Roanoke Cement, a Timken customer for more than a decade, lost 30 percent of their production when their roll press went down unexpectedly – causing major operational problems.
The Solution
To assess the problem and get the roll press operational as quickly as possible, Timken assembled a team of experts and placed key engineers on-site at Roanoke to develop a customized solution.
“Timken has the most reliable field service any mill could ask for,” said Moe Petty, maintenance supervisor at Roanoke Cement. “From the sales representative to the engineers, they supported our mill through the situation to restore the unit to full operation. I know Timken service is excellent because there’s a true partnership to provide the custom solution for our mill.”
Timken and Roanoke Cement worked together over several weeks to:
- Inspect the raceway surfaces and a section of outer ring from a roll press bearing.
- Assist with the removal of a double row spherical roller bearing from the roll press.
- Assist with reconditioning a damaged housing.
- Assist with on-site installation of a replacement bearing reconditioned by Timken.
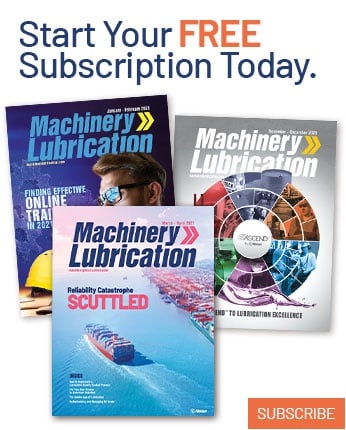