The term reliability was discussed in my last column. I argued that maintenance should be responsible primarily for “equipment reliability” and work in a close partnership with operations, whose primary responsibility is “process reliability,” and engineering would control life cycle cost (LCC).
In this article, I will suggest how plant management can plan a clear path toward reliability improvements. It’s common for us to have an unclear or disjointed view of what actually needs to be done in order to excel in reliability. For example, is there a unified plan for achieving higher equipment reliability before we start new projects? Do all involved employees understand the plan and how it’s to be executed? If not, let me suggest a simple approach to create a plan. Create a detailed plan by following these five steps:
1) Get all necessary people involved. If someone creates a plan alone, there will be no buy in. It’s as simple as that. The creation of a valid improvement team and awareness of the reliability process is the most important process step. Unfortunately, this step is often forgotten. Here are some important things to think about when creating the team:
- The team must have clout in the organization and management must take part.
- Involve operations, maintenance and engineering.
- The bigger the team, the more buy-in.
- The bigger the team, the longer the process will take.
- The facilitator must create reliability awareness by having a good plan in mind.
- The facilitator must be respected by the organization and viewed as a leader for the improvement effort.
2) Create a vision and mission statement for maintenance management. A vision statement explains where a plant wants to be in the future. A mission statement explains how the plant gets there. A simple example that has worked well in the past:
- Vision: We will achieve 80 percent of our agreed-upon best practices by 2010.
- Mission: We will execute the best practices.
Keep the mission and vision statements as simple as possible.
3) Create a checklist for best practices. The best practices in maintenance management are actions that will cost-effectively improve equipment reliability. By executing the items in the list, your plant should believe it can achieve better equipment reliability and, therefore, lower costs.
Organize best practices in a simple format. It’s a good idea to divide the best practices in work processes. Define work processes by documentation, execution and follow-up. For example:
- Document a definition for a planned job.
- Execute job planning according to the definition in point 1.
- Follow up by assessing the percentage of jobs that are correctly planned. Another example:
- Document condition monitoring on- the-run inspections for mechanical equipment.
- Execute the condition monitoring routes described in point 1.
- Measure (follow-up = route compliance and number of corrective work orders initiated by doing condition monitoring routes for mechanical equipment).
In my experience, you’ll end up with approximately 250 to 350 points by describing maintenance management in this fashion..
4) Prioritize the checklist and create a detailed plan. Prioritize the items the plant should work on by assessing current performance against the best practice checklist. Select only a few items and make a detailed implementation plan for each item, including training and support.
5) Audit plan progress by using the best practice checklist. To become instituted, monitor and reinforce any process improvement or project. Use the checklist to assess how well the organization is performing. I suggest you create a scoring system and create a gap analysis report for auditing purposes.
Torbjörn (Tor) Idhammar is partner and vice president of reliability and maintenance management consultants for IDCON Inc. His primary responsibilities include training and implementation support for preventive maintenance/essential care and condition monitoring, planning and scheduling, spare parts management, and root cause problem elimination. He is the author of “Condition Monitoring Standards” (volumes 1 through 3). He earned a BS in industrial engineering from North Carolina State University and an MS in mechanical engineering from Lund University (Sweden). Contact Tor at 800-849-2041 or e-mail info@idcon.com. |
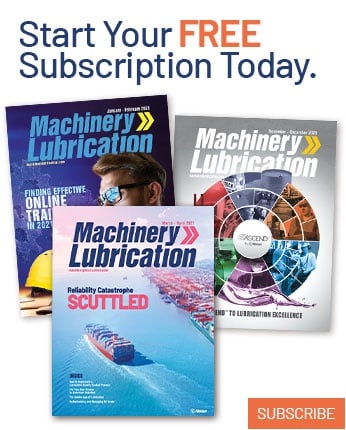