We tend to speak about financial issues more than moral issues in the business world. Safety is an issue that has significant ramifications from both moral and financial perspectives.
Safety is a financial imperative in today’s business world. According to a 2010 Liberty Mutual study, the annual documented direct and indirect industry cost of U.S. workplace accidents totaled $240 billion per year.
The average cost to industry for a fatal accident ranges from a low estimate by the National Safety Council of $1.27 million to the enormous average of $8.6 million per fatality paid out by BP after its refinery explosion.
According to an Air Force study, the average cost of a permanent disability is $1.3 million, while a partial disability costs $210,000. Workers’ compensation premiums, which correlate directly to your accident and incident rate, amount to millions of dollars per year in even a modest-sized company. Any way you look at it, accidents are expensive.
Dollars and cents aside, no manager or supervisor wants to ever have to face a distraught family and tell them that their spouse or parent will not be coming home tonight. It is hard to look an employee in the eye at the hospital when you know that his or her injuries could have been avoided.
Even minor injuries can take a serious toll physically, mentally and economically on everyone involved. I think we can all agree that accidents are an employee event that industry does not want to pay for and nobody ever wants to attend.
The premise of this article is that facilities that rank high in terms of reliability excellence also have superior safety performance.
There have been some statistics published that show the relationship between recognized measures of reliability and an organization’s safety performance. The source data has not been all that well-documented, but the relationship has been observed many times.
Improving safety should be seen as the journey toward reliability excellence proceeds. Rather than focusing on boring cost data and correlations, let’s explore why a state of reliability excellence supports excellence in safety performance. For it is from the “why” that you can learn how to improve safety performance.
According to the 2010 survey, the top five types of accidents in terms of compensation were falls, electrocutions, injuries from working in confined spaces, fires and explosions, and burns.
The causes of these accidents have their roots in unsafe conditions and unsafe behaviors. Both of these factors are positively influenced by the journey to reliability excellence. What sort of unsafe conditions and behaviors exist in reactive facilities that do not exist where reliability excellence is in place? Here are a few common ones:
- Leaks and spills that contribute to falls and some fires exist in plants where maintenance people are not deployed efficiently and “minor” defects like these have to be tolerated. Operators do not keep the equipment clean and in good order. Thus, the sources of leaks are not identified and corrected easily at an early stage.
-
Falls often result from temporary hoses and pipes, poorly barricaded “emergency work” areas, and the seemingly inevitable debris that there is “never time to clean up” before proceeding to the next emergency.
-
Electrocutions often occur because of poorly maintained electrical grounding systems and power tools. In a reactive facility, there never seems to be enough time to ensure that grounding checks are made, and that GFCIs are always used. Other electrocutions occur during emergency troubleshooting and repair of equipment. Often there is “not enough time” or the organizational discipline is lacking to perform LOTO consistently. Poorly planned high work near power lines is also a factor.
- Confined space injuries occur largely because of the lack of individual or supervisory discipline within the organization necessary to adhere to confined space procedures. Poor job planning and insufficient preparation for confined space entry also play a role. The absence of consistent employee training is often cited. Constant job interruptions and the rush associated with urgent work compound the situation by contributing to poor decisions.
-
Although falls account for the largest number of fatalities, fires and explosions always get attention. When you dig into the root causes of fires and explosions, you come across these contributors: poor configuration management (control of alterations to materials, process and procedures), leaks and spills, and lack of a disciplined adherence to procedures. In a reactive plant, procedures get bypassed and alterations and material substitutions are made to compensate for emergencies and poor material management systems. Leaks, spills and general poor housekeeping literally “add fuel to the fire” when one occurs.
- Burns not occurring as a result of fire are often attributed to hot liquid leaks. Leaks abound in reactive plants. In process plants, a very common cause is poor thermal protection condition, such as pipes and vessels with missing or damaged insulation. In a reactive facility, costs are high and manpower is generally scarce. Often one of the first things to be sacrificed is “minor” leak repairs and the condition of insulation.
These fundamental root causes are present in the top five accident types. Let’s explore how a reliability excellenceenvironment mitigates or eliminates these root causes.
Procedures and Discipline
No procedures or poor discipline to follow existing ones are characteristic of a reactive environment. Within reliability excellence, work processes and procedures are fundamental. Creation of process and procedure is one of the first steps taken in the implementation of reliability excellence.
Discipline results from setting expectations, measuring results and holding people accountable. It is also the reliability excellenceresult of establishing a culture that encourages and rewards a disciplined approach.
Disciplined does not mean stagnant. Structured continuous improvement is an integral part of reliability excellence, but the days of the “heroes” and “cowboys” are over. Reliability excellenceemploys the principles of change management to develop the right culture.
Planning
Poor or no job planning and a high level of emergencies set the stage for accidents. Lack of planning forces people to hurry and “make it up as they go,” creating opportunities for errors. In the reliability excellenceenvironment, more than 90 percent of jobs are planned and scheduled.
