It's commonly understood that safety in the workplace is a collective responsibility within an organization. But this wasn't always the case. Decades ago, safety was the responsibility of the safety department. Then "thought leaders" — those informed and innovative thinkers who inspire and enlighten us — realized how critical safety is to the success and sustainability of a manufacturing facility. Culture change ensued.
In much the same way, reliability is now arcing its way along the path safety once took. The significance of reliability is making its way out of reliability departments and into corporate boardrooms. Many executives are beginning to realize that reliability is one of the most overlooked opportunities for growth.
No manufacturing facility is 100-percent reliable. There is always some level of waste due to inefficiencies and unreliability. So opportunities to improve exist, and these improvements can impact three key areas in which every organization wants to improve: customer loyalty, employee satisfaction and, of course, profitability. However, improvement is a journey that requires time, culture change and dedication to performance. There are no shortcuts, and the journey can never be completed without a commitment to continuous improvement.
Today, an increasing focus on reliability is putting many forward-thinking organizations on the path to high-level performance and even higher profitability. The path begins with executive support and is marked by a company-wide shift in focus toward reliability. This shift in focus is what sets top organizations apart from others when an improvement initiative is undertaken.
Proactive Culture Change is Linked to Performance
The more proactive an organization is about change management, the more adaptable it is to change. Successful behavioral shifts drive a company to become failure-free more quickly, significantly impacting the speed at which the reliability journey develops.
Achieving reliability becomes possible when management believes it is possible and encourages proactivity. Failing to address an abnormal indicator (however small) immediately makes it more likely that the sub-par will become accepted as normal — and that a slide to failure will begin. First-quartile (Q1) performers encourage proactive measures at the earliest sign of failure.
Every year, new technology and tools become exceptional reliability resources. However, as with safety, unless the organization is proactively striving toward becoming failure-free, improvements will be slow to materialize. Q1 performers actively address technology improvements, streamlined work processes, and improved diagnostics and communications. And they continuously devote effort toward becoming more proactive, seeking to understand any failure mechanisms that occur in the system so that they can pass this knowledge onto others for the benefit of the entire organization.
No Shortcuts to Top Performance
Organizations can get sidetracked on their reliability journey when there is pressure to put cost-cutting measures ahead of failure-free performance. When cost-cutting becomes the chief mechanism for achieving financial targets, reliability suffers — as does customer service. Organizations who succumb to the cost-cutting approach may realize short-term (but unsustainable) improvement.
Top performers understand that improved performance follows a path known as the inverted C (with the C turning counter-clockwise). This path may initially require more spending in order to improve reliability, but the resulting reliability culture will have a significant, positive impact on cost. Organizations that try to cut costs directly will have less success. Studies show that it is simply not possible to achieve sustainable improvement through cost-cutting mechanisms.
Achieving sustainable performance means initially investing more to create results. In time, however, the spending becomes more targeted and realizes higher returns. Spending is then driven down, while reliability is on the upswing, creating the aforementioned inverted C.
High Performance and Reduced Spending
Higher performance and reduced maintenance spending can be achieved once a certain level of reliability is attained. When companies can commit to the journey and apply long-term focus on continued process improvement, reliability is established. Then, continuing proactive performance improvement combined with targeted maintenance spending leads to sustainable reliability increases and spending decreases.
Ultimately, the highest performing organizations are able to consistently find the optimum amount of maintenance spending that delivers the highest operational availability.
Time for Improvement
Becoming reliable does not happen overnight. The journey requires significant planning, effort and buy-in from all staffing levels. Understandably, the further an organization is from Q1 performance, the longer it will take to achieve top-tier performance.
Typically, most companies begin to make progress four years following the launch of a performance improvement initiative. Throughout the process, these organizations must stay focused, even amidst the temptation to cut costs in order to realize short-term financial gains. But staying on course is critical. Along the journey, companies must modify work practices and processes and, at times, increase spending in targeted areas to revitalize assets. These are not easy tasks. It takes time to realize sustainable gains, but in the end the journey to reliability pays off.
Continuous Improvement through External Benchmarking
Once organizations start seeing year-over-year performance improvements, they begin to realize that the next level of performance measurement will require an external lens. The only way to truly measure whether performance levels are competitive is with external benchmarking.
Organizations that focus on improving reliability eventually realize that they must measure themselves against the best in the industry to know if their approach toward improvement is keeping pace with the competition. Only through consistent, external benchmarking is an organization able to measure itself competitively.
When companies fail to set out on the journey of reliability and performance improvement, profitability isn't maximized. In addition, without external benchmarking, untapped potential is unknown and opportunity may be left on the table. Top performance can only be achieved by improvements in reliability as verified by external benchmarking.
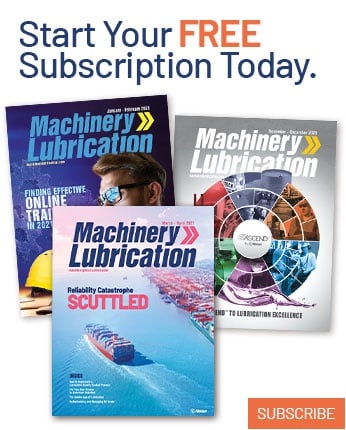