With there being a never-ending need for manufacturers to produce at reduced cost, all opportunities to improve output must be investigated and exploited to maintain a competitive advantage. One strategy in improving output is to review and address the conditions or events that restrict the output of production facilities, which is often referred to as bottlenecking.
Bottlenecking can occur in any aspect of a manufacturing process, from the supply of raw materials through to delivery of product to a customer, and the causes will vary significantly between industries and processes. An aspect of manufacturing where bottlenecking is often found is in the inability of the equipment to reliably produce the required output. Potential causes for this may be:
-
Physical, such as the equipment breaking down often;
-
Human, such as poor work practices; or
-
Latent, such as ineffective planning processes.
Maintenance and reliability issues touch on all of these potential causes. This article discusses what aspects of maintenance affect plant output, and then what actions can be taken to mitigate these negative effects.
The Reactive Maintenance Organization
A typical reactive maintenance organization displays the following characteristics:
-
The organization plans and schedules preventive work on the day the task is required.
-
Breakdowns are commonplace and are attended to at the expense of completing planned tasks.
-
Down days are not planned into the production schedule.
-
Documented planned maintenance tasks are few.
-
There are no dedicated maintenance planners.
-
Materials are not effectively managed.
-
Bills of materials are incomplete or don’t exist.
-
Operation security risks have not been assessed.
-
There is no structured system for development of maintenance plans.
-
Technical information is not well managed and often difficult to find.
-
Modifications to plant are made without applying a change management process.
-
Analysis of failures does not occur.
The equipment being maintained by organizations in this “reactive spiral” is likely to become less reliable over time because critical preventive tasks are not being completed and root cause of failures is not often addressed. At some stage in this reactive spiral, plant reliability may become a bottleneck in the production process.
Here’s how a reactive organization can generate bottlenecks.
Planning and scheduling
Terry Wireman is an author of a host of books that focus on maintenance. Terry claims that highly reactive maintenance organizations can spend as little as two hours per day on the tools, and unplanned work can cost up to five times the cost of a planned task. With tool time being so low, how effective will planned outages be? In reality, good planning and scheduling will improve tool time to at least six hours in an eight-hour shift. So in this instance, a previous eight-hour outage could be reduced to less than three hours. If your process is capacity constrained, then this will eliminate a five-hour bottleneck; however if capacity is not an issue, then up to three times as much work may be completed in the same time frame, effectively reducing the cost to maintain. When you apply this logic to a 12-month schedule of work and include some large multi-week shutdowns, it becomes clear that improving the planning and scheduling of maintenance work is well worthwhile.
Without going on to extensive detail, there are a few critical steps related to implementing effective planning and scheduling.
-
You have to accept that there is a need for change, and management must support the change.
-
Dedicated maintenance planners must be deployed whose sole task is to plan and schedule work (not execute it).
-
Detailed task lists have to be developed for all repetitive tasks.
-
Spares and bills of materials must be effectively managed.
-
A process must exist to manage work through the system.
-
Planned outages must be put in place, and this process must be locked in with production.
For those that want to head down this path or improve their current systems, there are many excellent texts and consulting organizations available that could assist.
Breakdown maintenance
Breakdown of equipment can be a significant cause of bottlenecks in production processes. There are fundamentally two forms of breakdown that create bottlenecks:
-
High-frequency, short-duration breakdowns
-
Extended-delay breakdowns
The effects of an extended delay are obvious; no production equals no output. But how often is the cause of the breakdown assessed with a view of eliminating the defect?
The high-frequency, short-duration breakdowns are far more sinister. Often, these types of failures are hidden as the operations staff has developed workarounds, such as following an unapproved procedure, cycling the power or slowing the process down. In time, the operations staff begins to accept these delays as being normal. Does your business measure how often these events occur and how much time is lost for each event? It’s one thing to understand what these losses are, but another entirely when it comes to eliminating these defects. Reactive organizations rarely find the time to address the root cause of any issues.
The key steps for reducing breakdowns and, hence, removing a potential bottleneck are:
-
Use your CMMS to record all breakdowns, no matter how small they are.
-
Use Pareto graphs to regularly assess the failure data to identify chronic reliability issues.
-
Determine which of these issues are causing the most significant losses or causing unacceptable bottlenecks. These issues will be the highest priority.
-
Determine which of these issues are particularly annoying to the operations personnel. There may not be significant financial gain in focusing on these issues, however it is likely to have a positive effect on motivation.
-
Utilize run charts to determine if improvements have been successful.
Planned outages
To maintain plant and equipment to an acceptable standard, it is vitally important that maintenance-related outages are valued and embedded in the production schedule. However, in reactive organizations, it is common to see down-day schedules changed or cancelled.
It is not desirable for maintenance work to be planned and scheduled, only to find on the day that the equipment cannot be put down due to production requirements. This indicates a fundamental issue with the production planning system, as missing critical maintenance may lead to chronic losses, which in turn will reduce output. There often is also a significant effect on the maintenance organization in that the well-planned job now has to be moved, and work has to be found for the previously scheduled workers. If the planned outage itself is causing a bottleneck, then the reason for the outage and allocated time need to be reviewed.
Maintenance strategies
Maintenance strategy is concerned with deciding how to maintain a plant, setting up an appropriate maintenance organization, establishing usable maintenance systems and directing the maintenance effort. Before you can plan and schedule, you have to have a maintenance strategy, because if you haven’t defined what you need to know, how can you plan what to do?
