You could tar your roof with it. It sticks to everything. It spreads like cancer. You thought you were getting rid of it with the oil change and flush, but it is back again – lurking in your oil and gripping the insides of your machine.
Does this sound familiar? Maybe you have it now . . . sludge and varnish. Do you know what causes it and how to stop it from spreading? Do you know how to prevent it from coming back later? More importantly, do you understand its destructive potential?
More Cases of Affliction
In industrial equipment, Noria Corporation has seen a surprising surge in sludge and varnish (S&V) cases in recent years. There are many possible explanations, but perhaps the biggest contributor evolves from the increasing demand for machinery reliability. Today, there is more awareness in the user community of the impact that S&V has on lubrication and machinery health. People are making closer inspections, asking more questions and are less tolerant of its presence.
Additionally, the increasing use of low-solvency basestocks (for instance, hydrocracked and polyalphaolefin synthetic) could be amplifying problems. These basestocks, on one hand, are more thermally and oxidatively robust. On the other hand, they may be more prone to lie down and coagulate oil degradation products (oxides, salts, carbon fines, etc.), leading to sludge and varnish.
Also, more users push lubricants to the limits by extending oil drains and, in some cases, improperly top-treat in-service oils with additive concentrates. Many used oils are now being reconditioned and returned to service or blended with new oil. In certain instances, these somewhat progressive practices may lead to more frequent and severe S&V problems.
In addition, many organizations are doing a better job at controlling leakage through better maintenance. Oddly, this can contribute to more frequent cases of S&V. When leakage is reduced, so, too, is the replenishment of fresh additives and basestocks that come in with makeup oil. This has the practical effect of shortening the oil’s life.
Sludge and varnish can take many forms. Here, varnish
appears as a gold adherent film on this valve.
In contrast, companies generally are maintaining equipment cooler, cleaner and dryer than in the past, and are better at deploying oil analysis. These improved practices normally have a positive and stabilizing effect on lubricant health and reduce the risk of S&V problems.
Causes of Sludge, Varnish
The approach of detecting and analyzing S&V problems in machinery is not the same as used oil analysis. In many instances, this is because the evidence is not always in the oil. The sludge and varnish should be analyzed directly, using a completely different set of tests and evaluation parameters. Still, used oil analysis plays an important diagnostic role to help reveal candidate causes as well as rule out others.
The conditions that commonly lead to S&V problems vary, which complicates the process of identifying the root cause analytically. There are at least 25 unique lubricant degradation mechanisms leading to S&V formation. A few of these include:
- Aeration of the fluid
- Sparking from static electricity
- Bulk thermal degradation
- Antifreeze contamination
- Soot coagulation
- Bulk oil oxidation
- Hydrolysis
- Prolonged cold storage
- Grease contaminated oil
- Caustic detergent contamination
- Nitration coking on hot surfaces
- Radiological contamination
- Poor engine combustion efficiency and blowby
- Highly aromatic fuels
- Sulfation (fuel, H2S, etc.)
- Lead corrosion reactions
- Reactive compressor gases
- Additive incompatibilities
- Base oil incompatibilities
Upon looking at the above list, it is obvious that the prescribed corrective action relies on the accurate discovery of the specific, and often elusive, root cause. Without this, correcting the problem is reduced to the costly and lengthy process of trial and error. There is a unique remedy for each cause. It’s always good advice to keep an accurate history of the conditions and observations that lead up to the occurrence of S&V. The troubleshooting process depends on building a case file containing each little piece of information and a timeline.
Machine Inspections
Lubricants degrade in different ways, and the products of this degradation are essentially referred to as sludge and varnish. These products are generally unstable in the oil and, as such, are looking for a place to land – that is, to be deposited. In certain instances, the deposits form on machine surfaces at the exact location where the oil degraded (for example, hot surface coking). In other cases, the oil degrades in one location but deposits condensed on a surface elsewhere.
Over time, some deposits can thermally cure (become baked-on) to a tough enamel-like coating. Other types of deposits, generally in cooler zones, remain soft or gummy. Sludge is not always black or even dark. It may appear clear and grease-like, similar to petroleum jelly. The following are examples of where and how S&V might occur:
- Black crusty deposits on mechanical seals
- Gold adherent films on spool valves in electrohydraulic control systems
- Charcoal-like deposits on babbitt sleeve bearings
- Gooey-brown mayonnaise on diesel engine oil filters
- Black scabby deposits on thrust-bearing pads
- Lumpy, tar-like globs in dryer bearing drain lines (paper machine)
- Grayish gummy deposits on natural-gas engine discharge ports
- Carbonaceous residue on servo strainers
- Hard black enamel on piston crown and ring lands
- Cottage cheese-like gunk clinging to engine valve covers
- Drab-color slime on compressor oil filters
Damage Caused
The deposits that form on machine surfaces interfere with the reliable performance of the fluid and the machine’s mechanical movements. They also can contribute to wear and corrosion or just cling to surfaces. For example, deposits on the spool of a servo control valve can tighten the interference fit between the spool and bore. Compounding this are the adherence properties of varnish, which can stick particles from the oil to silt lands, leading to common silt-lock valve failure.
Other types of sludge and varnish-type failures include plugged orifices, damaged mechanical seals, plugged discharged ports on compressors, journal bearing failure, premature plugging of oil filters and diesel engine combustion-zone wear.
Most organizations that suffer from S&V problems have these three needs:
- They want to know the root cause of the problem.
- They need simple solutions to quickly return the lubricant and machine back to service.
- They want to know how to prevent the root cause from reoccurring.
Because of the impact S&V has on lubrication and machine reliability, for the past several years, Noria has been on a crusade to learn everything possible about it. We have conducted extensive laboratory investigations. We have amassed stacks of analytical material. We have conferred with experts and academics. We have combed through hundreds of pages of technical literature. And, we have gone to the field to see it in the machines where it lives.
Do you have a problem you’ve encountered relating to sludge and varnish? Have you learned something new about how it forms or had a success in solving a problem? If so, please share your experiences.
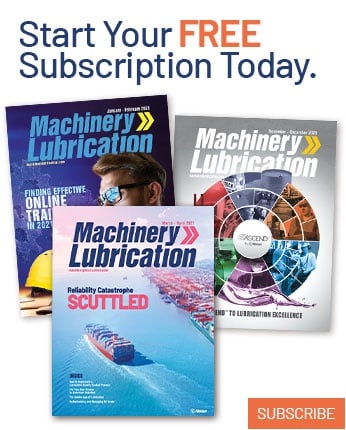