I was recently facilitating a "Maintenance and Reliability for Managers" four-part series course at a particular site when the subject of planning was raised by one of the supervisors attending. As part of the conversation, he commented “but gee, Jeff, I’m planning for my people now”. As it was Tuesday, I asked if he was planning for next week’s schedule or this week. His reply is like so many that I hear, “No, I’m planning for this week, actually two days from now.” Mind you, his site has a planner scheduler. I went on to ask, if the supervisor was doing the planning, who was doing the supervision – i.e. removing obstacles from jobs in progress, determining the development needs of the people, controlling time lost during and between jobs, etc. In the end, it wasn’t him. Turns out no one was performing that function. It begs the question, if the supervisor is doing the planning, what is the maintenance planner scheduler doing? That’s another story for a different day. The goal of maintenance planning and scheduling is to drive out the inefficiencies of what are typically an organization’s most expensive hourly resources – the maintenance technicians. No, we aren’t trying to make them work harder. We are trying to just help them work smarter by providing a level of organization to the chaos that normally accompanies a reactive world. While better than no planning, planning jobs for a day or two days away often doesn’t allow us time to reduce costs associated with expedited freight or making everyone jump through hoops to accomplish the job. No doubt, there always will be jobs that need to be completed in two days (or tomorrow for that matter). Jobs that happen in this manner are still very reactive by nature. That’s not what we want in a proactive, reliability-centered environment. Ideally, we put this week’s schedule together last week, and all of the stakeholders agreed that the items listed were the ones that the organization wanted to accomplish. In establishing the schedule, we chose work based on our priority matrix (high to low) and on 100 percent of the available labor hours that we anticipated for this week. So, if the supervisor is planning and executing jobs in this week, that means we are breaking the schedule. “Can we break the schedule?” you ask. Sure, but that usually means that some other work that we placed on the schedule is not getting done, as we scheduled 100 percent of our available labor resources. When we break the schedule, we should ask the following:
- Assuming that we have the parts to do the work, are we breaking the schedule for work that is more important than the work on the schedule?
- Is it work that really could be planned and scheduled next week?
Another item that many supervisors don’t stop to consider is how doing work in the current week outside of the week’s schedule affects our metrics. Using the example of breaking the schedule gives a lower schedule compliance number if work that was scheduled during the week is not completed. Remember, schedule compliance is a measure of “did we do what we said we were going to do on the schedule?” If the work that didn’t get completed is a preventive maintenance / predictive maintenance activity, we get a double-ding when PM compliance is added to the mix. Again, it’s OK to break the schedule if business requirements demand it, but it’s not something to take lightly. What, you aren’t measuring your performance or key indicators? How do you know where you are going if you don’t know where you are? If you would like a listing of some key metrics you should be monitoring, send an e-mail to me at jshiver@peopleandprocesses.com. I’ll also be happy to answer other questions about maintenance planning and scheduling as well. Just shoot me an e-mail or reply below.
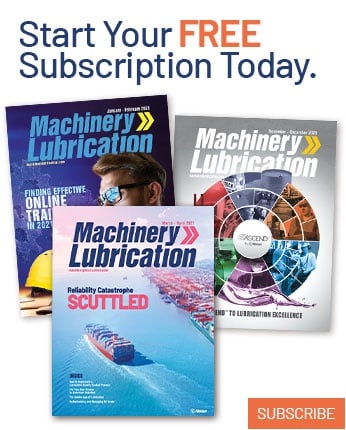