When Hank Coffin wanted to improve the performance of his maintenance team, he started with the basics. Keeping a power plant up and running is critical for more than just that company and its profits – thousands of people depend on it for their electricity.
Coffin, a manager at PPL Montana’s Colstrip Steam Electric Station in the southeastern part of the state, realized that keeping his plant – and its four generators – running requires understanding the value and impact of proper maintenance and repair. So, he decided to contact Timken to flesh out the needs of PPL Montana.
To help fine-tune operations at PPL Montana, Timken worked with Coffin to set up an onsite training program that would help his maintenance team learn techniques to extend bearing life, reduce costs and improve equipment reliability.
“Providing our customers the opportunity to continue their education in best maintenance and repair practices is a value-adding service that can deliver exceptional results,” said Jeff Calvin, Timken section manager for service engineering – bearings. “The Timken Bearing Certification program helps us to make them better at their everyday practices, which improve operations and performance.”
The program is a tool used to help customers focus on each area of maintenance and learn techniques for good practice. Customized to each customer’s unique needs, some key areas of the training include review of proper bearing storage, handling, inspection, and installation and removal processes.
Re-educating his team at PPL Montana, Coffin can see the impact of the training on a number of levels.
“I realized that all of our guys didn’t have the same level of training and knowledge, so the benefits of the program have reached a number of layers to improve our overall operations,” said Coffin. “Our steam plant mechanics and operators, supervisors and PE-licensed engineers have all learned from the program. And with everyone on the same page, we have a lot better success with bearings.”
Following the onsite training and auditing, PPL Montana earned the “Timken bearing certified” designation, reserved for world-class maintenance operations. Since beginning training, the more than 1,100-megawatt coal-fired power plant has significantly improved uptime and maintenance costs.
Through improved education and knowledge of maintenance practices, PPL Montana also has gained a first-hand look at the benefits of bearing repair vs. bearing replacement. Understanding the bearing and its environment assists in recognizing the need for scheduled repairs before breakdowns cause delays.
“Learning the benefits of bearing repair are reflected in both performance and the bottom line,” said Coffin. “We’ve noticed a definite improvement in the availability of equipment and are saving one-third to one-half the cost of buying new since we’ve started capitalizing on bearing repair.”
“What’s more important is that Timken doesn’t care if it’s their bearing or that of a competitor,” he explained. “Either way, they help us fix the problem; and because of that, I’ve gained a new respect for them.”
For more information on Timken products and services, visit www.timken.com.
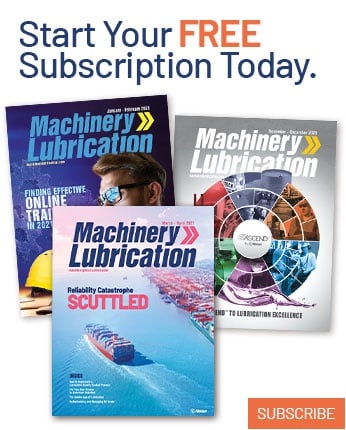