aluminum's conductivity is lower than copper's. To keep up with copper coils, aluminum magnet wires may need larger cross-sections so they can provide the same level of conductivity. Windings wound with an aluminum wire may have greater volume compared to a copper wire motor of the same size.
If you're still using aluminum windings, ensure that the ends of the aluminum magnet wire are properly connected. Aluminum oxidizes much faster than other metals, and if powdered aluminum is exposed to air, it will oxidize fully in just a few days and leave behind a fine white powder.
To make a proper connection that ensures good conductivity, the oxide layer of the aluminum magnet wire must be pierced to prevent the aluminum from coming in further contact with air.
Of course, achieving motor efficiency is more than just deciding between aluminum and copper windings. Several manufacturers have developed high-pressure-piercing crimp connectors to enable better efficiency. This has been done to help aluminum windings keep pace with their copper counterparts. While it is possible for motors with aluminum windings to match the power of copper ones, it takes time and money. Aluminum also requires more turns and a larger diameter wire, which may not always be economical.
If the motor is required to work occasionally or for a short duration, and when efficiency and volume are not of the essence, using aluminum magnet wires can make sense. Otherwise, copper windings should always be preferred.
Using Copper Bars in the Rotor
When it comes to rotors, copper offers the advantage of efficiency as well. Copper rotors are preferred for energy-conscious industries in developed countries and in developing nations where electricity is often in short supply and costly. Copper rotors are a better bet compared to aluminum ones in terms of motor quality, reliability, cost, efficiency and lifespan.
Machining Moving Parts with Precision
Machining entails removing material from a compartmental unit to a highly tolerable substance. Precision machinery is necessary to achieve the highest tolerance at the smallest measurable degree. Whether it is metal cutting or coal mining, precision machinery can provide the accuracy needed to produce materials in the desired quantities. The moving machine parts will demand timely maintenance for maximum output and efficiency. Maintenance should only be performed by experts, and an inspection of all parts should be required.
Using High-quality Steel for Rotors and Stators
High-tech electrical steel is essential for manufacturing economical stators and rotors used in an array of electric-motor applications. This type of steel ensures high magnetic permeability and low power losses for top-notch performance. However, power losses in electrical steel may still occur. Eddy currents, also called Foucault currents, come into play when a magnetic field is alternated. Rolling steel to a thinner gauge controls these eddy currents and reduces current losses. This is especially true of application frequencies beyond the standard 50 or 60 hertz.
Keeping the Rotor and Stator as Close as Possible
Through precision manufacturing, manufacturers can keep the rotor and stator as close as possible without touching. When the rotational speed reaches several thousands of revolutions per minute, the electrical steel in the rotor may experience tremendous stress. High stress is especially felt in areas near the magnet slots, where narrow equipment holds the magnets in place.
With induction motors, the transfer of energy takes place through the air gap between the stator and the motor. The air gap is necessary to minimize resistance. A small air gap will lead to less energy loss and higher efficiency. The total flux linkage between the stator and rotor widens as the air gap decreases. Higher flux linkage results in decreased energy losses and heightened efficiency. A smaller gap also helps to avoid noise.
More Coils Make Motors More Efficient
The wires in the phase coils of small power motors are thinner. However, the number of coil turns should be high to increase the magnetomotive force or current density. The resistance of the phase windings and the power loss density are also higher than in high-power motors. Therefore, low-power motors with high speeds will require more magnetomotive force. This means more coils will be needed along with a higher number of turns with a thin wire that produces higher current density.
Using Variable-speed Drives
Variable-speed drives (VSDs) or adjustable-speed drives are heavy industrial electric motors. Their speed can be adjusted with an external controller. These drives are used in process control, as they help to conserve energy in plants that utilize numerous electric motors.
VSDs typically are employed as energy savers in pump and fan appliances, since they better process operations, especially where flow control is necessary. They also provide soft-start capabilities, which bring down electrical stresses and line voltage sags that are generally found in voltage motor start-ups, particularly when driving high-inertia loads.
How Electric Motor Users Can Ensure Efficiency
As mentioned previously, how electric motors are used by manufacturers, industries and homeowners will determine their efficiency. Below are some specific steps users can take to ensure motor efficiency and longevity:
Using Smart Motors with Appropriate Motor Starter/Controller
While smart motors are widely used and available, it is crucial to choose the best fit to minimize downtime, improve efficiencies and lower costs. Industrial engineers know the burden that electrical consumption by motors can put on their operating budgets. To mitigate this, they often utilize motor control technologies that use only the necessary amount of energy to start motors, reveal diagnostic data and reduce downtime. As motor starters gain acceptance, motor starter technology is also increasing in prominence.
Following are a few important questions to consider before deciding on potential applications for electric motors:
Will the application require speed control even when the motor is at a certain speed?
Speed control requirements should be decided upon as early as possible. Some soft starters have limited slow-speed control between starting and stopping. The important thing to remember is that the operating speed of the motor cannot be changed because the soft starter regulates only the voltage of the motor and not the frequency.
Will the application need specific start and stop times?
