Numerous process improvement methodologies have been proposed in recent years. Three of the most prominent are Six Sigma, lean and the Theory of Constraints (TOC).
How can you determine which methodology is the right one for your organization? While the ultimate goal of all three is to increase profit, their more immediate goals to accomplish this vary:
Six Sigma - consistently meet customer expectations
Lean - add value for the customer
TOC - increase throughput
What are some additional characteristics, differences and similarities of these approaches?
Six Sigma
Six Sigma is a data-driven approach that focuses on reducing variation in order to solve both process and business problems. It applies a very structured and rigid methodology to meet customer specifications and assumes that variations are the cause of defects that impact customers negatively.
Six Sigma also assumes the entire process to which it is applied will be improved by implementing variation reductions for multiple elements. The methodology encompasses five steps:
Define – Determine, who are the customers, what are their problems, and what are the process elements and output conditions?
Measure – Categorize key characteristics, verify measurement systems, collect data
Analyze – Convert data into information, identify most important causes of problems
Improve – Develop solutions to the problem, implement changes, evaluate results through measurements
Control – If performance is now as desired and predictable, put it under ongoing control to ensure consistency
It is also hoped that the focus on reduction in variation can produce other secondary effects, such as quality improvement, elimination of superfluous elements and a decrease in errors.
Lean
Lean thinking, or lean manufacturing, as it is sometimes called, focuses on the removal of waste, defined as anything that is not necessary to the production of the good or service and does not add value to the final customer.
There is an emphasis on the flow of processes. Some of the assumptions underlying the methodology include that waste is the main limitation on profitability and that many small, rapid improvements are more beneficial than analytical study. The approach consists of five steps:
-
Identify features that create value (either for the ultimate customer or a subsequent process)
-
Identify the value stream, i.e., the sequence of activities which contribute to the value for the customer; determine whether activities which do not contribute value are, nonetheless, necessary
-
Make the activities flow with minimal interruption; common flow inhibitors are queues, batch processing and transportation
-
Allow the customer to pull product or service through the process; provide it only when the customer needs it
-
Perfect the process; continually attempt to remove non-value activity, improve flow and meet customer needs
As with Six Sigma, it is hoped that lean’s focus on eradicating waste and enhancing flow will have some secondary effects, including quality improvement, process acceleration, and reduction of constraints and obsolescence.
Theory of Constraints
The Theory of Constraints (TOC) logic-driven approach focuses on system improvement. It views the system as a chain of interdependent links that work together toward the primary goal of transforming inputs into sold outputs, thereby increasing throughput (the rate at which the organization generates goal units – usually dollars).
The performance of the entire system is limited by the weakest link, or the constraint. All improvement efforts should be aimed at this constraint through the use of five focusing steps:
Identify the constraint – can be a physical process or a policy
Exploit the constraint – decide how to do everything possible to utilize the constraint to its maximum capability
Subordinate to the above decision – all other activities should be adjusted to support and defer to the constraint, to insure it operates at peak effectiveness
Elevate the constraint – if system performance is still not satisfactory, consider investments to improve or eliminate the constraint
Repeat the cycle – once the previous constraint is broken, go back to Step 1 and identify the new constraint; before starting again, be sure that old habits, policies and rules are re-evaluated considering the changed environment.
Assumptions include that the speed and volume at which products or services travel through the system are primary determinants of success, and, therefore, removing the constraint will improve profitability.
Secondary effects include protective inventories, quality improvement, reduced variation, and a positive impact on flow and, therefore, throughput.
Choosing the Right Methodology
How can you determine which methodology is the right one for your organization? One of the main distinctions between TOC and the other two methodologies is TOC’s extensive focus on the system’s constraint, while the other two approaches are not targeted in this manner.
While it may appear attractive on the surface to make improvements anywhere they can be made, economic reality is that resources are limited. Hence, TOC dictates that you want the most improvement possible for the least investment.
Efforts to improve all of your organizations individual processes at the same time could actually have a detrimental effect by hindering your ability to meet your customer’s needs and provide your product or service when it’s needed at the lowest cost.
Another consideration is that TOC’s focus on one specific constraint at a time requires only a relatively localized effort.
Therefore, extensive data analysis and involvement of the entire work force is not critical to success as they are with Six Sigma and lean. Significant results can be expected with TOC after just three months of effort.
If you are already utilizing one of these approaches, there are ways in which the methodologies can complement each other, especially with regard to exploiting a constraint identified through a TOC effort.
Six Sigma can be a tool for getting more throughput out of a constraint, and lean thinking can help eliminate any waste associated with it.
They might also be used to drive out disruptive variation or reduce waste associated with non-constraint processes that interfere with the constraint, as well as to make sure the constraint is never starved or fed inferior inputs.
Some precautions should be taken, though. First, take care not to drive out waste to such an extent that the protective capacity vital to buffering the constraint is also eliminated.
Second, be aware of the differences among the methodologies with regard to balanced systems. While lean and Six Sigma will tend toward balance throughout the system, TOC relies upon an imbalance in the form of focus upon the current constraint.
Although the flow throughout the system should be balanced, the capacity should not – only the constraint will continually operate at maximum capacity.
In conclusion, be sure not to waste time and resources on strengthening system elements that are already strong. Focus your efforts where they will produce the best return.
TOC can guide you through the process of identifying and breaking your organization’s constraints, increasing your throughput and realizing the dramatic benefit to your bottom line.
Method of success
-
Assess the current situation, immediate threats, longer-term needs, effort required and impact of moving from a “push” to a “pull” system
-
Gain top management buy-in to the assessment and approach
-
Build knowledge and understanding across the supply chain, at all levels
-
Utilize systems that deliver actionable information, integrated with your existing software
-
Work until expected results are achieved
About the author:
Debra S. Renard is the director of project management for IDEA LLC, a supply chain management consulting firm based in Charleston, S.C. To learn more, visit www.ideallc.com or e-mail tomdemuth@ideallc.com.
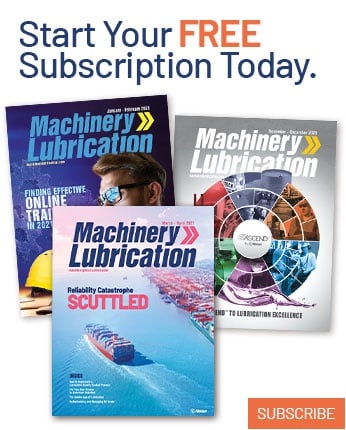