Many organizations are using their computerized maintenance management system (CMMS) as a record-keeping tool. If that’s all they want, a spreadsheet perhaps can suffice. A correctly used CMMS is a tool that goes way beyond record-keeping. By not fully utilizing the CMMS, maintenance operations are missing out on opportunities to save time and money. As the utilization of CMMS increases, overall productivity and profitability also increases.
Make sure you know the full functionality of your CMMS and plan ways to improve your use of it in the future. A CMMS gives you the ability to look at a massive amount of data that can be tracked over time, enabling you to make meaningful decisions.
Full utilization of the CMMS begins with the process flow.
The Ideal Process Flow
There are eight components of a good maintenance work process flow: notification, approval, planning, scheduling, dispatching, executing, follow-up and performance matrix. In my experience over the last 20 years, I always see three out of these eight key components. These are notification, dispatching and executing of work. Beyond that, however, the other five may not be in place at all or only in a limited form — for example, planning and scheduling. However, two categories that are consistently absent are follow-up and performance matrix, even in some of the most modern maintenance environments.
Follow-up/Continuous Improvement
A large part of follow-up involves reviewing and interpreting CMMS reports and completed work orders. Someone, most likely a planner or a supervisor, should review these items on a regular basis. Whether it is daily or weekly, these reports need to be consistently monitored.
Here are some examples of follow-up items:
Root Cause: By monitoring completed work orders, you may find that there is a repeated failure on a piece of equipment. This alerts you to the fact that there is a larger problem with the device. Maintenance workers are mostly working under stressful conditions, and they are almost always rushed. They often don’t have the time to properly diagnose the problem. Instead, they perform a quick-fix, and the problem will eventually occur again. If you are performing consistent follow-up, however, you can catch this and allow more time to fix the problem completely. This saves time in the long run as you aren’t repeatedly bandaging the same injury.
Data Analysis: A CMMS is a great tool for analyzing the data and making meaningful decisions. Examples include reviewing work-order schedule compliance, ratios of preventive maintenance and repair work orders compared to total work orders, and taking necessary corrective action.
Monitor Readings: Maintenance operations frequently gather readings on a variety of equipment such as boilers, chillers, etc. In a paper-based system, forms are filled out and filed away (never to be found again). Some companies have started using their CMMS to record and save these readings (i.e., pressure, temperature, etc.). The purpose of this data is to identify abnormal readings and correct problems to prevent failures. A CMMS is just the tool to accomplish that. Once you have defined a certain range and criteria, the CMMS will flag a warning immediately upon meeting those criteria. For example, if the temperature reading falls outside of a certain range, it will notify you instantly so you can take corrective action. Otherwise, it can turn into a catastrophic failure in the future. Maintenance planning can automatically incorporate usage and condition-based preventive maintenance, predictive failure maintenance and corrective maintenance resulting from abnormal readings.
Make the Most of Your Time: CMMS can be an excellent tool to identify non-value-added activities and shorten process cycle time as part of a follow-up/continuous improvement program. Maintenance spends a great deal of time waiting for parts, approval, instructions and equipment to be available. A CMMS can help identify where exactly maintenance is losing most of the time, enabling you to analyze the situation and correct it.
Follow-up and continuous improvement hinge on the same often under-utilized quality of a CMMS — data reporting. It is all well and good to track and store data, but it is useless if that data is never examined. By monitoring reports and completed work orders through a follow-up and continuous improvement process, you constantly make your operation more efficient. Higher efficiency means lower operating costs, larger savings and increased profitability.
About the Author
Kris Bagadia is the president of PEAK Industrial Solutions in Brookfield, Wis. A longtime consultant and educator, he can be reached by e-mail at krisb@peakis.com or via www.cmmsmadeeasy.com.
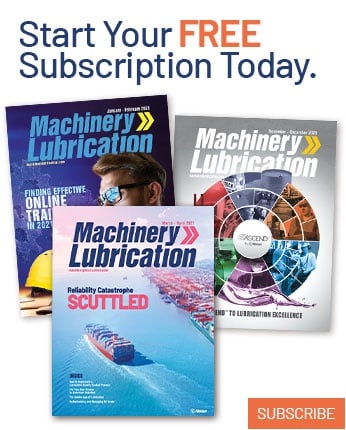