Usually, start and stop times with soft starters are dependent on the load. Internal algorithms adjust the voltage based on pre-programmed times to increase the current and torque to start the motor and/or decrease them to stop it. If the load is light, the motor can take less time to start than the programmed value. New-age soft starters have employed advanced algorithms, leading to more accurate and less load-dependent start and stop times.
Will the application need full torque at no speed?
VFDs may work best with applications that require full torque at zero speed. They can produce rated motor torque from zero to rated speed and even provide full torque at no speed. Soft starters, on the other hand, typically operate between the frequency of 50 to 60 hertz, and full torque can only be achieved at full voltage. Initial torque (available at zero speed) normally ranges from zero to 75 percent and can be programmed.
Will the application need constant torque?
Soft starters alter the voltage to control current and torque. At the time of starting, the current varies according to the voltage, while the motor torque varies as the square of the applied voltage. The torque may not remain constant at different applied voltages, a condition which may become more complex with varying loads.
Certain soft starters work on torque control algorithms, but this does not necessarily relate to constant torque. During acceleration, however, VFDs use different frequencies on the motor while changing the voltage. The VFD control mode is referred to in terms of constant volts per hertz and produces a constant torque.
What are the cost, size and thermal concerns?
At an amperage of less than 40 amps, soft starters can offer a minor cost benefit when compared to VFDs. As the amperage and power increase, the cost of VFDs increases faster than that of soft starters and can reach extreme levels at high amperages.
When it comes to size, soft starters have an advantage over VFDs at all amperages, thanks to their construction. As the current and power increase, the difference can become larger. When soft starters are teamed with an internal or external electromechanical bypass, they are even more effective and can produce less heat. This is because soft starters have fewer active components in the circuit during start, run and stop modes.
What are the installation and harmonics considerations?
Installation concerns can be categorized into cost, size, temperature and power quality. Soft-starter installations involve smaller sizes and lower costs, which is why they are not much of a concern.
In addition, soft-starter harmonics are less than those of VFDs. Long cable runs for VFDs need more attention than those for soft starters. Furthermore, special wire types may not be needed for soft starters. Electromagnetic compatibility may also not be considered.
Discontinue Using Motors When Not Needed
As simple as it sounds, the most effective way to save energy is to turn off the motor when it is not in use. More often than not, users hesitate to switch off a motor because they believe that starting it up repeatedly will lead to major wear and tear. One way to mitigate this is by using soft starters, which can reduce wear and tear. A properly installed and specified soft starter can also decrease the pressure on mechanical and electrical systems.
Reducing Wear and Tear
Reducing motor wear and tear is among the primary concerns of users. A great deal of wear and tear takes place when an electric motor is started, as the high initial currents and forces pressurize the mechanical and electrical systems. Although this can be detrimental, the damaging effects can be controlled with the help of soft starters. You may also employ VSDs, but these may be costly and less efficient.
Using High-efficiency Motors
Motor efficiency can be derived from two factors: the size of the motor and its efficiency quality. For smaller motors in particular, size is an important factor that affects efficiency. For larger motors, it is the efficiency classes that matter more.
Energy-efficient motors use less electricity, do not heat up as easily and last longer. These types of motors are characterized by a better design, which results in less heat loss and lower noise. The use of high-quality materials, tighter tolerances and improved manufacturing techniques also help to reduce losses and enhance efficiency.
To assess the benefits of high-efficiency motors, you must first define "efficiency" for an electric motor. This can be determined by the ratio of mechanical power delivered by the motor (output) to the electrical power supplied to the motor (input). Therefore, efficiency = (mechanical power output/electrical power input) x 100 percent.
Thus, if a motor is 80 percent efficient, it can convert 80 percent of the electrical energy into mechanical energy. The remaining 20 percent of the electrical energy is lost in the form of heat.
Buying the Right Motor Size
Motors tend to be most efficient between 60 and 100 percent of their full-rated load, and most inefficient below 50 percent loading. This means that merely buying the correct motor size can increase efficiency to a great extent.
Generally, oversized motors operate below 50 percent of their rated load, which not only makes them inefficient but also more expensive than motors of the right size. Moreover, they may also reduce the power supply to the machine, which increases the load on the electrical system.
Final Thoughts
With "energy efficiency" becoming a modern catchphrase, it is important that this concept be integrated into daily household and industrial applications. Energy-efficient motors can offer many benefits. With proper installation, they can run cooler, deliver higher service standards, last longer, provide better insulation, and emit less noise and vibration. With so many advantages, motor manufacturers would be wise to ensure that they are producing and employing the most energy-efficient motors possible.
This article previously appeared on www.powerjackmotion.com.
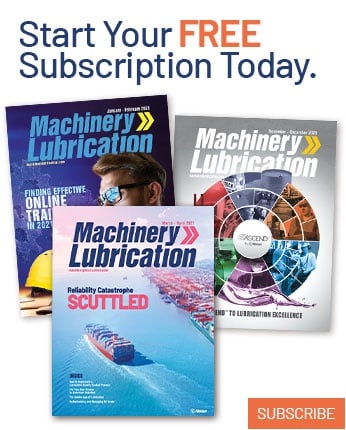