Emergencies are few because effective preventive maintenance programs are in place. Chronic failures are systematically identified and corrected, and the root causes eliminated by loss and failure elimination processes.
Insufficient Maintenance Resources
Reactive sites consume budget money and craft resources in huge quantities. The poor or omitted maintenance that creates an unsafe work environment often exists due to lack of money and people. When good work execution practices are in place as a result of reliability excellence, the productivity of the maintenance organization increases by as much as 25 percent.
Reliability engineers using effective loss and failure elimination processes significantly reduce the number of chronic failures. These and the preventive and predictive maintenance programs developed and deployed in a reliability excellenceimplementation extend the equipment mean time between failures and eliminate much unnecessary emergency work.
The overall cost of maintenance goes down, while the level of maintenance goes up as resources, once poorly utilized reactively, are now available for proactively addressing all of the maintenance needs of the site.
Poor Housekeeping
“Temporary” hoses and pipes as well as debris left behind from emergency repairs or only partially completed maintenance create an unsafe work environment. In a proactive environment, emergency repairs become the exception. Craft people are not pulled away from partially completed jobs to deal with the next emergency.
In addition, every job includes the time to render the work area safe and clean before moving to the next job. General housekeeping improves as well. Indeed, 5S is integral to reliability excellence. Clear expectations and scheduled tasks generated by the operator care function result in operators who have the time, the ability and the desire to maintain a clean and safe workplace.
Lack of Configuration Management
Uncontrolled changes often create unsafe process and equipment conditions. There is a history of major industrial accidents resulting from poor control of changes. Condition monitoring is one of the fundamental components of a reliability excellenceimplementation, thus ensuring an appropriate level of procedural safeguards is in place.
Often the need to make changes is the result of a reactive environment. Parts and material substitutions occur when the material management function is not working, and a breakdown occurs. World-class material management practices ensure that the right parts in the right amount are at the right place at the right time.
The failure elimination process eradicates most chronic and unpredictable failures. Between the two, much of the need for emergency work-arounds, which are often the drivers for configuration management failures, simply goes away.
Lack of Training
Either from neglect by reactive leadership or from lack of necessary resources, training is often poor quality or non-existent. With reliability excellence comes reduced failure rates, less severe failures, more productive use of craft labor and the ability to schedule effectively.
Process interruptions become rare. Both the time and money to train your people become available. The world-class target of 2 percent of labor hours devoted to training becomes not just possible but desirable. Root-cause analysis of failures helps to target specific training needs. Tracking systems that are integral to the process validate the effectiveness of your training dollars.
Poor Decision-Making/Errors
Lack of process, asset and organizational stability in a reactive environment forces people to make decisions under time pressure, often reacting to totally new situations. Process upsets and equipment breakdowns generate overtime, which is frequently excessive and unplanned. This leads to fatigue, which leads to poor decision-making and errors and accidents.
Human-error rate tables indicate that the average trained and competent person performing a routine repetitive task under no unusual stress will make a mistake roughly once every 500 times he or she performs it. Add fatigue, being in a hurry and having to perform non-routine tasks, and the error rate increases to roughly once in every 25 actions.
In the right (or rather wrong) emergency conditions, the error rate can be as much as one in four. It is little wonder that the accident rate is so high at facilities that have unstable processes and unstable equipment. Reliability excellence introduces stability, predictable work schedules and lower stress.
Management Focus
In sites where it is a daily battle to make production and keep poorly maintained assets running, it is hard to find the time to focus on improving safety. When assets and processes are stable and under control, when you have the resources to maintain the facility at peak condition, and budget pressures are lower, then you have the time, energy and ability to focus on safety. Reliability excellence creates this very environment.
In summary, whether for moral or financial reasons, reliability excellence is an imperative for a safe and profitable business.
About the Author
Sam McNair is a senior consultant with Life Cycle Engineering (LCE). A professional engineer and Certified Maintenance and Reliability Professional, Sam has more than 32 years of experience in discrete manufacturing, chemical process industries, mining, machine processes, automation, aviation, construction, and utilities. Sam specializes in reliability engineering with a focus on the integration of maintenance and manufacturing functions. You can reach Sam at smcnair@LCE.com.
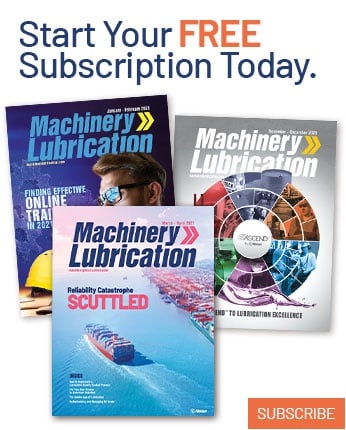