There are two types of run-out specified for bearings: radial run-out and face run-out. Radial run-out is the variation of wall thickness in a bearing race. In technical terms, run-out is the measurement of the raceway in which the rolling element rides and how it relates to the outer ring’s outer diameter and the inner ring’s inner diameter as you rotate the bearing 360 degrees.
Inaccuracy can lead to serious issues but can be avoided by properly selecting the correct bearings and bearing class before use in your application. Face run-out is the variation in the axial distance of the side face (inner or outer rings) from the raceway.
Bearing run-out is controlled by the manufacturer and is subject to limitations based on the tolerance class. Therefore, it is important to select the right bearing tolerance class for your application. For instance, machine spindles typically have a tighter tolerance range for run-out than standard bearings.
Both the inner and outer rings have a specific tolerance range as defined by the American Bearing Manufacturers Association (ABMA)/International Organization for Standardization (ISO) Standard 20.
What Can Go Wrong with Bearing Run-out?
Incorrect run-out can cause a wide variety of issues, depending on the application. For example, if you have a machine designed to create specially aligned holes in a part, incorrect run-out could affect the proper placement of the holes, meaning those holes might not match up with the mating part.
In a motor application, you could face issues with vibration or noise. With spindle applications, run-out could force the drill on a lathe to be off-center or make a hole larger than required.
While bearing run-out is established based on the ABMA/ISO specification, the shaft and housings also must be controlled, as the bearing is only providing the motion relative to each. Many people mistakenly blame bearings for application issues when in fact it’s a housing and/or a shaft that is out of position.
Other times, the selection of an incorrect bearing class can lead to an issue. Consult with your bearing manufacturer to determine the correct bearing class for your application.
How to Measure Bearing Run-out
To measure run-out, you will need a few items, such as your bearing of choice, a mount like a V-block and a dial indicator. The dial indicator must be precise, as you’ll be measuring less than a thousandth of an inch in some instances. You can purchase more expensive measuring equipment, but they’re not always necessary. A good dial indicator and a block offer the simplest way to universally measure run-out on bearings.
For radial run-out, start by mounting the bearing so you can rotate either the inner ring or outer ring, depending on which raceway you want to measure. The dial indicator should be held perpendicular to the surface of the raceway. Apply a load to remove any gap between the raceway and the rolling element, and then rotate the ring at least one full turn to register a total indicator reading (TIR). The TIR is the difference between the high and low readings, and indicates the amount of run-out on your bearing.
This process can be used to measure multiple points on a bearing, including the inner ring or outer ring raceway-to-bore thickness variation, the radial run-out of the assembled bearing inner ring or outer ring, the asynchronous radial run-out of the assembled bearing inner ring, the raceway parallelism with the face (face run-out), and more.
Additionally, there are specific ways to measure radial run-out for different bearing types. Contact your bearing manufacturer to discuss the right method for your preferred bearing or refer to ABMA/ISO Standard 4.
Keep in mind that run-out shouldn’t change over time unless the bearing is starting to degrade and wear is beginning to occur. If you measure your bearings before they are installed and the run-outs are off, you will need to have a discussion with your bearing supplier.
Remember, even a thousandth of an inch can make a world of difference when it comes to run-out. Take time to specify the bearings for your applications. It’s also crucial to find a good bearing supply partner so you can avoid unnecessary run-out issues and have an expert to turn to in case you have questions. With quality bearings and proper measurement techniques, you can keep your applications running the way they should.
About the Author
Chris Wilson is the corporate operations manager at Ritbearing Corp., an international distributor of ball and roller bearings which also specializes in custom-engineered bearing solutions for unique applications. Chris can be reached at 1-800-431-1980 or cwilson@ritbearing.com.
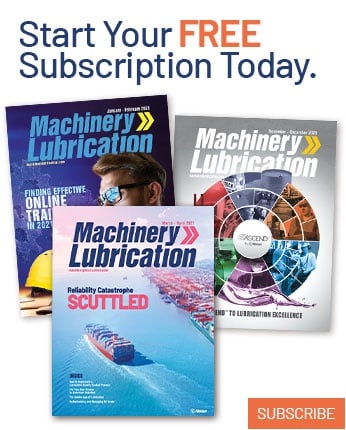