It seems as if new weight-loss programs and products come out every week. One of the latest is a plastic wrap you place around your stomach. If you strap it around your stomach, you will sweat and lose weight. Brilliant! Of course, you’ll probably sweat if you wrap anything air-tight around your stomach.
Perhaps the more interesting thought is to wonder why we fall for this stuff over and over when we all know the basic concepts in weight loss, such as:
- Less energy intake will reduce fat
- More exercise will burn fat
- More muscle mass will increase metabolism
If you know and understand these basic principles of weight loss, you can apply them and become very successful in losing weight. You will learn that it takes hard work to improve your metabolism and that it is a long-term lifestyle commitment, not a short-term project. This sounds awfully similar to reliability improvements, doesn’t it? Perhaps that is because both topics are maintenance, just with different equipment.
Lean is one of the newer concepts or buzzwords around maintenance. The lean philosophy encourages us to look at waste. What is waste in maintenance? Typically (not always), the largest waste is environmental and safety issues, followed by downtime of production equipment. There are also other losses such as damage due to catastrophic failures, wasted labor due to poor management system, high cost of parts and much more.
The key in the lean philosophy is to answer the question, “How do we reduce waste?” The answer is that we improve equipment reliability. As we all know, the key elements to improve equipment reliability are to have the following:
- Good leadership
- Planning and scheduling systems
- Preventive maintenance systems
- Spare parts management practices
- Technical database
- Root-cause analysis practices
- Engineering and design with consideration to reliability and maintainability
- Tools and workshops
- Skills development on all levels
The concept “lean maintenance” and all other new reliability improvement concepts often provide interesting angles and viewpoints, but you will end up with the same answers. To be quite honest, there are new technologies, but not much new has happened with work practices lately. The list above has been true since 1972. The hard part is doing the things in the list, not coming up with the list itself.
Lean is just another word used to convey doing the basics, but the angle is different. I recommend reading Shigeo Shingo’s classic book “Fundamental Principles of Lean Manufacturing” and applying the basic principles to reliability.
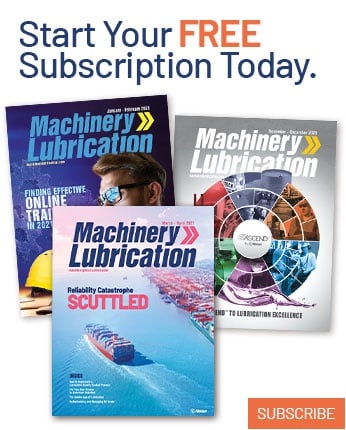