Are you experiencing equipment failure even with what you consider a good preventive maintenance program? What questions are you asking about the failures? Are the “five whys” tying back to the actual PM tasking? Or are the “five whys” pointing to something else? Is the PM tasking appropriate for the results expected on the specific equipment?
Many of us have had the wonderful experience of the expectation of children through the miracle of pregnancy. There are many things that need to happen and many checks and inspections that should be done to ensure the health and safety of the child and the mother. Those physicals and routine check-ups are, for the most part, common knowledge among the educated and well-read parents that are concerned about the present and the future of the family.
Now, consider where most of the focus is. On the mother and the child, correct? Most people focus on what is needed and necessary to ensure the health, well-being and safety of the mother and child. What about the car? When the contractions reach approximately three minutes apart and it is time to go to the hospital, the last thing anyone, especially the husband, wants is to throw the pre-packed suitcase in the car, load the already uncomfortable mother and get her strapped in, and then have the car refuse to start. One can feel the tension rising. Which of the family members is responsible for the maintenance of the car?
I know you are thinking the man is responsible! You can’t get away from that, given the boxes we are thinking in. If we consider the woman to be the “operational” entity, since she is the one producing the “product”, and the man to be the “maintenance” entity and the one responsible both for the vehicle “equipment”, then we have some questions to ask and answer. Questions without answers don’t help in the pursuit of equipment reliability!
In both the family entity and the manufacturing and service entity, operations and maintenance are required to produce the product. Here are some questions to answer to help maintain the health, welfare and safety of the products delivered:
-
Is the PM procedure adequate for the equipment?
-
Is the PM procedure adequate for the operating parameters? Have the production rates been changed from design?
-
Is the existence of standard work instructions a requirement?
-
Is the adherence to the standard work instructions a requirement for both operations and maintenance and the routine auditing of standard work instruction adherence a routine factor in the culture of the facility?
-
Are the intervals of the PM inspections adequate to allow the procedures to functionally prevent failure maintenance in any manner, except planned and scheduled programmed and corrective maintenance that is accomplished in a controlled manner, with minimal impact on production? Are you routinely mining and refining the knowledge and expertise of the operators and crafts to enhance the reward of the specific PM procedure and tasking?
-
Are your reliability engineers applying their talents to addressing less than functional PMs?
-
Are your crafts capturing and coding the PM work orders appropriately to allow the reliability engineers the necessary forensic data to improve and tune the specific equipment PMs?
-
Are your planners, in conjunction with operations and maintenance, ensuring the timely scheduling of preventive maintenance inspections for compliance completion?
After the birth of my first child, I became almost paranoid about the reliability of my vehicle to start and run. One doesn’t take a pregnant woman to the hospital in the middle of the night unless it is time. Likewise, life can become very anxious if she isn’t at the appointed place when it is time. My wife was really good at making sure I was certain the vehicle was functional and ready!
Preventive maintenance is not a maintenance-only effort. Preventive maintenance is not an operations-only effort. There is a tremendous amount of communication, cooperation and coordination required by both parties to ensure PMs are effective. Rather like a family situation, wouldn’t you say?
This article first appeared in the Life Cycle Engineering newsletter RxToday.
About the author:
Al Emeneker, a subject matter expert at Life Cycle Engineering, has more than 30 years experience in the maintenance repair and maintenance reliability fields with companies including Union Camp Paper Company, Fluor, the U.S. Air Force and South Carolina Electric and Gas. You can reach Al at aemeneker@LCE.com. For more information about Life Cycle Engineering, visit www.LCE.com.
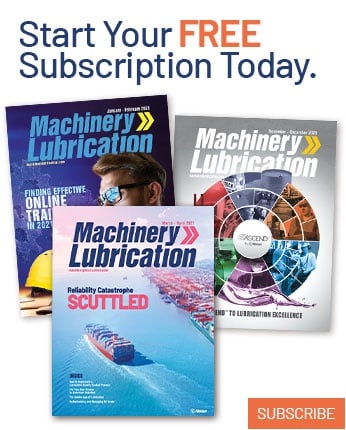