A long-held misconception is that operations employees are not responsible for reliability at plant sites. Instead, they assume reliability is handled by a completely separate department. This type of "silo" mentality, while prevalent at plants worldwide, does not result in a reliable, world-class operation. In fact, operations must take an active — not passive — role in plant reliability. Progressive companies recognize this and treat maintenance and reliability as processes, not departments. Unfortunately, the vast majority of companies have not adopted this progressive view.
In order to have a reliable, efficient operation, the various departments within operations must function like part of a process. Production must collaborate with and feel ownership of the maintenance, reliability and technical departments. The role of the internal customer remains important, but it is only one role. In companies that have the best reliability processes, production plays the role of not only the internal client but also of owner, director and partner, as seen in the diagram below.
Equipment Ownership
When there is a heightened awareness of the role of equipment ownership, the best practices in reliability are more likely visible. As Charles Bailey, retired vice president of operations at Eastman Chemicals once said, "Reliability cannot be driven by the maintenance organization. It must be driven from the operating units and led from the top."
Reliability and maintenance should be seen as processes, not departments. Operations has an important role to play both as owner of the equipment and as the driver of reliability. This does not mean that all reliability line organizations have to report directly to operations, but they should give an account of the status and reliability of the equipment to the equipment owners (operations) to drive better outcomes.
To achieve operations-driven reliability, operations/production should be in the driver's seat, since they own the equipment. They have the point of view of criticality and risk. They own the losses and should feel empowered to intervene directly. They also are trained to quick-fix. They feel ownership for the cost or the investment required to give a better return. They explain what they need to their partners. They make equipment available for maintenance, and they work with planners and schedulers to define the correct scope. They also give approval and constructive feedback regularly to those who provide them with updates, thus improving the service-partnership relationship.
Two key roles in this model are the operations maintenance gatekeeper and the operations reliability champion.
The Gatekeeper
In organizations that practice operations-driven reliability, there is an ordered way of determining workflow driven by four basic rules:
1. Maintenance employees will not generate their own work.
2. The equipment owners must make decisions about what maintenance work is done.
3. The determination of the workflow is usually made by a key operations person called the "gatekeeper."
4. Only the unit manager can overrule the gatekeeper (similar to the sergeant major in the army who reports only to the top officer).
The key to success is having a process to filter projects and an "executable backlog" of work with a specific operations role designated to gatekeeping. Oftentimes, as a result of the gatekeeping process, operations will take control over the value process and the work being done by maintenance. This, in turn, allows maintenance to focus on high-quality job execution and reliability improvement.
On a daily basis, the gatekeeper interacts with the planner, scheduler, operations team and first-line manager. He or she decides if a job needs planning or if it can be "self-planned." He or she gives feedback on the quality of notifications and can say "no" to his or her peers in operations if their request for work does not fit with the joint goal – generating profit within acceptable risk levels.
Frequently, the best choice for gatekeeper is a person in operations who understands the "personality" of the equipment and is a former first-line manager, as these employees have an affinity for operations and an understanding of the maintenance process. The gatekeeper can't be afraid to say "no." The gatekeeper role is essential for order, structure, prioritization and cost control of executed work.
To visualize where the gatekeeper fits among the three major groupings or departments of an organization, see the diagram below.
Maintenance and reliability are more processes than they are departments. As such, the maintenance and reliability processes are driven by the people who have the knowledge, skills and attributes to drive improvement. Operations-driven reliability breaks down silos and focuses everyone on the joint goal together.
Operations Reliability Champion
The operations reliability champion (ORC) manages equipment reliability as well as other uptime losses, such as quality or process issues. The ORC asks the following three questions in relation to equipment reliability:
1. Are the reliability processes focused on the right things?
2. Who provides direction?
3. How do we monitor progress?
In progressive organizations, reliability professionals do not generate their own work, and everyone is focused on the joint goal of solving and preventing problems.
The ORC's role includes ensuring that the problem-solving process is healthy. This includes chairing meetings with reliability engineers and site management to review root cause failure analysis (RCFA) outcomes and tracking, as well as obtaining management assistance to remove barriers or approve funding.
The ORC must also make certain that the problem prevention processes are effective. For example, the ORC needs to confirm that there is an appropriate risk-based approach in place. It is not his or her role to run these processes but to ensure they are healthy and working on the right activities. Again, the ORC may chair meetings that drive the problem prevention process and organize the team to support the objective.
In addition, the ORC should own the losses. The ORC knows where all the uptime or availability losses are and that each one has a plan – playing to one of the two processes above.
Operations-driven reliability is essential for progressive plant operation. It applies to refineries, chemicals, metals, cement or any manufacturing or customer-focused process where there is a joint goal of increasing profit within tolerable and acceptable risk levels. It breaks down silos and ensures that maintenance and reliability are not just departments but integral processes. When operations-driven reliability works, it delivers results and is sustainable. The commitment and hard work required to achieve it are well worth the effort.
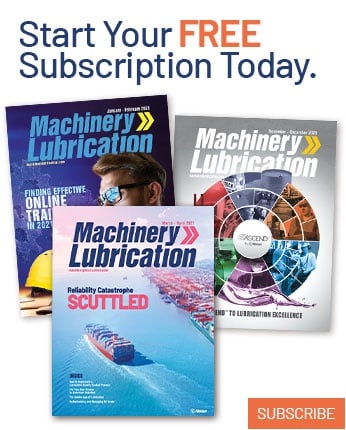