The demands placed on bearings for wind power plants are extremely high. Therefore, the procedures for bearing selection and lifetime calculations are fundamentally different than selecting bearings in other application areas.
When selecting bearings for industrial use, design engineers can choose bearings for a defined bearing location relatively easily, working together with their suppliers if necessary, and basing their decisions on parameters such as rotary speed and torque, radial and axial load, and the required rigidity and preload or clearance. The wide range offered by complete providers such as NSK means that the right bearing is always available, even for unusual applications or special operating conditions. If this is not the case, special customized bearings can also be used.
Exacting requirements
In wind power technology, the procedures leading up to the selection of a bearing are fundamentally different, essentially because of a single parameter: the bearing lifetime. The manufacturers of wind power plants and the gears for those plants require a bearing lifetime of 20 years (i.e. 175,000 hours) for their bearings. This is already an extreme value, but it does not cover all requirements. In addition, it must be taken into account that external loads acting on the bearing are highly dynamic (that is, irregular) because of the wind. The unfavorable environmental conditions for offshore facilities, used ever more frequently, are another factor: sea air is highly corrosive. For generator plants, electrical corrosion must also be taken into account. Finally, the service options available to wind farm operators are extremely limited, and any unscheduled downtime for a bearing will result in significant costs.
The importance of calculating lifetime
Just calculating the lifetime of this type of bearing requires a large degree of expertise. This is why selecting bearings for wind power plants is more complex than in other areas of use. Numerous parameters must be taken into account. Besides the bearing loads and the rotational speeds in the application context, design engineers must consider the construction in which the bearing will be placed – i.e. the configuration of the shaft and housing, their materials, and their tolerances.
Based on this data, first the conventional, standardized calculations are made in accordance with DIN ISO 281, also known as the catalog method. The parameters are bearing load, rotational speed, load capacity and bearing type. In further calculations, parameters such as temperature, lubrication and purity of the oil also are taken into account.
Greater precision than required by the standard
Appendix 4 of DIN ISO 281 assumes a simplified bearing geometry as the basis for calculating the modified reference lifetime. In most cases, this sort of calculation is adequate. However, in the wind power industry, more precise values are preferred. NSK has developed its STIFF software for this purpose. In calculating the bearing lifetime, STIFF also takes into account the exact internal geometry, the running clearance and preload, deformation of the shaft-bearing system, and the load zone and load distribution between rolling elements and bearing raceway.
In this model, the rolling elements are divided into slices. An individual, modified reference bearing lifetime is determined for every slice. A more realistic indication of the total bearing lifetime is obtained based on the share of time for each load case.
Targeted design optimization
Apart from fast and precise calculation of the bearing lifetime, the STIFF software also allows short-term version analyses and thus optimization of existing designs. In addition, special adaptations of the bearing can be tested quickly. This particular advantage is frequently exploited: Customized bearings are often used in wind power technology precisely because of the exacting requirements. Furthermore, predictions of rigidity, estimation of efficiency loss, and investigation of operational safety are part of the calculation objectives pursued by the NSK Wind Energy unit when selecting bearings.
Engineering to the fore: Intensive cooperation with customers
Given the amount of data that must be taken into account in this area and the demanding bearing lifetime requirements, it is not surprising that such projects are always executed in close cooperation with the customer. Along with engineering, testing also plays an important role. NSK has designed bearing test rigs that allow simulation of dynamic loads and motion. These include, for example, a large bearing test rig capable of applying dynamic forces and moments from the rotor load, and a test rig for simulating acceleration and deceleration and braking procedures for rapidly rotating roller bearings.
Super-TF technology for wind power technology
Aside from the selection of the bearing design, the choice of material also plays a crucial role: A bearing lifetime of 175,000 hours, for example, under unfavorable conditions and dynamic loads can only be achieved through the use of special materials. That is why NSK has drawn on its many years of material expertise to develop special materials suitable for extreme operating conditions. One such development is the Super-TF technology. This technology deploys a high-purity bearing steel combined with a special heat treatment technology, guaranteeing an optimized retained austenite content. This material ensures that any foreign matter that penetrates the bearing generates less stress in the material than in conventional steel. As a result, damage from impurities occurs less frequently.
Bearings made from this material and used with a clean lubricant have roughly twice the lifetime. The Super-TF technology can be used for a large range of bearing types, such as cylindrical roller bearings, which are among the most frequently used bearing types in wind power technology, as well as for tapered and spherical roller bearings.
Different types of bearings
In modern wind power plants of the megawatt and multi-megawatt classes, multi-stage planetary gears and differential gears primarily provide the necessary speed reduction of the main power train. In this case, design engineers must select not just the appropriate bearing type but also determine the type of bearing arrangement. Bearing assemblies with fixed and free-end bearings, an adjusted bearing assembly or a floating bearing assembly are available.
Every bearing type has certain advantages and disadvantages. An adjusted bearing assembly that allows precise guidance of the shaft, particularly in the axial direction, therefore runs the risk of reciprocal tensioning. Therefore, bearing assembly types such as tapered roller bearings, which allow axial forces to be accommodated in at least one direction along with radial forces, must be selected here. The same applies to floating bearing assemblies, in which the shaft can move axially for a certain distance. Fixed and floating bearing assemblies are used, for example, in bearing designs for planet carrier and planet wheels.
New designs for main gears
In addition to the trend for higher and higher performance and offshore facilities, new drive and gear designs also present design engineers with new challenges. NSK is working closely with the manufacturers of wind power plants and their drive components. The goal is to help develop new designs (that increase the efficiency of wind turbines or reduce weight in the nacelle, for example) for the market quickly and give their users a competitive advantage. NSK has the advantage of more than 20 years experience in developing bearings for the wind power industry an advantage that also benefits users of bearings outside the wind power sector.
For more information on NSK products and services, visit www.nsk.com.
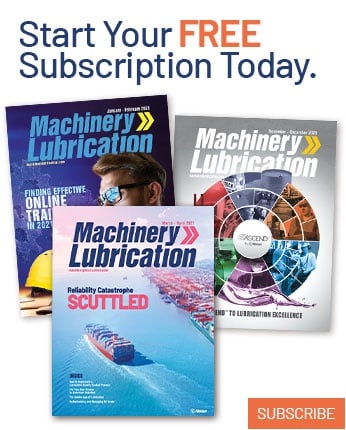