Managing a warehouse demands both a unique skillset and mindset, as it involves a team of people who must work together for a common purpose. This requires specially trained staff members who can fulfill complex inventory and shipping requirements as well as handle equipment and machinery both safely and efficiently.
Fundamentally, effective management will entail the proper balance of maintaining a productive, trusting relationship with staff members and asserting the right amount of authority. With that in mind, below are four crucial steps for managing a safe and productive warehouse.
Earn Their Trust
You can't effectively manage a warehouse staff without trust. Your employees must know that you are informed about their day-to-day routines and that you understand how their individual roles feed into the long-term warehouse goals. Your employees should feel comfortable enough to come to you with work-related issues, requests or concerns.
One way to accomplish this is to have an open-door policy for all work-related issues while also allowing workers to file anonymous company suggestions. That way, your warehouse staff can communicate with you with whatever level of anonymity is most comfortable for them. The goal, however, is to develop a relationship of trust where that option will not even be considered by your employees.
Trust always begins with transparency. Your workers should understand that all incoming orders, outgoing shipments, supply status reports and inventory counts are important to the overall success of the company and workforce, and therefore must be closely monitored. Accountability should be a welcomed part of the company's culture because it means "we really care." No need should arise to monitor staff activities secretly.
A united mindset toward recording, documenting and communicating progress should come from the highest levels of management to the newest employee at the lowest pay grade. Employee evaluations are never fun for employees, but what would it look like if managers established a culture of honesty and transparency whereby evaluations would not have to be endured but welcomed?
Communicate
Closely related to trust is communication. Your warehouse staff should always be kept in the loop about the business developments that affect them.
You can achieve this level of communication by conducting weekly meetings. Along with discussing warehouse and inventory needs and upcoming orders and shipments, communicate that "we are here to equip you to succeed in the role you play on this team." Keep the human factor in the conversation.
Be flexible and allow your staff to bring up any issues that are affecting the workplace. This gives you the chance to act on them early before they grow into unmanageable problems.
You should also use weekly meetings to inform your staff about any business developments, such as new hires or changes in company policy. The more your employees feel they are informed about the things that affect them, the more they know you care about them. This kind of effective communication will inspire security, confidence and a united productivity.
Manage Wisely
In a warehouse, jobs are not always interchangeable, since many require strict certification and specialized training. Despite this, managers must take into account another critical factor in selecting the right employee for a specific job — a great attitude. Just because an employee can execute a job does not mean that he or she is the best candidate for that job. Pay attention to the attitudes of your employees.
A "team player," the person whose mission is in line with the company's mission, should always be considered even above those who possess greater skill. Skills can be taught, but a great attitude requires long-term modeling so that it can eventually be "caught" (with no guarantees that it will be either).
This is why wise delegation is so critical. You don't just want a job done right. You want team players who not only get the job done right but also influence the company culture to think the way they do.
Productivity is paramount to a company's overall success. Therefore, managers should train multiple "back-ups" for every job position. There is no reason to stop production if qualified substitutes are on hand and ready to take the place of the person who cannot fulfill his or her role. This is why understanding the roles of each employee is critical. Know what your employees are being asked to do and closely monitor how well each performs his or her respective duties.
As the warehouse manager, you must also be familiar with all federal and state employment laws that pertain to your staff. Keep informed about any passed or pending legislation that might require you to update your staffing policies.
Also, be aware of workplace safety regulations and understand all processes related to workers' compensation. These regulations change on a regular basis, so staying current will equip you to properly manage your warehouse and protect yourself, your employees and ultimately your company.
Provide Regular Training
Jobs evolve. Rules change. Equipment eventually requires fixing and ultimately updating. With every change taking place in the warehouse comes the need to communicate to the affected staff members how those changes will be implemented and what is required to make those changes possible.
As job descriptions change over time, each employee should be provided further training to meet the new demands of their respective roles. Training should ultimately equip employees to successfully fulfill their duties without the need for being micromanaged. Employees work at their best when they are equipped and empowered to be responsible and make wise decisions.
Another critical component that should be included in regular staff training is safety protocol. Go over safety procedures and remind your staff how to spot malfunctions or other hazards. Make sure to provide all of your employees with a readily accessible list of onsite and offsite emergency contacts should any warehouse emergency occur.
The better informed your team is, the better opportunities are available to them to make wise decisions in the workplace. When this takes place, everyone wins.
About the Author
Jerry Matos is a product specialist at Cherry’s Material Handling, which offers material handling equipment from industry-leading manufacturers including machine dollies, toe jacks, pallet trucks and more.
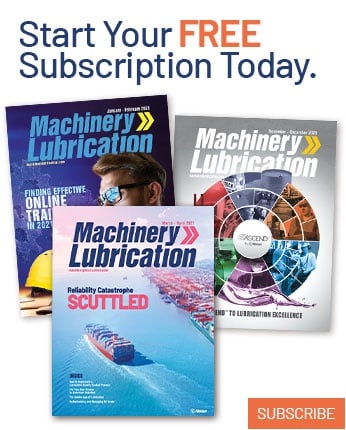