Well-constructed maintenance strategies will be unique for each type of equipment and will include a number of different activities which when applied will assist in ensuring that equipment can reliably meet its production requirements. Maintenance strategies generally fall into one of four categories:
-
Run to failure. This is a legitimate strategy when the implications of the failure are minimal or there is no way of predicting the failure. Lighting is an excellent example of this
-
Condition monitoring (vibration analysis, thermography, etc.). These technology-driven inspections are the preferred method for understanding whether equipment requires overhaul, as they are usually non-intrusive and can predict issues accurately. The theory goes, “If it’s not broken, don’t try to fix it”.
-
Fixed-time inspection/replacement. Fixed-time inspection is another form of condition monitoring, but it may require some intrusive work. Fixed-time replacement is used where the wearout rate of any item is well known (e.g. oil in a car).
-
Fixed-time overhaul. This should be a last resort for most organizations and should only be used when wearout rates are very well understood.
How maintenance strategies can create bottlenecks
In years gone by, when maintenance labor was plentiful, there were some very extensive planned maintenance programs in place, with most being based on the “best guess” of the experienced people in the business. The results were often a plant that was being over-servciced or the servicing was occurring on equipment that had very low failure rates. In the last 20 years, there has been a significant movement to actions being based on the mitigation of failure modes, using tools such as Reliability-Centered Maintenance or PM Optimization. The aim of these tools is to help ensure the right strategy is applied based on sound knowledge and data. The effect of this is that over-servicing is eliminated and the focus of maintenance is moved toward condition-based assessment, which generally can be completed on-line. Over-servicing leads to longer down periods, an increase in the incidence of premature failures, and can possibly create a process bottleneck. Having correctly developed and deployed maintenance strategies will mitigate this possibility.
There are two significant aspects of the maintenance organization that may have an effect on process throughput – the structure of the organization and the skill level of the members.
The optimum organizational structure
Ultimately, the aim of the maintenance department is to ensure that equipment can meet the output requirements of the business at the lowest cost. Leading from the earlier discussion, it is clear that the less reactive your business is, the more efficient and cost effective you will become. So, the organization needs to be heading toward a structure that supports planning, scheduling and good materials management practices. On the other side of the equation, the organization may need to be able to respond quickly to emergencies and then be able to have time to assess the failures. Ultimately, it is critically important that the structure in place helps support ownership of equipment and issues at a trade/craftsman level.
The ideal structure will be different for every business, but as a guide there should be:
-
A maintenance and reliability manager (may of may not be reporting to a production manager)
-
Maintenance planners/schedulers (ratio of around one for every 10 trades)
-
A reactive maintenance crew that deals with all breakdowns and unscheduled work
-
A maintenance crew that deals with planned, preventive and predictive maintenance
-
Condition monitoring and reliability engineering resources
-
Shutdown contract resources for work greater than the base load
Training and skill levels
Fundamentally, if your workforce does not have the skills to complete a task correctly, you will get a second-class result. Maintenance workers must have the appropriate tertiary training in their specific skill area, and the organization should ensure that the workforce is kept up-to-date with equipment and technology they have installed.
How the maintenance organization can create bottlenecks
An inadequate maintenance organization structure can create process bottlenecks. If your reactive crew is not resourced enough, then you may have equipment down waiting on repair. If there is little or no higher-level technical support, short delays could become much longer ones. When there are not enough people in your planned maintenance crew, or they are not trained correctly in completing a task, an eight-hour shutdown may become a 12-hour shutdown. All of these possibilities will reduce output and potentially create a bottleneck in your production process.
The steps required to help prevent your maintenance organization from creating process bottlenecks need to address both the organizational structure and training issues.
In relation to training, you will need to understand what skills your team requires to maintain the plant. This will have to be matched against the current skills set and the gaps identified. From this, available training programs will need to be developed and a training schedule built.
With the organization structure, it is important to understand your current work patterns. How much of your current load is reactive vs. proactive? Are you not completing all required maintenance work? This information will help you understand where the labor should be placed and may highlight areas where not enough labor is available. If you are moving to or improving your planning and scheduling, the split between reactive and proactive will have to be reassessed as your systems improve. The ultimate aim is to have a less reactive workforce.
Conclusion
If your process bottlenecks are linked closely to the maintenance and reliability of your equipment, it is most likely you have a highly reactive maintenance organization. To move from a primarily reactive regime, significant focus must be placed on developing and deploying systems that move the organization toward being proactive. This requires effective planning and scheduling, well-developed maintenance strategies, a detailed work management process, a skilled workforce that is resourced adequately, a process to determine and rectify the root cause of failures, and a good materials management process. In reality, all of these traits are commonly accepted as being best practice, and the application of them will limit the maintenance and reliability of equipment being a cause of process bottlenecks.
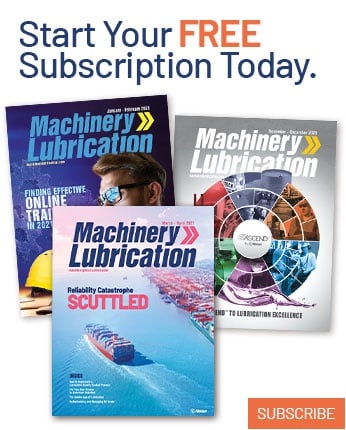