Reliability is important to every manufacturing operation. Successful reliability requires communication, cooperation and coordination. To learn the importance of these three Cs, let’s examine how your organization is structured and how it operates.
How much does unscheduled downtime cost and where does the responsibility for that unscheduled downtime lie? Is the unscheduled downtime because someone unilaterally decided to run to failure, or is it because the work request was in the “system” but not responded to in a timely fashion to preclude the unscheduled downtime caused by an unscheduled failure?
Does a competent operator know when there is an anomaly with the equipment? Since a good operator is a living, breathing data-acquisition machine, the answer is a resounding “Yes!” In the state of normal operation, good operators are cognizant of anomalies in the equipment they operate approximately one-fourth of the week.
A follow-up question that progressive, reliability-focused management should be asking is: “What is preventing the competent operator from communicating the impending failures of the equipment to the ‘system’ early enough to develop good job plans, identify the needed materials and resources, and schedule the repair in a timeframe that reduces unscheduled, expensive downtime and instead allows a quality repair to be done at a time that minimally impacts productivity?”
Does a craft-qualified, ethical maintenance tech have a desire to leave his name on a less-than-quality repair? As with the competent operator, the answer to this question is another resounding statement, “No!” Just as the competent operator wants to be known for producing a quality product at the desired rate, a qualified maintenance tech desires to leave his name on a quality repair that will not fail and be classified as a “maintenance-induced failure.”
This leads to another follow-up question that management should be asking: “What is causing less-than-quality repairs?” Do the materials management personnel, storeroom attendants and purchasing buyers feel frustrated because the management-designed “system” allows them to be the scapegoat for obviously controllable, but voluntarily uncontrolled product loss due to unscheduled downtime? Yes. You either voluntarily control downtime or voluntarily allow it to happen in an uncontrolled manner. The controlled or uncontrolled downtime is in the system that management has developed or allowed to evolve.
What is management’s mindset regarding efficiency and effectiveness? For example, take a NASCAR pit stop. Which is more effective and efficient – a pit stop that is scheduled, albeit in a short timeframe, or one that just happens somewhere on the oval track? It may seem like a rather inane question, but consider what you allow to happen routinely in your production-centric environment. Do you try to milk the last bit out of your system, ignoring the fact that well-maintained equipment is much more reliable and productive than ill-maintained equipment? Perhaps you are merely hoping that your stock car will get seven more laps on those bald tires and that the telemetry data on fuel usage is inaccurate. If the tires don’t make the seven laps or the fuel telemetry is accurate, you may end up with zero points in the standings.
Are your customers happy with getting the product that they contracted for, within specific parameters, delivered in a haphazard manner and time frame? You probably don’t accept transactions that way in your personal life. You expect the terms and conditions of the agreement to be met. The clients that purchase your company’s products expect the same fulfillment of their contracted expectations. If these expectations are not met for your customer, they will find another supplier because it is a competitive marketplace.
Reliability is the answer. Just as you expect your vehicle to start when you put the key into the ignition and turn it, so you have the same expectations with your manufacturing equipment. A major difference between your personal vehicle and manufacturing assets is that your personal vehicle is probably only driven by you, whereas the manufacturing equipment is operated by a succession of qualified people. This takes us back to the importance of the “system.”
How is your system designed? Are the communication, cooperation and coordination between the support pillars of your organization functional? In assessing how well your plant stacks up on the three Cs, start by answering some fundamental questions:
- Are problems being identified while they are small and not affecting the quality and quantity of your product?
- Are problems being addressed in a manner that minimizes adverse effects on equipment uptime?
- Is there a mutual acceptance of responsibility and ownership between the operation function and the maintenance function?
Operations should do an excellent job in making the product, while maintenance should provide quality and timely preventive maintenance (PM), predictive maintenance (PdM) and a well-managed and functional inventory in the storeroom, which is under maintenance control.
Both operations and maintenance must form a viable partnership of communication, cooperation and coordination of activities to ensure timely repair of identified malfunctions before minor malfunctions become catastrophic and affect productivity. There must be a realistic business case decision to manage between the short-term and long-term gain. You must be willing to take a short production loss now, in a controlled manner, scheduled at a time that minimizes the effect on productivity, rather than wait and take a longer, more devastating hit on productivity at a later date because you have chosen the uncontrolled path.
To be on a proactive, world-class path requires organizational functions to be mutually supportive, to communicate needs and observations, and to coordinate the effort, time, resources and knowledge necessary for mutual success.
About the Author
Al Emeneker, a subject matter expert at Life Cycle Engineering, has more than 30 years of experience in the maintenance repair and maintenance reliability fields with companies including Union Camp Paper Company, Fluor, the U.S. Air Force and South Carolina Electric and Gas. He can be reached at aemeneker@LCE.com.
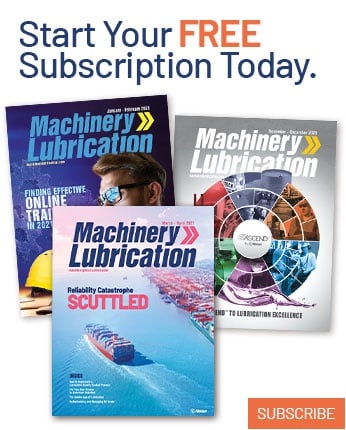